Enamel Steel Tank
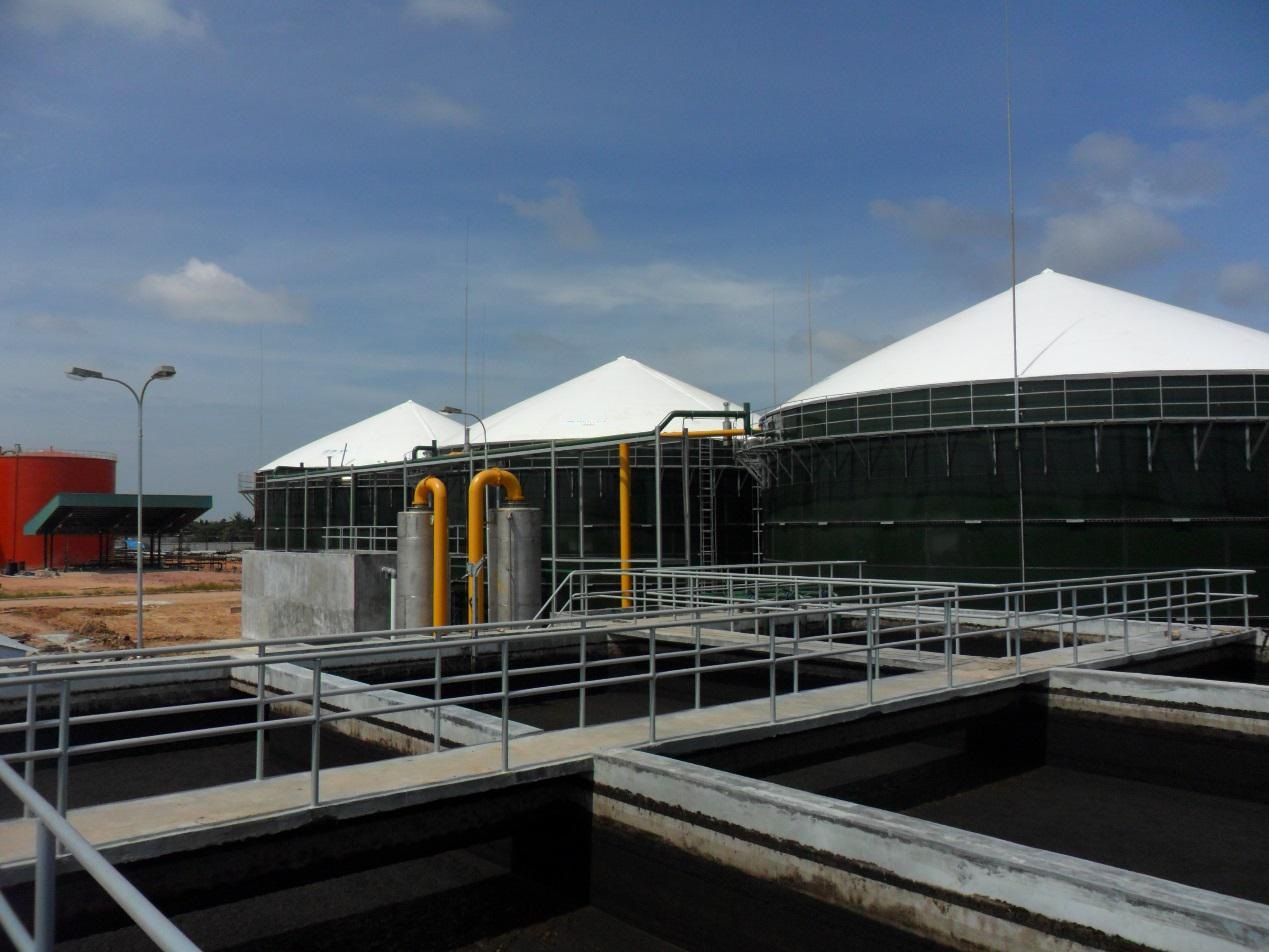
Our factory of enamel steel is the production base in China, the location of birthplace of hot-rolled steel with double-sided enamel. While it’s the largest and most professional supplier for enamel assembly tank in China, with nearly 30 years of experiences in manufacturing enamel steel. Products are enjoying high reputations internationally, being exported to the United States,Russia,Asia and Africa etc.
Specifications of Enamel Steel Plate:
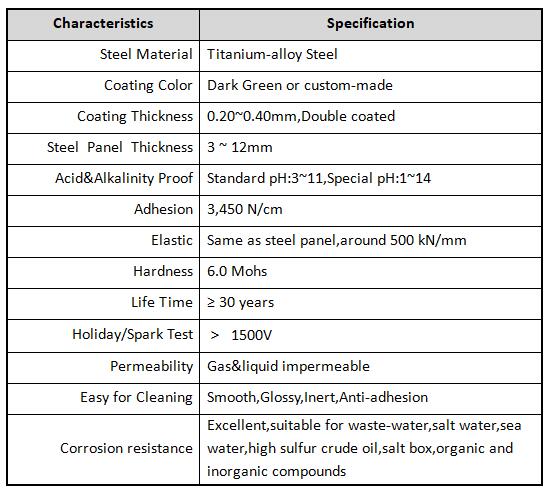
Tank is equipped with the auxiliaries below for a complete reactor:
1.Double-membrane Gas Holder.
Mounted on top of tank as all-in-one solution of biogas production&storage,the outer&inner membranes of gas holder would be fixed tightly by stirrups around tank;2.Stirring System.
It makes biomass complete contact with microorganism. Three types of stirring methods: Mechanically, Hydraulically and Gas. Among of them,mechanical agitator is the most popular, has three kinds of installation: Vertically,Inclined entering and side entering.3.Pressure Protector.
To avoid damages for tank and gas holder resulting from too high or too low pressure inside tank;4.Heating Coils.
Made of Stainless Steel in tube form,it spirals around inside wall of tank. Hot water from CHP or boiler to be used for tank heating through heating coils.And water after heat exchanged would return to CHP or boiler,as a complete water circulation;5.Three-phase Separator.
It is required for UASB/EGSB/IC types of digesters with feedstock of low solid content, to achieve separations of “gas”, “liquid” and “solid”;6.Sensors, Monitoring Devices.
According to actual process requirements, liquid level sensor,temperature sensor,ph sensor,gas pressure sensor and leaking alarm can be installed or integrated into the PLC monitoring system together with biogas analyzer,flow meter etc;7.Insulation Layer.
For projects located in cold area,heat insulation layer would be installed outside of tank,to keep warm and avoid heat leaking,to guarantee the fermentation temperature;8.Ancillary Equipment:
Feeding system, discharge system, biogas output pipe, the center support, ladder, casing, manhole, lightning rod, electric control cabinet, blower. Etc.Common Dimensions:
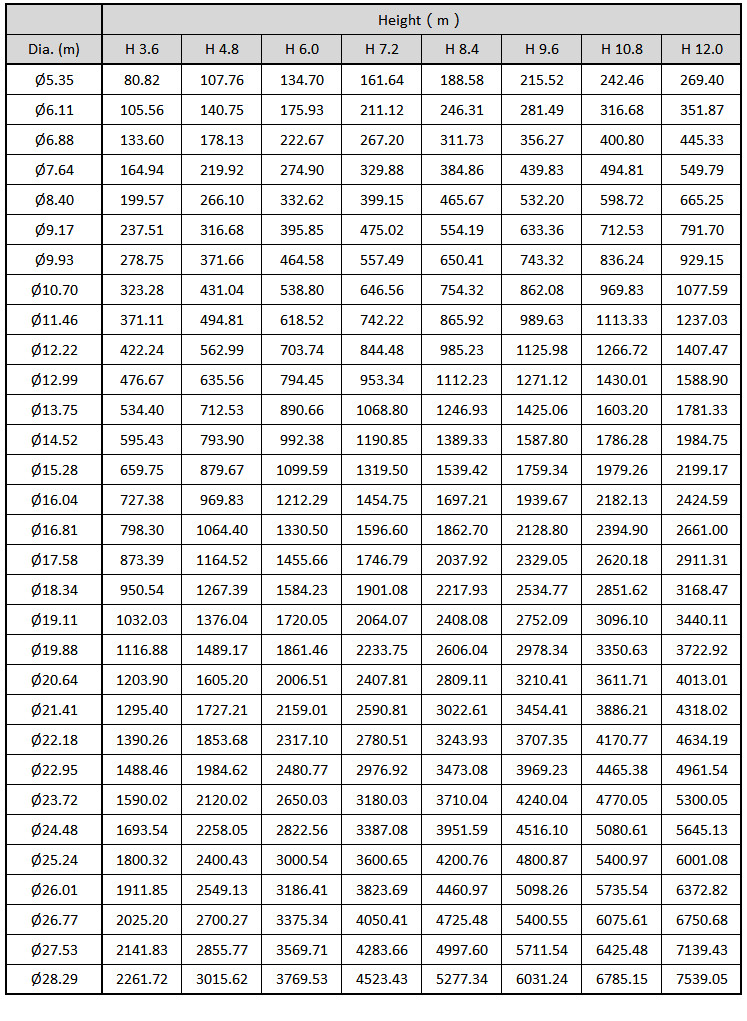
LIPP Tank
Technology of LIPP tank is originated from German, a kind of unique construction method. When tank erection, a certain width of steel plate is rolled by uncoiler and then delivered to molding machine for further processing into geometric shape as required. Then through the bending machine for bending and seaming to form a 30~40mm width of continuous spiral cord around the outward of tank, this structure plays the role of strengthening the tank. The bending for two different materials is also possible through the above machines.
Characteristics of LIPP tanks:
1.Good overall performance and long life-time
The complete construction process is completed by special machine at project site. The bended and seamed spiral cord is five times thicker than material, greatly enhanced the carrying capacity of tank, so that the tank overall strength, stability and shock resistance are all better than other kinds of tanks. In addition, it uses a particularly good anti-corrosion properties of material, which makes it life-time longer than other tanks.2.Good airtight performance and wide applications
Bending and seaming of steel plate by special machine to ensure the quality of any part of tank, so its sealing is particularly good, especially suitable for tank type wet anaerobic fermentation in the filed of biogas energy.3.Short construction period and low cost
LIPP tank is on-site building, tank cover is made on the ground. Line speed of molding&bending can reach 5meters/min, set-up of scaffolding and other auxiliary facilities is not required, so as to make construction period very short. Main material is thin steel plate, its weight is only equivalent to the rebar of reinforced concrete tank, this greatly reduces the cost for tank.4.Small area occupation and easy management
Unlike other steel tank, LIPP tank can be in different dimensions, its diameter and height can be arbitrarily selected in a large range. The distance between two tanks can be minimized at 500mm, space can be fully used. Due to high automation of tank, if coupled with sensors of temperature, feedstock level,etc. management would become very convenient.Anaerobic Lagoon
HDPE Enclosed Anaerobic Lagoon type of Digester, membrane material is HDPE(High Density Polyethylene), is a kind of cheap solution for anaerobic fermentation.Structural features are as follows:
1.This kind of digester is a regular trapezoidal lagoon; Lagoon surface and bottom are rectangular (Surface is large, bottom is small); The trapezoidal slope is designed at generally 30 degrees to 45 Degrees according to actual volume of lagoon.2.The bottom of lagoon is anti-seepage treated by using HDPE geo-membrane in conformance to USA GRI quality standard and ASTM testing standards. Membrane thickness is mostly at 1.0 mm;
3.The top of lagoon is covered by HDPE geo-membrane with the same standards as above, and a certain volume of space reserved for biogas storage, about 3~4 meters higher above ground level of lagoon when it’s full of biogas. Membrane thickness is mostly at 1.5 mm;
4.Stirring and TS% regulation of feedstock are implemented before fed into lagoon. Wells for pipeline, waste input&output, digestate discharging are distributed around the lagoon. Stirring mechanism,heating devices,pumps,Pipeline,Valves and Connections are embedded underground. Biogas pipe would be fixed on the outer HDPE membrane;
5.The packaged HDPE membrane is rolled with 6~8 meters width, thermowelding process on site to make individual piece of membrane welded together. The foundation of lagoon would pressed tightly, and make sure that no sharp objects to damage the membrane. The top membrane is fixed tightly by using special anchoring devices.
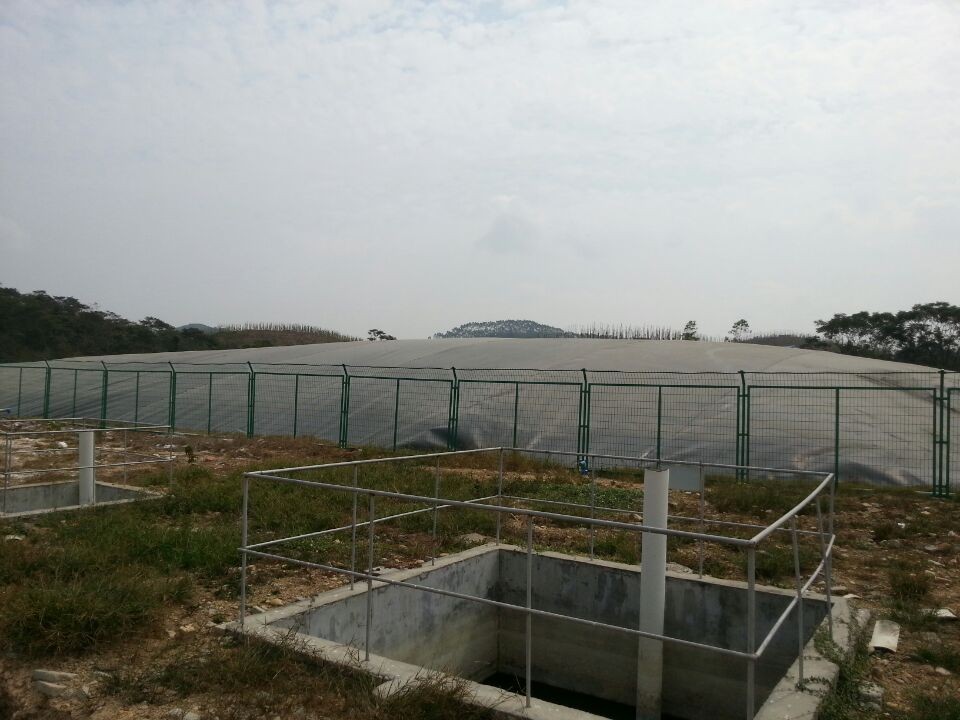
Because of its following characteristics, the HDPE M.E.A.L has been widely spreading internationally, especially in Southeast Asia, South America and Africa:
1.Low construction cost, less investment, average cost per m³ is about US$ 4~10;2.Construction is simple, convenient with short installation time;
3.Long HRT(Hydraulic Retention Time) and WRT(Waste Retention Time), high COD/BOD removal rate,resulting in clean liquid output;
4.HDPE membrane has good heat absorption performance to cause high gas production, especially for areas with high ambient temperature.
5.Large storage volume, all-in-one solution for fermentation and biogas storage;
6.No limits by the structure, single lagoon volume can be up to 60,000 cubic meters;
7.Low operating costs, low power consumption, simple operation.
Commonly Dimensions:
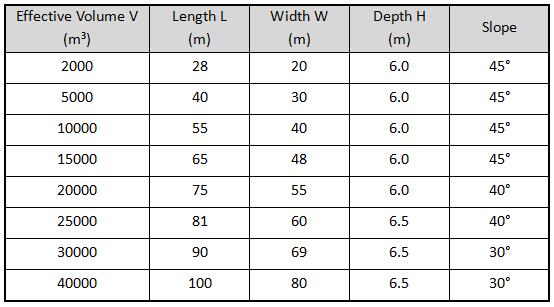
Comments:
The above dimensions would be changed without notice and Bigger dimensional lagoons are available.
Floating Soft Digester
The floating cover of digester is made of reinforced PVC membrane or coated fabric. The edges are double-sided welded, crossed by iron wire or plastic tube to be fixed at bottom of digester.Household type digester is always in the dimensions of diameter 1~3 m with height 1~1.5 m, cylinder or rectangular shaped; Industrial type is 3~4m width, arch height at 1~1.6m and length at 4~15m, single or multiple numbers in parallel.
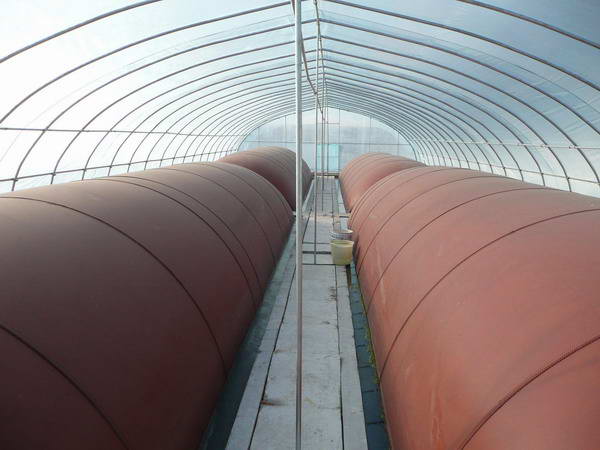
Characteristics of floating soft digester:
1.Excellent heat absorption
Fermentation temperature is the key factor, at least 15 degree.C required by this technology. This modified membrane could absorb heat from sunshine for improvement of biogas production.2.Strong pressure resistance
For digester of reinforced PVC membrane, operation pressure could be up to 3 kPa; For PVC coated fabric, it can reach 8 kPa; What’s more that the digester is equipped with pressure protecting mechanism.3.Good air tightness
The floating cover is hot-welded by multi-functional high frequency welding machine, with perfect performance of air tightness, in line with the requirements of anaerobic fermentation.4.Perfect stretchability
The reinforced PVC membrane is flexible, enables floating cover to expand about 10% larger.5.Strong weather appliability
The membrane chose is a kind of modified PVC alloy material, with good stability, can be antifreeze (-25 Degree.C) and anti-exposure(+50 Degree.C). It is also acid&alkali resistance, lightning protection, earthquake resistance and tear resistance. Life-time can reach 12~15 years.6.Easy operation&maintenance
It is easy to learn and master the complete processes. Short time of training enables worker to achieve a comprehensive grasp how to operate and maintain the whole digester.Free-standing Gas Holder
Free-standing double-membrane Gas holder,In 3/4 spherical shape, installed on the ground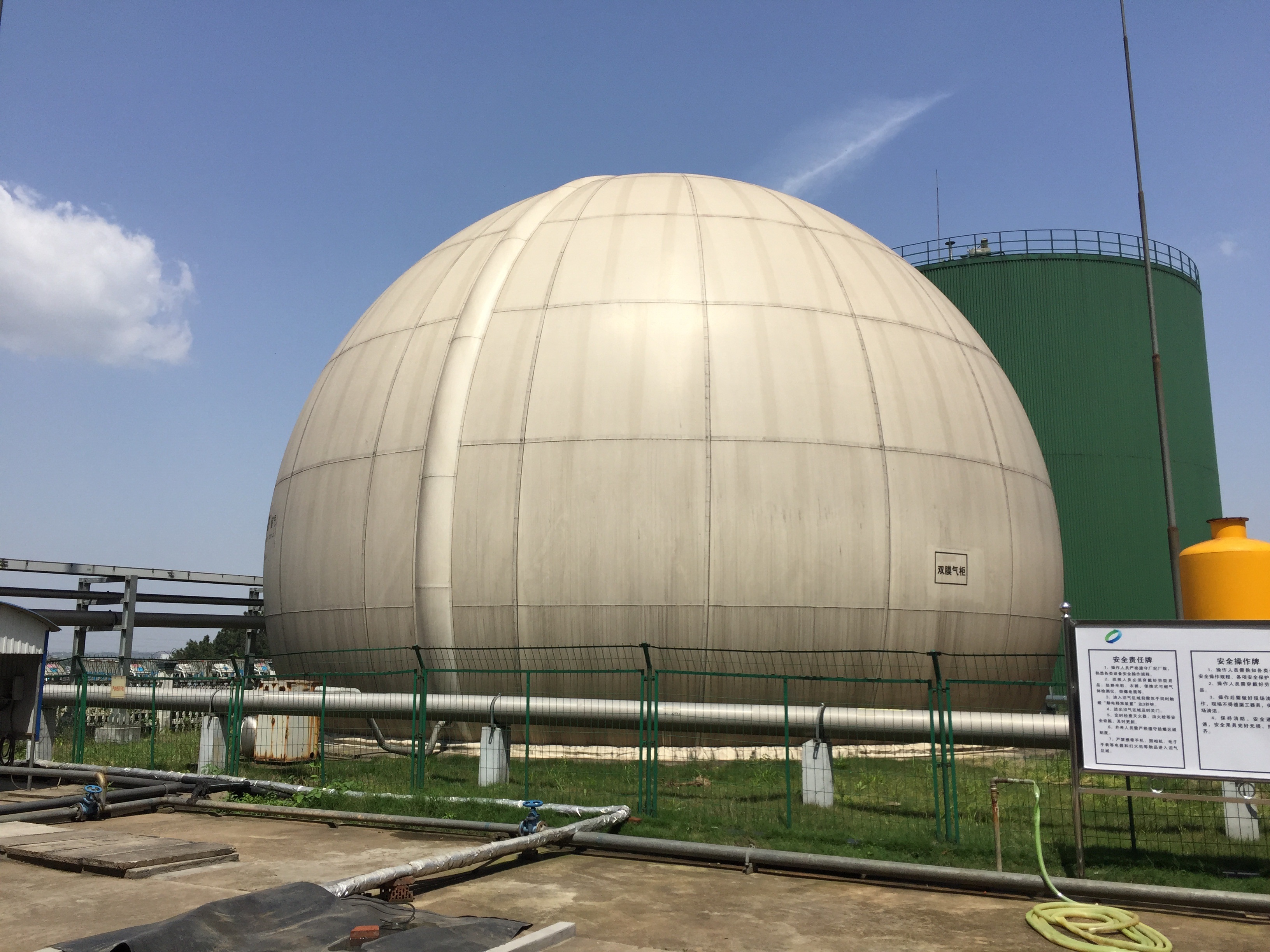
Main structural features:
1.Bottom membrane. For sealing of the complete gas storage system;2.Inner membrane. For partition of biogas and air and pressure regulation;
3.Outer membrane. For biogas output under constant-pressure and protection for inner membrane;
4.Electrical control cabinet. For making constant pressure in the room between Inner and outer membrane;
5.Safety protector. For air release when pressure is too high in the room between the inner and outer membrane;
6.Explosion-proof blower. For air pumping;
7.Anchoring device. Including press plate, anchor bolts, etc.;
8.Support device. Including middle bar, support network, seat belts, etc.;
9.Detecting device. Including mirrors, sensors, etc .;
The membrane quality and production process determines the quality and life-time of the entire gas holder. We can provide Germany-made, Belgium-made membrane, or Mainland-made, Taiwan-made membrane, to meet the following features:
1.Anti-aging;2.Strong tensile strength;
3.Anti-corrosion for sulfide etc;
4.Anti-ultraviolet;
5.Alkalinity Resistance;
6.Good softness;
7.Compound tight, good air tightness.
Parameters Table for Selection
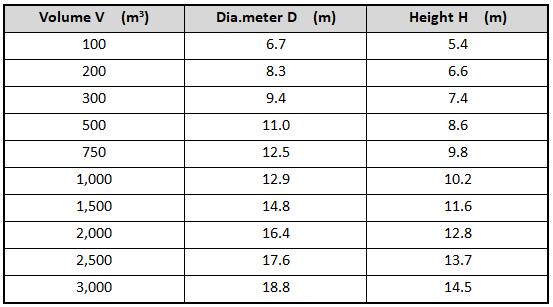
Comments:
The above are standard dimensions,subject to actual requirements and bigger sized gas holders are available too.
Integrated Gas Holder
Integrated double-membrane Gas holder,mounted on top of digester for ALL-IN-ONE design
Main structural features:
1.Inner membrane. For partition of biogas and air and pressure regulation;2.Outer membrane. For biogas output under constant-pressure and protection for inner membrane;
3.Electrical control cabinet. For making constant pressure in the room between Inner and outer membrane;
4.Safety protector. For air release when pressure is too high in the room between the inner and outer membrane;
5.Explosion-proof blower. For air pumping;
6.Anchoring device. Including press plate, anchor bolts, etc.;
7.Support device. Including middle bar, support network, seat belts, etc.;
8.Detecting device. Including mirrors, sensors, etc .;
The membrane quality and production process determines the quality and service life-time of the entire gas holder. We can provide Germany-made, Belgium-made membrane, or Mainland-made, Taiwan-made membrane, to meet the following features:
1.Anti-aging;2.Strong tensile strength;
3.Anti-corrosion for sulfide etc;
4.Anti-ultraviolet;
5.Alkalinity Resistance;
6.Good softness;
7.Compound tight, good air tightness.
Parameters table for Selection:
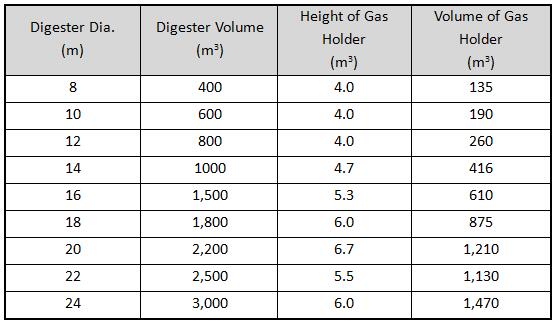
Comments:
The above are standard dimensions,subject to actual requirements and bigger sized gas holders are available too.
Biogas Storage Bag
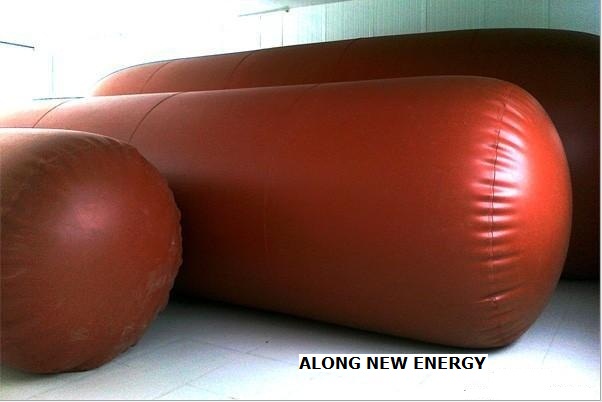
Single-membrane Biogas Bag
Made of reinforced PVC membrane,Thickness 0.6 ~ 1.8 mm available. Individual loading capacity is up to 400 m³ ; Maximum operation pressure is up to 3 KPa.
We accept custom-made orders in accordance with clients’ specific requirements on the total volume and dimensions.
Specifications of PVC composite membrane
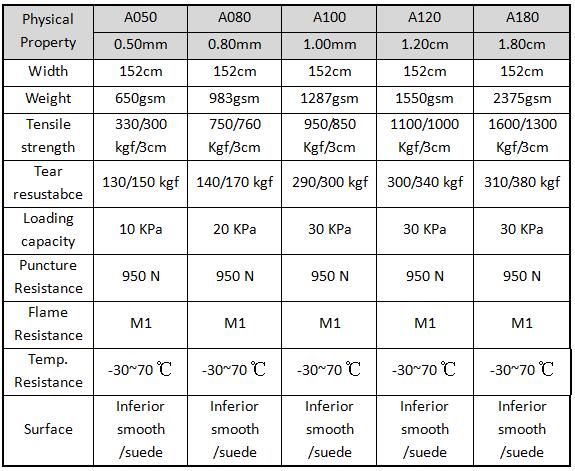
Specifications of PVC coated fabric membrane
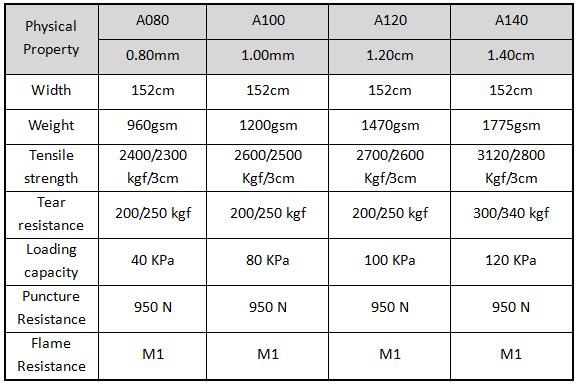
GasCle System
Our GasCle system is for the pre-treatment of raw biogas from anaerobic reactor, suitable for biogas flow 20 ~ 300 Nm³/hr. The raw biogas from digester always contains saturated water vapor, physical impurities and hydrogen sulfide. These substances should be removed before the utilization of biogas, to avoid damage to generator, burner of boiler and torch or other equipment.
The GasCle system is skid mounted in combination of multiple functional units, or individually installed at project site.
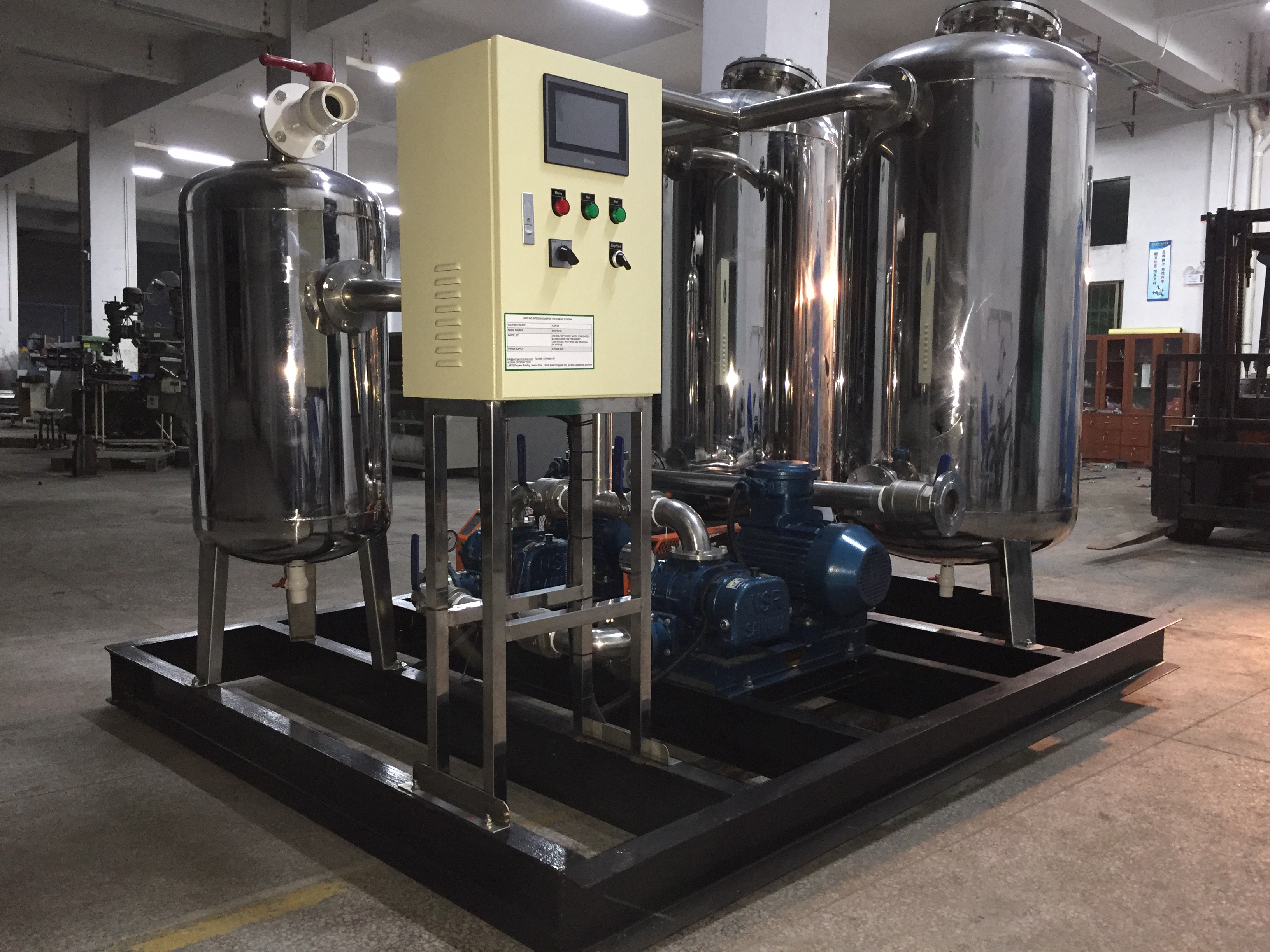
GasCle system has the following modules:
1.Primary filter (optional)
For preliminary removal of physical impurities and saturated water vapor;2.Desulphurization tank.
For reducing the hydrogen sulfide content in biogas, to meet the requirements of follow-up equipment;3.Secondary filter.
For Precise removal of physical impurities in the biogas and moisture;4.Biogas blower
Increasing biogas pressure for transportation and meed the requirement of follow-up equipment for gas intake pressure;5.Electrical control system
Equipped with VFD(variable frequency drive) and LCD touch screen.6.Pressure gauge and H2S analyzer(Optional).
7.Pipes, valves and base frame.
GasCle system has the following functions:1.Desulfurization
Hydrogen sulfide can be reduced to 50ppm or less;2.Dehydration
Removal of saturated water vapor;3.Impurity removal.
Removal of physical impurities and volatile matter of desulphurizer agent;4.Pressure increasing
Increment could reach 39.8 kPa or even higher;5.Pressure stabilization
Stabilizing gas outlet pressure at a fixed value to meet the gas intake pressure requirement of the follow-up equipment;6. Measurement of Pressure and hydrogen sulfide content (optional);
7.Digital display.
Pressure setpoint, gas outlet pressure, motor frequency, motor speed, motor current, output torque, bus voltage, output voltage, power consumption and system operation time would be indicated on the LCD display.GasPro System
Our GasPro system is for the pre-treatment of landfill gas or desulphurized biogas of other sources, suitable for gas flow 300 ~ 5,000 Nm³/hr, with main functions of dehydration, dehumidification, edulcoration, boosting, pressure-stabilization, thermoregulation, automatic/remote controlling and on-line detecting,etc.
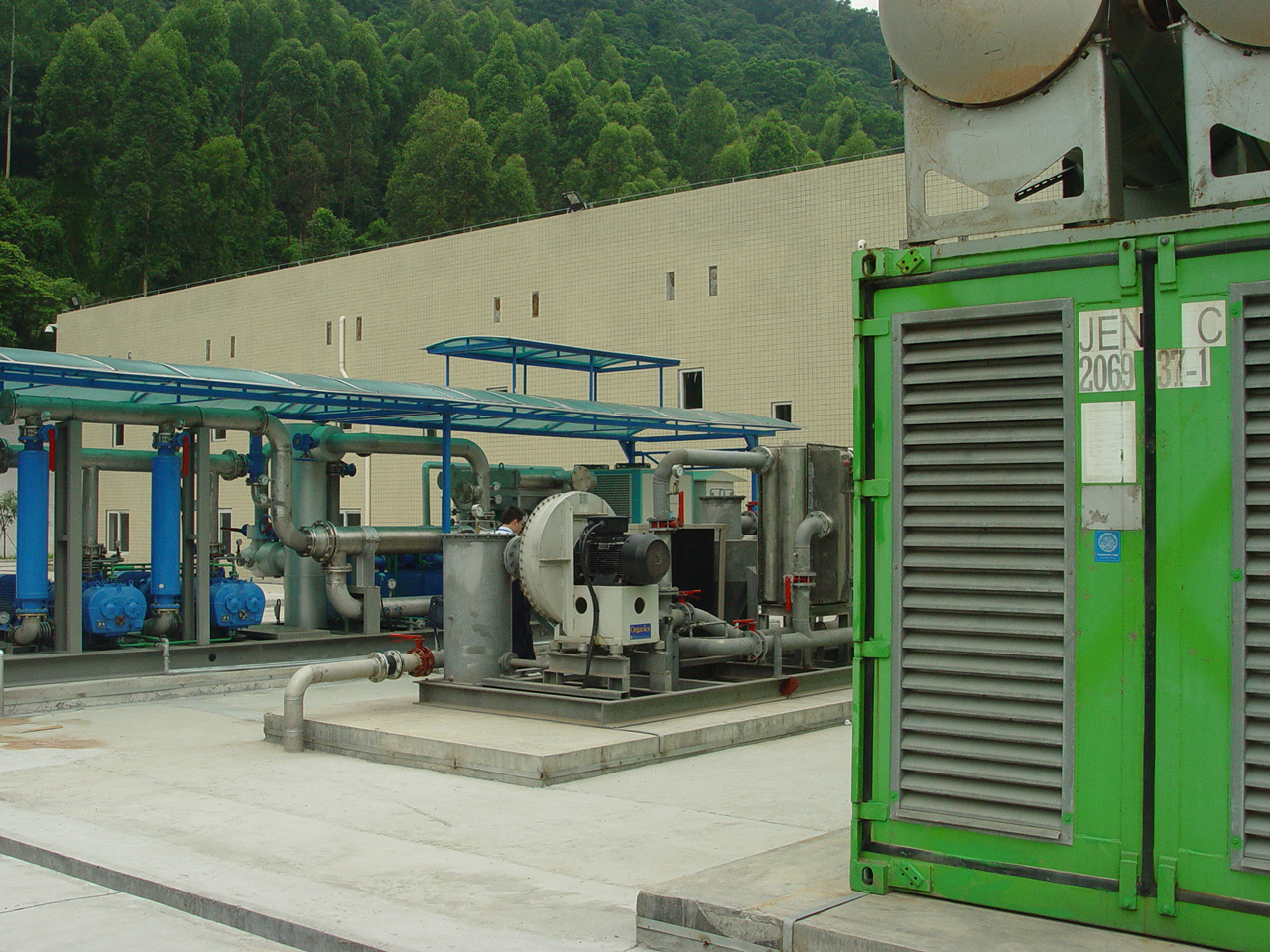
b.Multi-stage dehydration could reduce the temperature of gas dew point,as well as the water vapor content;
c.Freezing function for condensation and precipitation of harmful gases;
d.Adjusting gas temperature in proper condition to feed engine;
e.On-line detecting system for measuring gas composition timely(optional);
f.Advanced control system could stabilize the gas outlet pressure and temperature;
g.The gas flow is automatically tracked rooted on the requirements of engine;
h.Equipped with alarms and protections for over-pressure and over-temperature, to ensure safe and reliable operation of system in the long-term;
i.This matched system could make engine runs under condition of fixed thermal value, to improve the stability of engine operation and protect the gas collector.
The technological process of GasPro system:
The landfill gas or other biogas, after cleaned through our GasPro system, could be in a proper condition for the use of generators. The stability of outlet pressure can be realized through the combined effects of automatic control system and blower.
Flow-chart of GasPro system for converting landfill gas: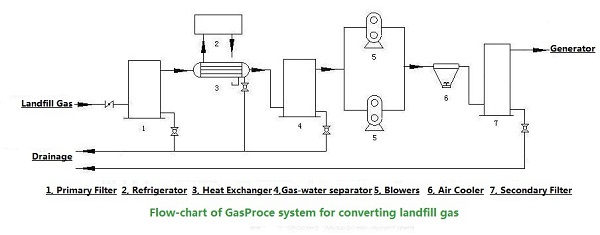
1.Dehydration, Dehumidification, Edulcoration
The relative humidity of raw landfill gas is 100% to be fed to GasPro system. Through the high efficient primary filter, water spray and physical impurities are removed, water content becomes saturated and dust size less than 50μm, meanwhile the hydrogen sulfide, ammonia and other harmful gases are dissolved in the condensate, to be discharged out of system.Subsequently, the saturated gas goes into deep cooling system. Its temperature drops down to 10~15 degree.C after cooled in the shell and tube heat exchanger. The moisture, dust and harmful gases can be removed further in the condenser. The relative humidity of gas gets out of condenser could reach 80% or even lower to satisfy the requirement of generator on water content.
The separation of condensate water occurs in the gas-water separator.
2.Pressure increasing, Pressure stabilizing and Thermoregulation
①Pressure increasing
Taking into considering the gas refining, the need of power generation and investment control, commercial solution is the use of roots blower for gas delivery and meeting the requirement of inlet pressure of generator.②Pressure stabilizing
Roots blower is controlled by frequency converter. The gas pressure signal from outlet of system is fed back to PLC, to regulate the output current of frequency converter, to change the speed of motor of roots blower, by this means to regulate the gas flow in the range of 20 ~ 100%. Not only the manifold pressure can be stabilized, but also the power consumption of system could be regulated in accordance with the load fluctuation, to avoid the rise of power consumption of system.③Thermoregulation
The cooled gas from condenser goes through roots blower, after that, its temperature would rise naturally. Then flows into air cooler for cooling again. In this way, the gas temperature would be adjusted well to be fed to generator.3.Secondary Filtration
The final step of GasPro system is the secondary filter. Filter element is stainless steel material, with enough filtrating area. The micro-sized impurities could be effectively removed, to achieve the purpose of fine separation.4.Automatic Drainage
Condensate water would be generated resulting from the cooling of the pipeline and equipment of GasPro system, and it can be discharged out of system automatically.5.Automatic Controlling Process
GasPro system uses proframmable controller - PLC control, with functions of data acquisition, on-line detection and alarm. Standard communication interface to be provided in synchronization with the owner’s control system per clients’ requirements, to achieve the purpose of unattended and fully automatic operation:①A programmable PLC controller for data acquisition and processing;
②With function of remote data transmission;
③Through standard industrial Ethernet to read data when system in operation;
④Site controlling mode at local engineering station by the use of LCD touch screen. Through data transmission to achieve the purpose of remote controlling, eg. start/stop signal;
⑤The use of professional computer for processing of data and signal. Configuration software and past records are stored in the hard risk of computer;
⑥Within authorized scope, engineer could modify the parameter settings of alarm and shutdown.
Dry Desulphurization Tower
Dry chemical desulphurization is a simple, efficient and low-cost solution for removing Hydrogen Sulfide in biogas, generally suitable for low-flow biogas with low Hydrogen Sulfide content. Main principle is that H2S is oxidized by O2 to sulfur or sulfur oxide, so it is also known as dry oxidation process.
The process is structured as a cylindrical container with chemical fillings inside, which are activated carbon or ferric oxide, etc. The raw biogas at low velocity goes through the filling layer, then hydrogen sulfide would be oxidized to sulfur or sulfur oxide, which remains in the filling layer. And the purified biogas flows out of tower at upper position.

We call this cylindrical container as tower, material is carbon steel or stainless steel, wall thickness is 4 ~ 10 mm available, diameter varies in the range of 440 ~ 5000 mm, and height of tower is 1.0 ~ 10 meters available. It’s a kind of nonstandard equipment, actual dimension would be subject to gas flow and hydrogen sulfide content in the raw biogas.
Main equipment is the steel-structure tower, filled by desulphurizer agent, equipped with observation window, pressure gauge, thermometer and other components. There are usually two towers to be used alternately, one for operation while the other for regeneration. When biogas flows through tower down-up, below chemical reactions would occur:
Desulphurization agent (Ferric Oxide):First-step: Fe2O3•H2O + 3 H2S = Fe2S3 + 4 H2O (Desulphurization)
Second-step: Fe2S3 + 3/2 O2 + 3 H2O = Fe2O3•H2O + 2 H2O + 3 S(Regeneration)
The biogas containing hydrogen sulfide reacts firstly with the high-loading desulphurizaer agent near the bottom entrance. The upper filling layer is low-loading agent. By means of well-designed biogas airspeed and line speed to reach fine desulphurization effect.
It’s better to install a primary filter before the process of desulphruzation, to remove physical impurities and make biogas with a certain humidity.
When the desulphurizer agent in the running tower is observed discolored or the pressure loss is too big, the other tower should be used alternately. Natural ventilation for the current tower after biogas emptying for regeneration of desulphurizer agent. When regeneration result is not good enough for reuse, a replacement for the old agent would be processed through the bottom outlet and the same amount of fresh agent is filled into tower.
Wet Desulphurization Tower
Wet desulphurization technologies include physical absorption, chemical absorption and chemical oxidation. The need of reprocessing hydrogen sulfide of Physical and chemical absorption restrict their applications in actual projects. The widely used method is chemical oxidation, with alkaline solution as the absorbent and oxygen carrier as catalyst. The alkaline chemicals dissolved in water and goes into tower to contact with hydrogen sulfide to make oxidation reaction with elemental sulfur generated. The desulphurization efficiency of mature chemical oxidation method can reach above 99.5%.

For large projects, the desulphurization process is usually the combination of wet and dry types. Wet type is for the primary filtration while dry type for the fine desulphurization.
The wet desulphurization tower is composed of scrubbing tower, H2S sampling and monitoring system, alkaline solution deploying groove, softening water feed device, liquid level control system, supports and connection fittings. Automatic operation would be achieved through the monitoring of outlet hydrogen sulfide content and Ph value.
When system in operation, raw biogas gets through tower in the bottom-up flow, while the Na2CO3 solution(or NaOH solution) sprays into tower from the top down, by this means the complete reaction occurs between H2S and alkaline solution. The liquid is gathered in the bottom groove of tower, with automatic addition by metering pump by means of the monitoring of H2S concentration at outlet.
Main reaction mechanism if take Na2CO3 as alkaline chemicals
1.Absorption:H2S + CO32- = HS- + HCO3-
2.Oxidation Separation of Sulfur:
HS- + [Catalyst]•O = OH- + [Catalyst]•H
3.Regeneration:
[Catalyst]•H + O2 = [Catalyst]•O
OH- + HCO3- = CO32- + H2O
Biological Desulphurization Plant
Process Description:
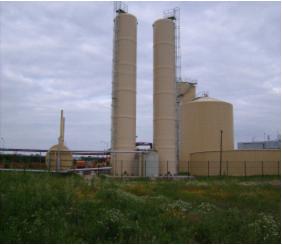
A certain amount of air is led to mix with raw biogas. The H2S would be removed in the biological desulphurization tower when mixed gas gets through it. Special plastic packings are installed inside the reactor to provide sufficient space for the propagation of bacteria. The circulation of nutrient solution keeps the packings wet and supplements nutrients required for the growth and reproduction of the bacteria. Exclusive species (such as Thiothrix or Thiobacillus) live and breed on the nutrient in the packings. By this means, they absorb H2S from the mixed gas and convert it into elemental sulfur, which then is converted to dilute sulfuric acid.
System Configuration
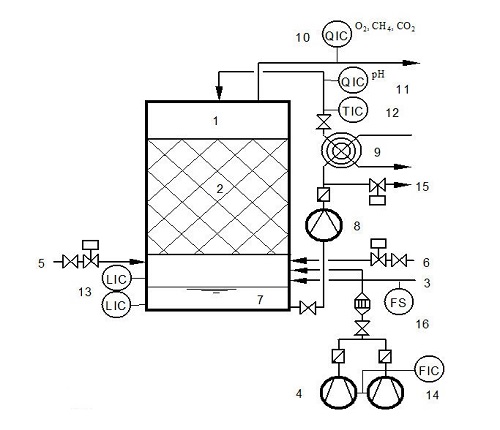
2. Packings
3. Biogas feed
4. Air supply
5. Nutrient solution supply
6. Dilute water
7. Circulating liquid
8. Nutrient Pump
9. Heat exchanger
10. Biogas analyzer
11. pH controller
12. Thermometer
13. Nutrient level controller
14. Air flowmeter
15. Spend nutrient solution
16. Flow switch
Biogas flows into reactor at bottom, across the packings and reaches the top. Addition of air into reactor is controlled precisely by frequency converter. Gas analyzer does detecting of concentration of oxygen remains, while reacts in accordance with air blowers. Circulating liquid is sprayed into reactor through circulation pump. The integral balance of liquid level is controlled by liquid-level switch. The maintenance of best activity of bacteria is achieved by means of system temp. regulation through heat exchanger and temp. monitoring. PH analyzer is used for controlling the acidity and alkalinity of nutrient solution, for example, when pH value is lower than the set point, fresh nutrient solution and dilute water are automatically added into reactor, meanwhile the spent solution is discharged automatically, by this means to keep the balance of liquid level.
Activated Carbon
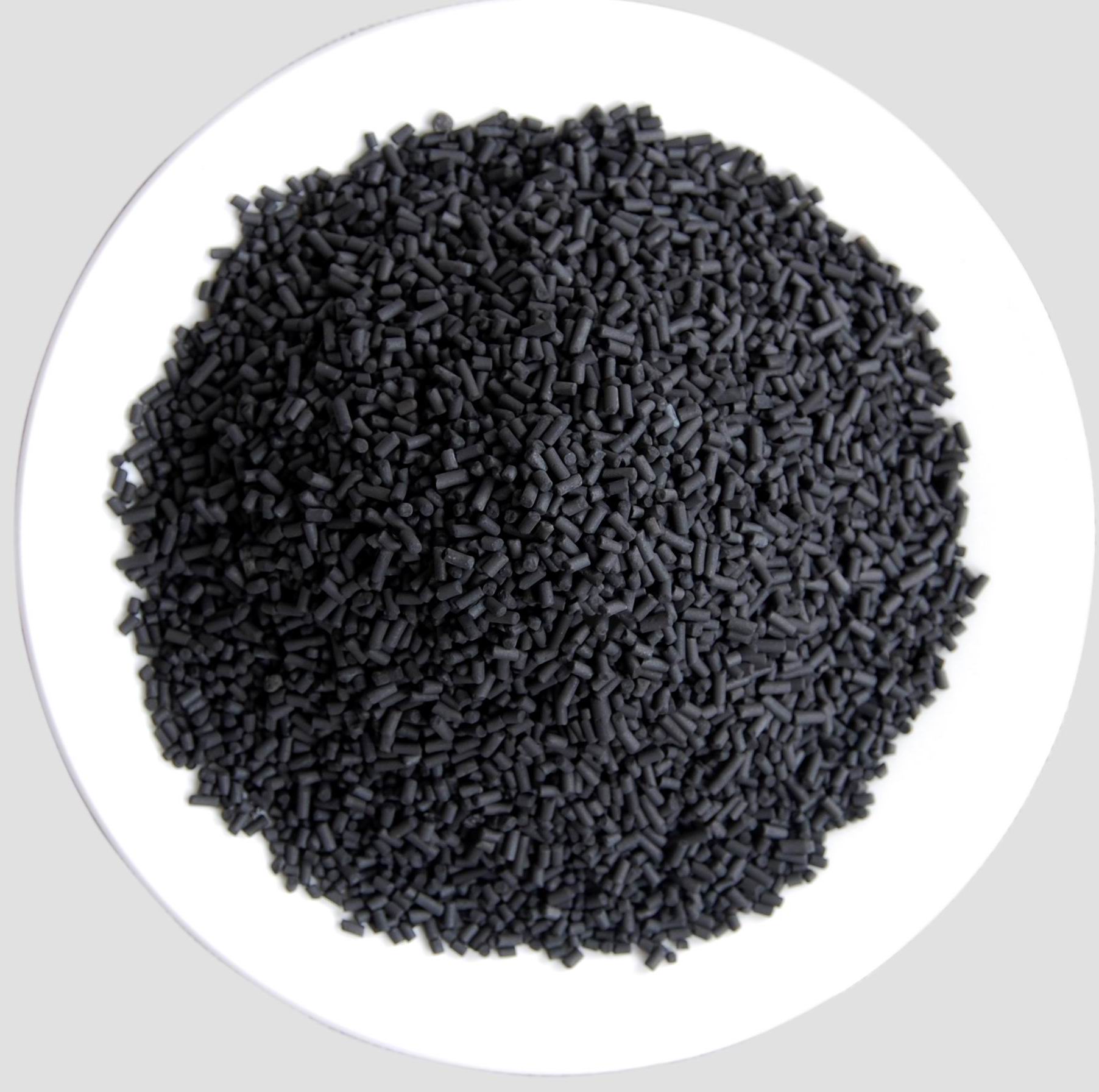
Product Description:
RY series of activated carbon has features of big surface area, developed microporous, wear resistance, anti-pressure&high temperature, fast adsorption, deep purification, without powder, long service life.The product is mainly used for the removal of H2S from various gases,like biogas, coke oven gas, natural gas, carbon dioxide gas, city gas, chemical feed gas and filtration and purification of impurities.
Technical datas:
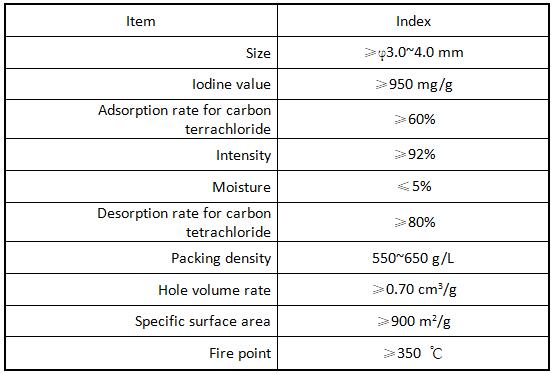
Comments:
Granularity and quality technical indicators can be set according to users’ specific requirements;
Ferric Oxide
Main components of desulphurization agent for biogas purification:Ferric oxide (Fe2O3.H2O).
Introduction:
MT-1 type desulfurization agent, whose main compoents is Ferric Oxide, is processed together with a variery of different accelerators. With Features of high sulfur capacity, deep purification, good strength, anti-water and good regeneration. Hydrogen sulfide can be removed even with the absence of oxygen and ammonia. Meanwhile a certain amount of organic sulfur can also be removed.MT-2 type desulfurization agent is produced under advanced production process based on the MT-1, adding a small amount of high activity components, with characeristics of high desulfurization accuracy, fast reaction rate, a wide range of desulfurization and high sulfur capacity under anaerobic conditions.
MT series of ferric-oxide desulfurizer is mainly used for water gas, semi-water gas, coke oven gas, biogas, natural gas, LNG, oilg and other gases in the fileds of city gas, fertilizer, coking, citric acid, winery, metallurgy, textile, light industry and electronics.
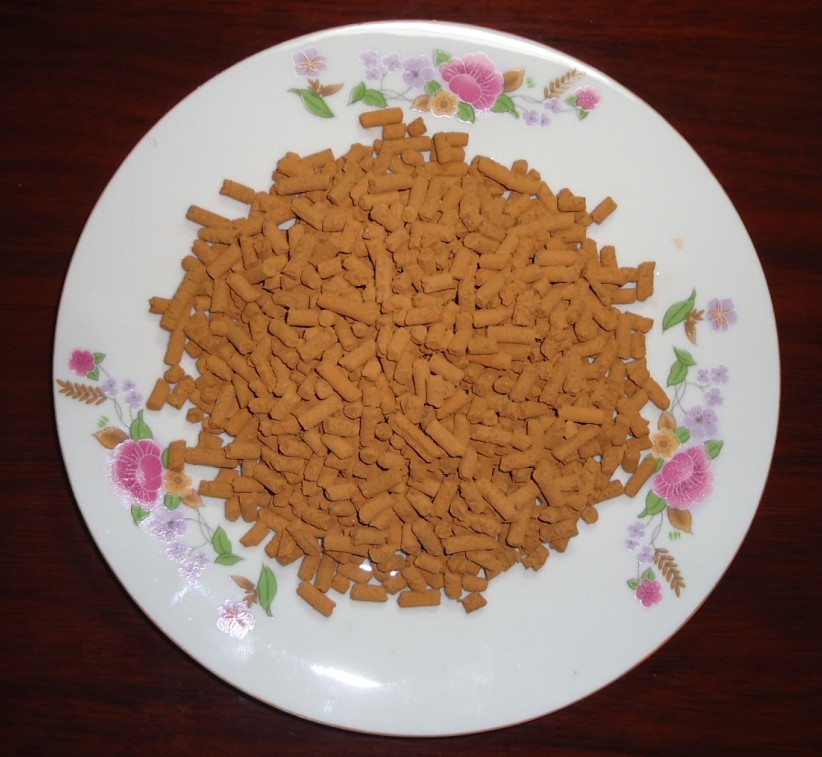
Performance and features:
1,Process conditions:
Temperature: 10-80 ℃;Airspeed: 500-1500h-1;
Superficial line speed: 0.10-0.30 m / s;
Pressure: atmospheric pressure -8MPa;
Humidity: the higher the humidity the better, preferably close to saturated water vapor, but strictly no water is allowed to flow into the bed; bed height-diameter ratio ≥ 3.
2, No special heating and energy consumption is required, but in winter outdoor applications, desulfurization device must be insulated to avoid gas overcooling, reducing the activity of desulfurization agent and the bed of water and deteriorating operation.
3, The quantities of desulfurization agent required is subect to the following conditions:
① feed gas H2S concentration and gas flow;② sulfur capacity of desulfurization agent;
③ desulfurization tower volume size.
(Chemical Absorption) Biogas-CNG
After two-stage desulphurization processes, then go through our GasDec system for carbon removal, biogas could be upgraded to make CNG, for vehicle or going into national pipeline network.The gas quality after upgrading as below:
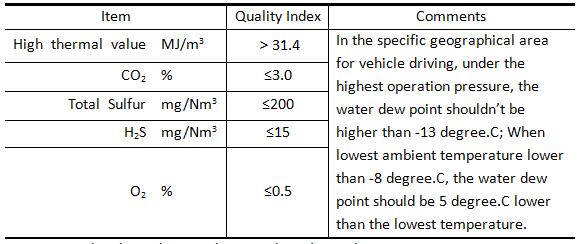
Comments: The above data is subject to clients’ actual requirements.
The Flowchart of biogas upgrading system
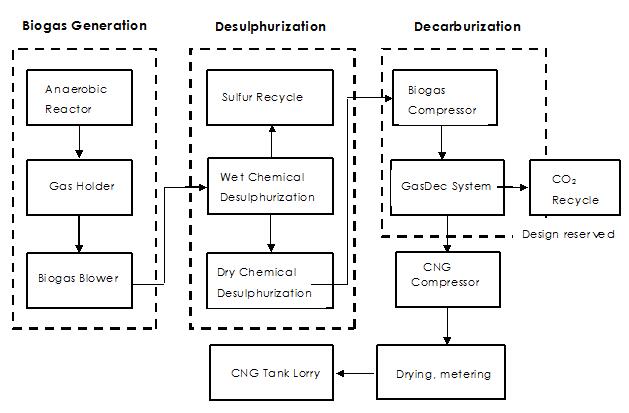
Procedures of our biogas upgrading system
1.Biogas Generation
Biogas is generated in anaerobic reactor and stored in gas holder in low pressure. Boosted by biogas blower, biogas is delivered to wet desulphurization tower;2.Wet Desulphurization
Wet chemical desulphurization technology is mainly structured as a single tower. Chemicals adopted is Na2CO3 with addition of catalysts (oxygen carrier). Chemicals is dissolved in the water, contact rightabout with biogas in the tower. More than 95% hydrogen sulfide, a small amount of carbon dioxide and other acidic substances can be absorbed by the liquid.The pregnant solution (the liquid) would be boosted by pump to a special groove, sprayed and oxidized by means of air suction for regeneration. Meanwhile elemental sulfur is precipitated out of the liquid, to be recycled for sale.
3.Dry Desulphurization
Dry chemical desulphurization technology is for the purpose of fine desulphurization, mainly structured as double towers, can be used alternately or operated in parallel or in series. Chemicals adopted is usually ferric oxide. Hydrogen Sulfide is converted to solid sulfide.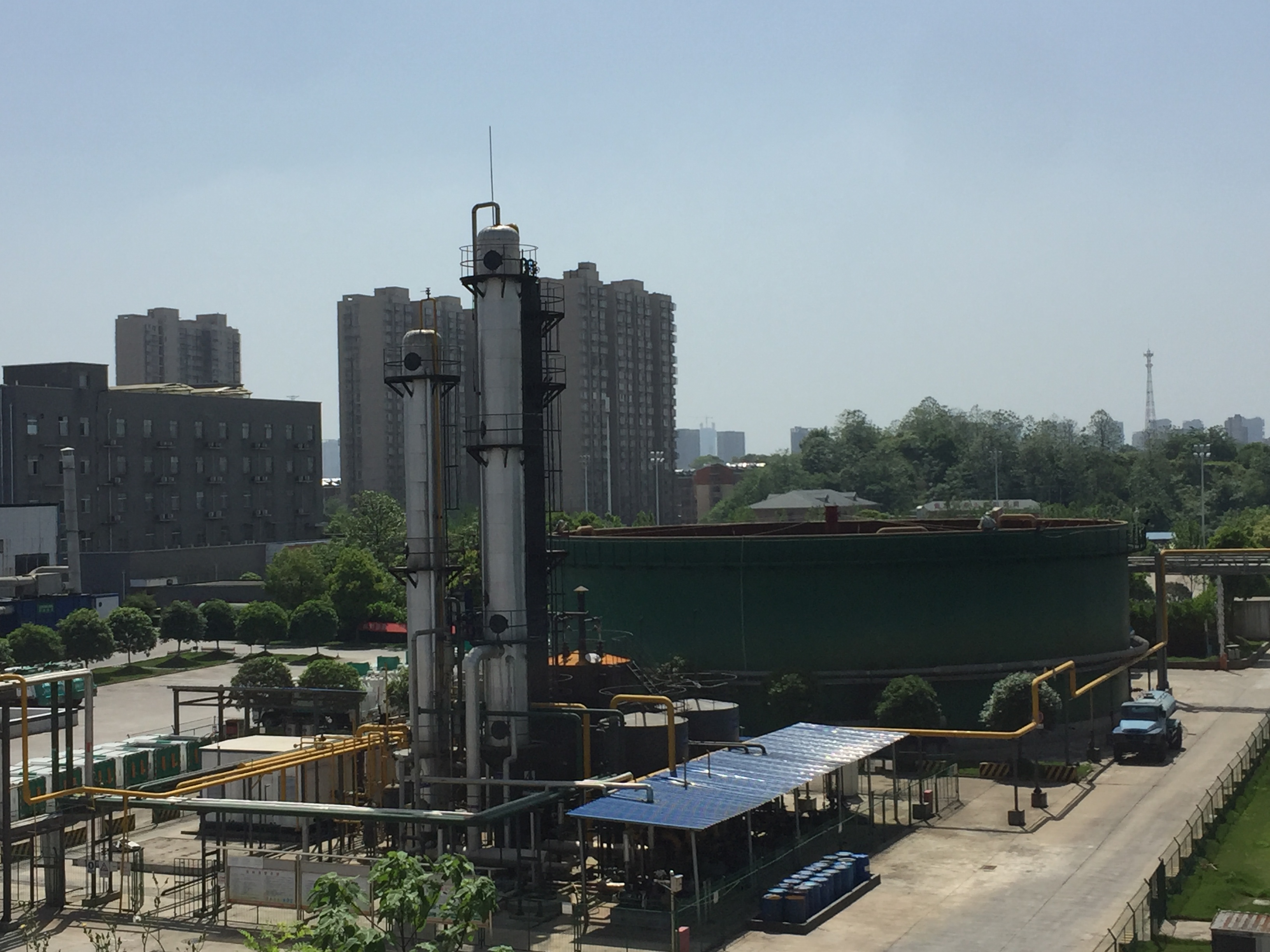
4.Gas Cleaning
The gas is boosted by biogas compressor, then after procedures of cooling, water and impurities removal, to be delivered to decarburization unit.5.Biogas Decarburization
The decarburization technology we adopt is chemical absorption. Chemical solution contacts with biogas rightabout in the absorption tower, to absorb carbon dioxide till its content lower than 3%.The upgraded gas is discharged from top of absorption tower, to be cooled by cooler and cleaned by separator for the removal of condensate water and chemical solution. Then gas is delivered to compressor.
The pregnant solution (the liquid) returns to the regeneration tower. The precipitation of carbon dioxide is achieved through steam stripping. The precipitated carbon dioxide gets through cooler and separator, can be discharged into atmosphere directly. The barren solution from the bottom of regeneration tower is pumped through automatic flow monitoring pipeline into absorption tower for circulatory use.
This is our GasDec system.
6.NG Compressor
The gas after decarburization procedure we can call it natural gas now. Its pressure rises to 22MPa or other pressure levels by natural gas compressor.7.NG Cleaning
The compressed natural gas would be dried and cleaned further by automatic NG drier. The working principle of drier is pressure swing absorption, taking 4A molecular sieve as absorbent.8.CNG Metering
CNG metering device is required when gas is for sale. Measuring method we usually adopt mass measurement. Eg. The mass flowmeter of our project in Henan Province of China is Emerson CNG050, accuracy could reach 0.5 magnitude. Gas is filled into CNG tank lorry through gas dispenser machine, to be delivered to standard CNG station (or Primary CNG station) as fuel for vehicle.Main equipment list of our upgrading system
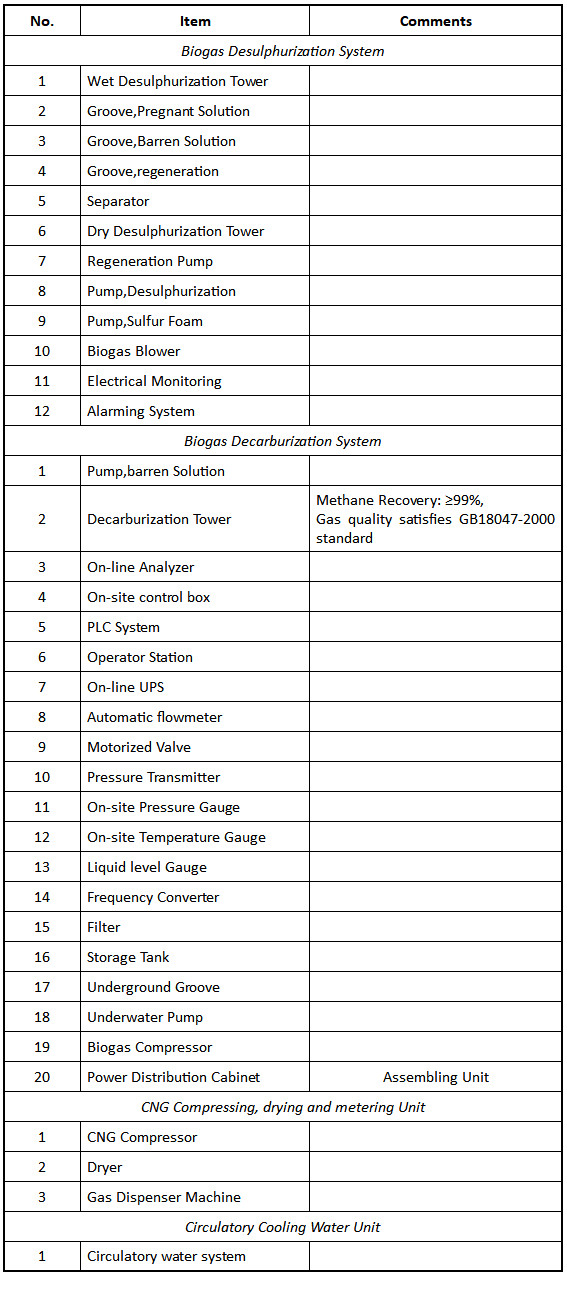
(Membrane Separation) Biogas-CNG
After two-stage desulphurization processes, then go through our GasDec system (Membrane Separation) for carbon removal, biogas could be upgraded to make CNG, for vehicle or going into national pipeline network.The gas quality after upgrading as below:
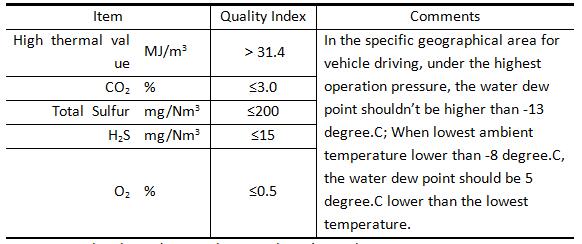
Comments: The above data is subject to clients’ actual requirements.
The Flowchart of biogas upgrading system
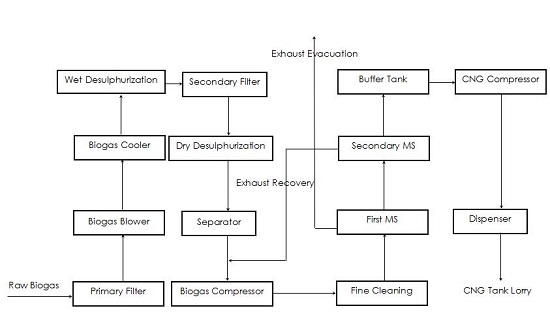
Procedures of our biogas upgrading system:
1.Primary Filter
The saturated water and partial particles in the raw digester gas are removed through the primary filter;2.Boosting, Primary desulphurization
The biogas from primary filter is boosted by blower. Then after cooling, the biogas is fed to wet type desulphurization system for primary removal of Hydrogen Sulfide, to make H2S content lower than 200 mg/Nm3;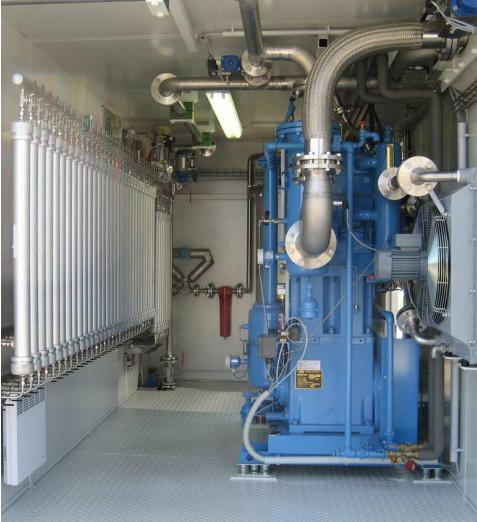
3.Fine desulphurization
The content of Hydrogen Sulfide is made lower than 50 mg/Nm3 through dry type desulphurization system;4.Impurities Removal, Fine Cleaning System
The new dust and impurities in biogas could be removed through the Separator; Then delivered to Fine cleaning system for removals of water and tiny particles in order to protect membrane and guarantee its life-time;5.First MS (Membrane Separation)
The high quality compressed biogas goes into the first MS system through gas-distributing pipeline. The exhaust gas could be gathered or discharged into atmosphere;6.Secondary MS (Membrane Separation)
The gas out of First-MS goes into Secondary MS system for final decarburization. The exhaust gas would totally return to the inlet of biogas compressor. Thiophane is added into the cleaned gas, after CNG compressor, through dispenser, to be delivered to gas station by tank lorry;Main equipment list of our upgrading system
1.Main non-standard equipment
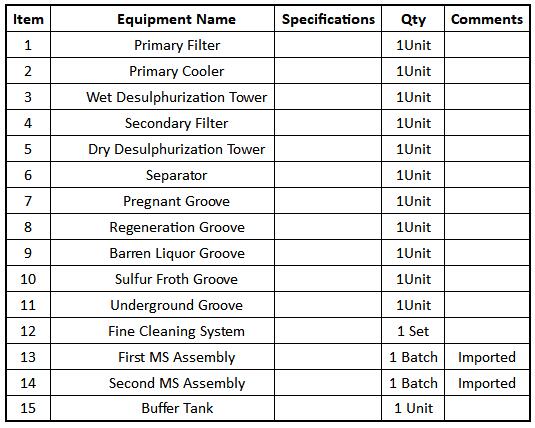
2.Main Operation Equipment List
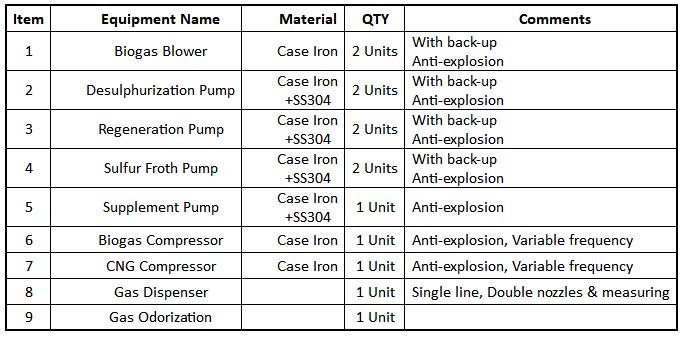
3.Instruments & controlling
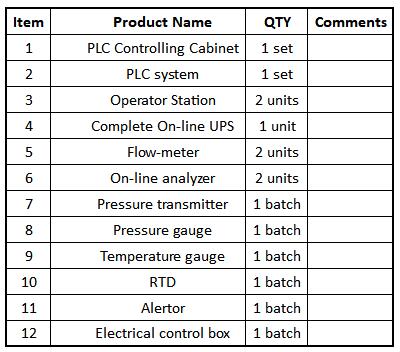
4.Main Monitoring Locations:
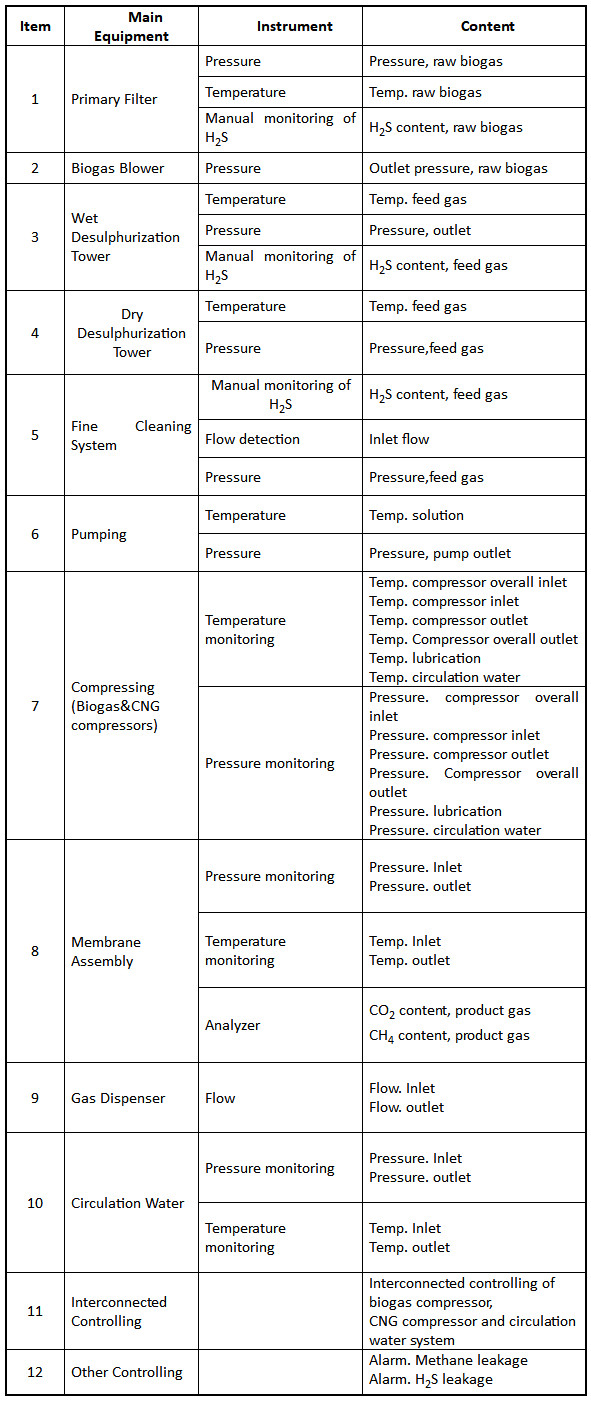
(Pressurized Washing) Biogas-CNG
After two-stage desulphurization processes, then go through our GasDec system (Pressurized Washing) for carbon removal, biogas could be upgraded to make CNG, for vehicle or going into national pipeline network.The gas quality after upgrading as below:

Comments: The above data is subject to clients’ actual requirements.
The Flowchart of biogas upgrading system:
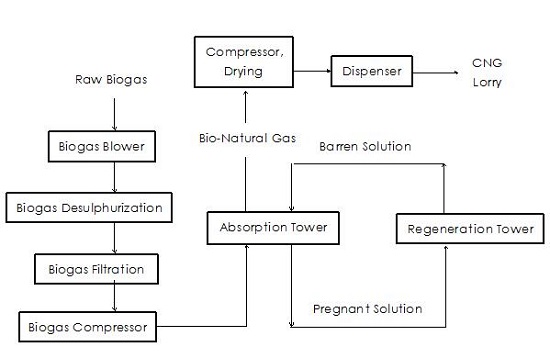
Procedures of our biogas upgrading system:
1.Gas
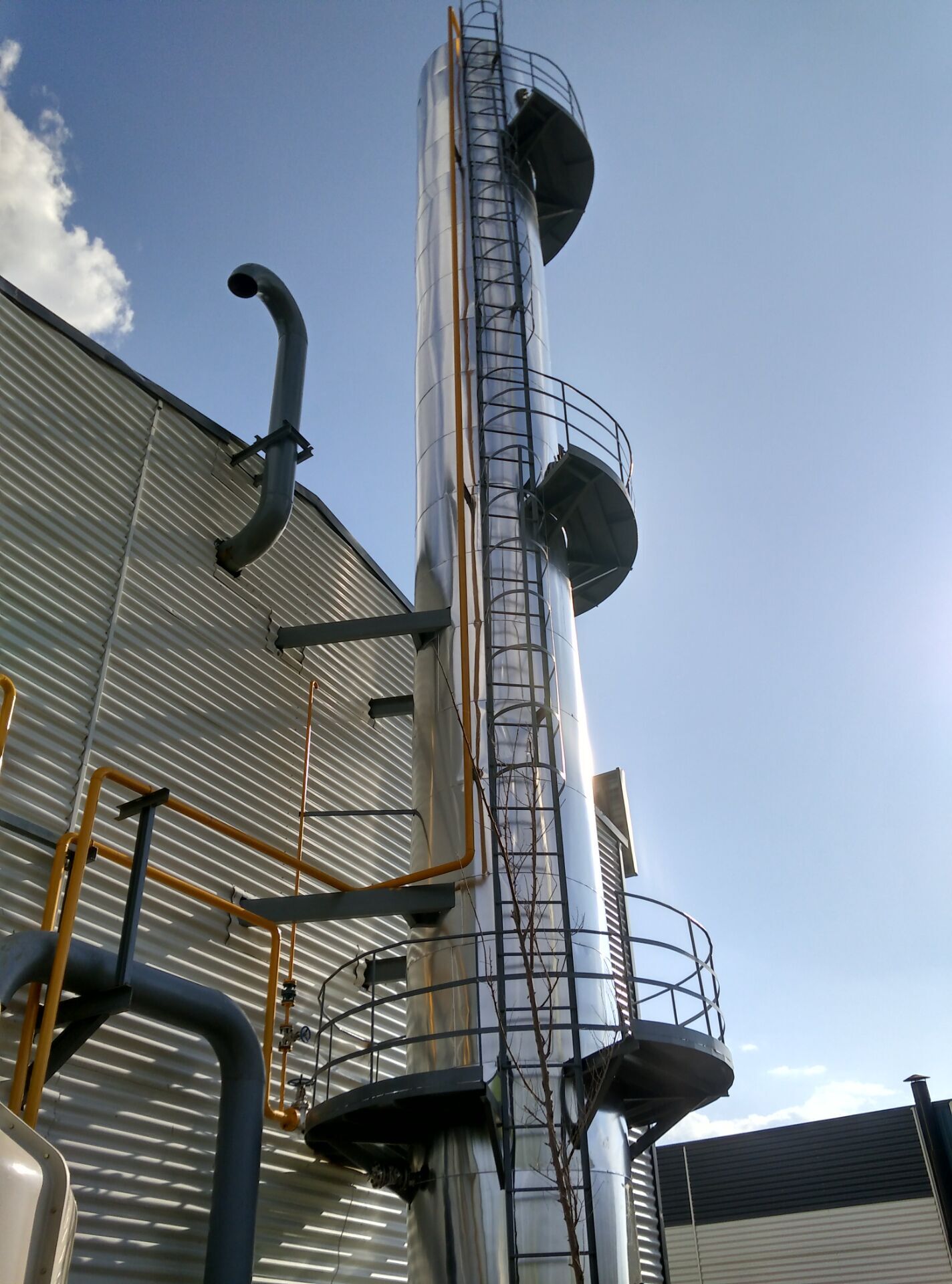
2.Liquid
The liquid is pressurized by barren-liquor pump, then is sprayed down along the packing layers in the tower through solution-distributor. Then contacts with biogas, absorbs CO2, the liquid becomes pregnant solution. Then goes into regeneration tower for pressure reduction and stripping for CO2 desorption, after cooled, the solution becomes barren liquor. The cleaned barren liquor is pressurized and delivered to absorption tower for recycling.The CO2 can be treated for producing food-grade or industrial grade.
Main equipment list of our upgrading system:
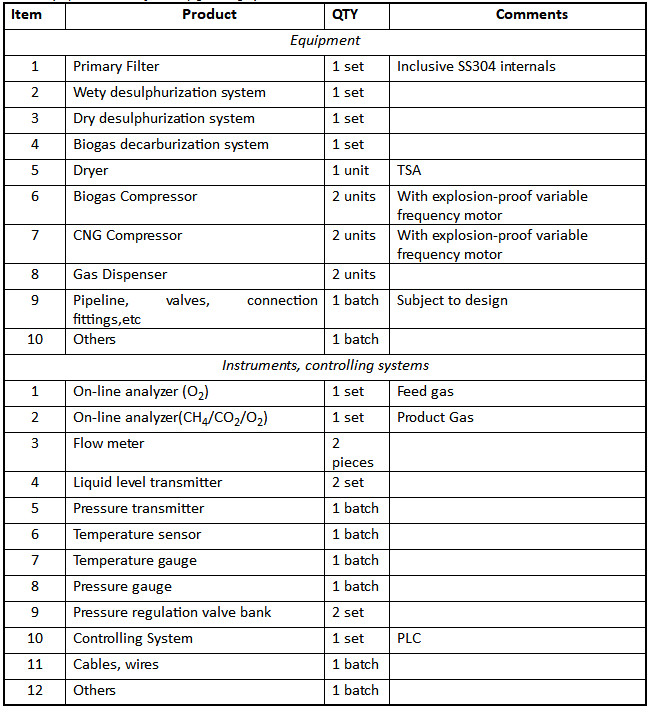
Cummins Biogas Generator
Hunan Along New Energy Technology Co., Ltd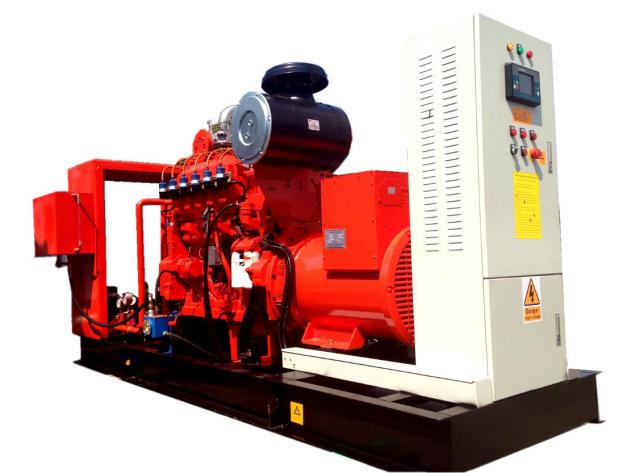
1.Europe: United Kingdom, Italy, Norway, Czech Republic, Spain, France, Russia, Romania, the Netherlands etc;
2.Oceania: Australia, New Zealand, etc;
3.Asia: Thailand, Malaysia, the Philippines, Bangladesh, Pakistan etc;
4.South America: Chile, Argentina, Bolivia, Peru etc;
5.Africa: Kenya, South Africa, Ghana, Togo, Nigeria,Senegal etc;
6.North America: United States;
ACG Series Biogas Generator Set/CHP
-Technology from USA Cummins
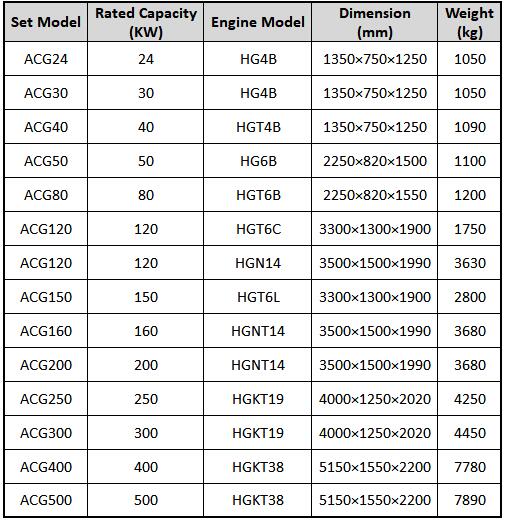
Comments:
1.Rated capacity as above is based on 50hz,while 60hz is available too;2.Alternator brands for option: Leroy Somer, Stamford, Marathon and Sinocox;
3.Control panel brands for option: ComAp, Deep Sea, Harsen and Smartgen;
4.Ignition brands for option: Altronic, WoodWard and MOTORTECH;
5.Automatic air&fuel ratio control system,automatic oil feed device are available;
6.Grid synchronization panel,containerized package,exhaust purification system can be provided according to customers specific requirements;
7.Heat recovery system for combined heat and power plant is available;
8.Warranty: 1 Year or 4000 Hours which comes firstly,can provide service of on-site maintenance and supply spare parts during the whole life of machine;
9.ALONG has a professional team for on-site installation internationally.
Deutz Biogas Generator
Hunan Along New Energy Technology Co., Ltd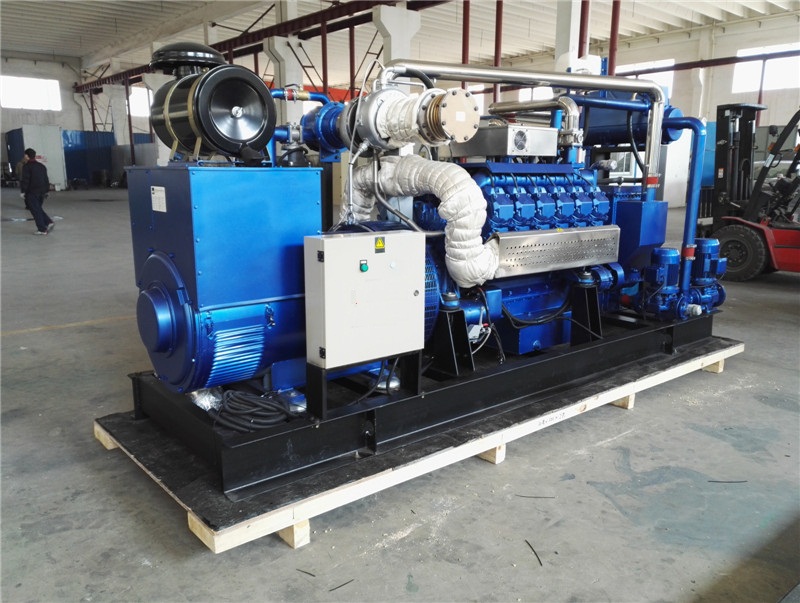
1.Europe: United Kingdom, Italy, Norway, Czech Republic, Spain, France, Russia, Romania, the Netherlands etc;
2.Oceania: Australia, New Zealand, etc;
3.Asia: Thailand, Malaysia, the Philippines, Bangladesh, Pakistan etc;
4.South America: Chile, Argentina, Bolivia, Peru etc;
5.Africa: Kenya, South Africa, Ghana, Togo, Nigeria,Senegal etc;
6.North America: United States;
ADG Series Biogas Generator Set/CHP
-Technologies from Germany Deutz
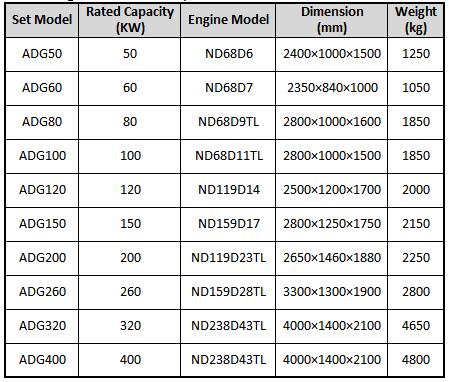
Comments:
1.Rated capacity as above is based on 50hz,while 60hz is available too;2.Alternator brands for option: Leroy Somer, Stamford, Marathon and Sinocox;
3.Control panel brands for option: ComAp, Deep Sea, Harsen and Smartgen;
4.Ignition brands for option: Altronic, WoodWard and MOTORTECH;
5.Automatic air&fuel ratio control system,automatic oil feed device are available;
6.Grid synchronization panel,containerized package,exhaust purification system can be provided according to customers specific requirements;
7.Heat recovery system for combined heat and power plant is available;
8.Warranty: 1 Year or 4000 Hours which comes firstly,can provide service of on-site maintenance and supply spare parts during the whole life of machine;
9.ALONG has a professional team for on-site installation internationally.
MAN Biogas Generator
Hunan Along New Energy Technology Co., Ltd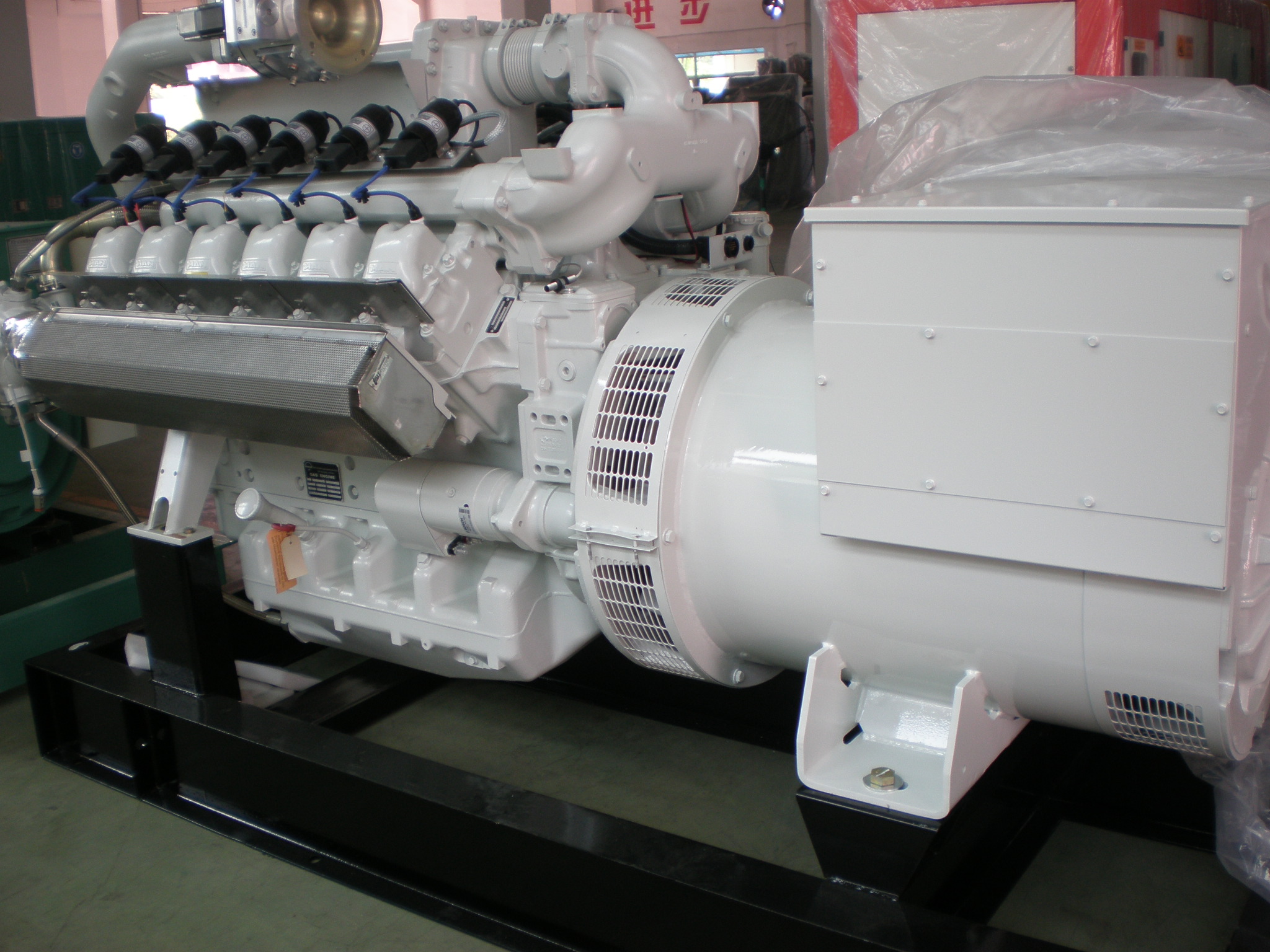
1.Europe: United Kingdom, Italy, Norway, Czech Republic, Spain, France, Russia, Romania, the Netherlands etc;
2.Oceania: Australia, New Zealand, etc;
3.Asia: Thailand, Malaysia, the Philippines, Bangladesh, Pakistan etc;
4.South America: Chile, Argentina, Bolivia, Peru etc;
5.Africa: Kenya, South Africa, Ghana, Togo, Nigeria,Senegal etc;
6.North America: United States;
AMG Series Biogas Generator Set/CHP
-Engine is originally made in German for biogas application
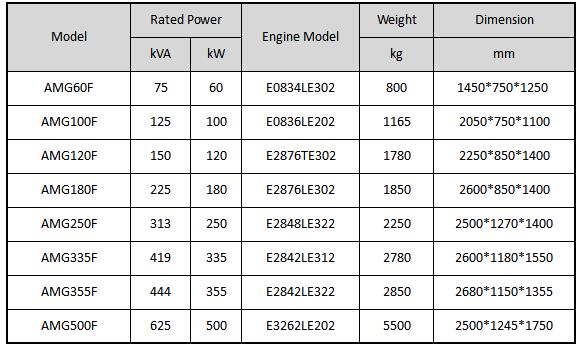
Comments:
1.Rated capacity as above is based on 50hz,while 60hz is available too;2.Alternator brands for option: Leroy Somer, Stamford, Marathon and Sinocox;
3.Control panel brands for option: ComAp, Deep Sea, Harsen and Smartgen;
4.Ignition brands for option: Altronic, WoodWard and MOTORTECH;
5.Automatic air&fuel ratio control system,automatic oil feed device are available;
6.Grid synchronization panel,containerized package,exhaust purification system can be provided according to customers specific requirements;
7.Heat recovery system for combined heat and power plant is available;
8.Warranty: 1 Year or 4000 Hours which comes firstly,can provide service of on-site maintenance and supply spare parts during the whole life of machine;
9.ALONG has a professional team for on-site installation internationally.
Switch Gear
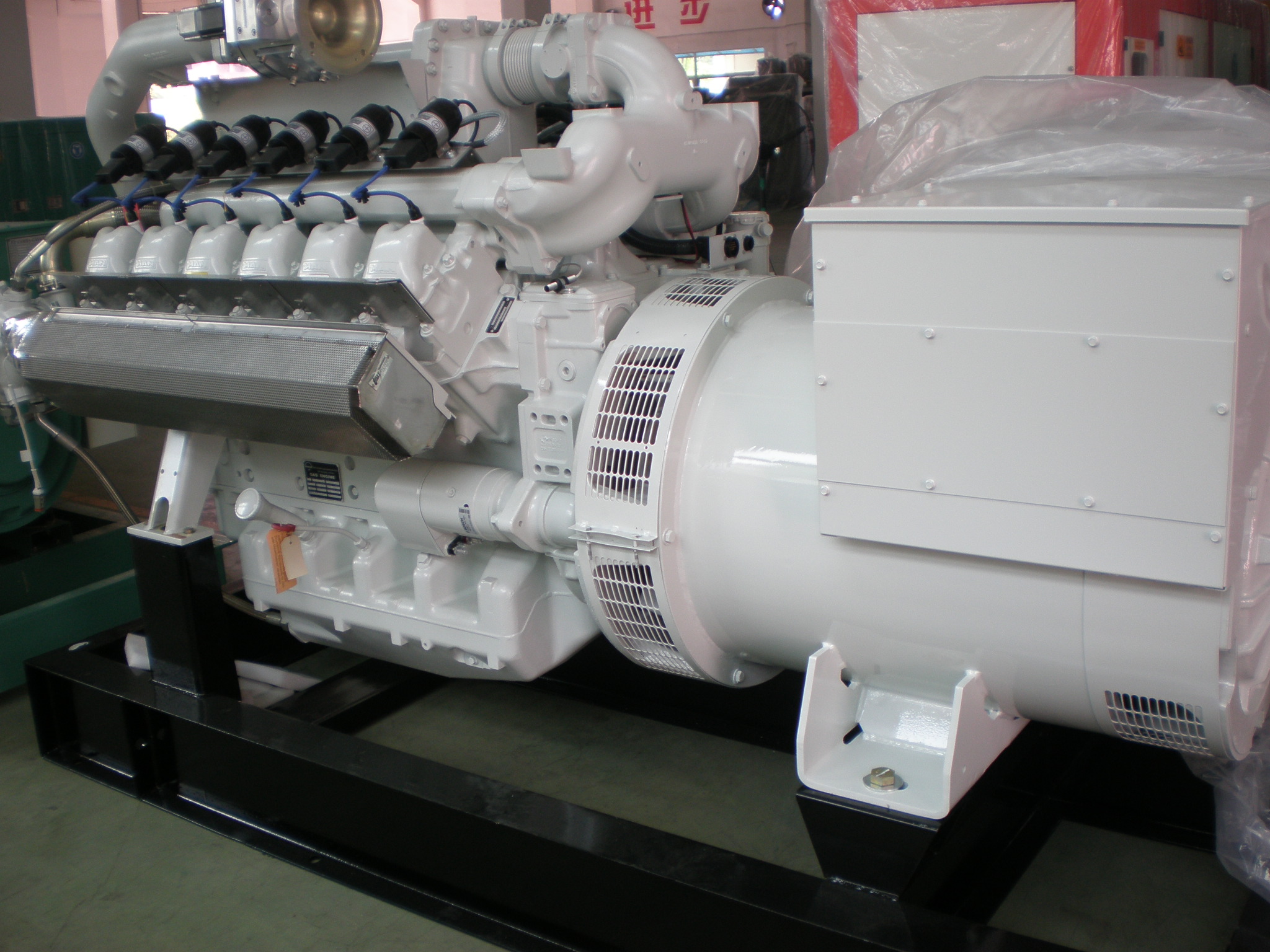
Based on plant design, we can provide high quality power distribution panel and switch gear at different voltage ratings, whose insulation class is in accordance with customers’ requirement; Multiple switch brands available: ABB, Schneider, Chint, etc.
They would be used for:
1.Power supply for biogas plant;
2.Power supply for owner’s production workshop;
3.Synchronization with national grid;
4.Automatic changeover between mains and generator.
Power Transformer
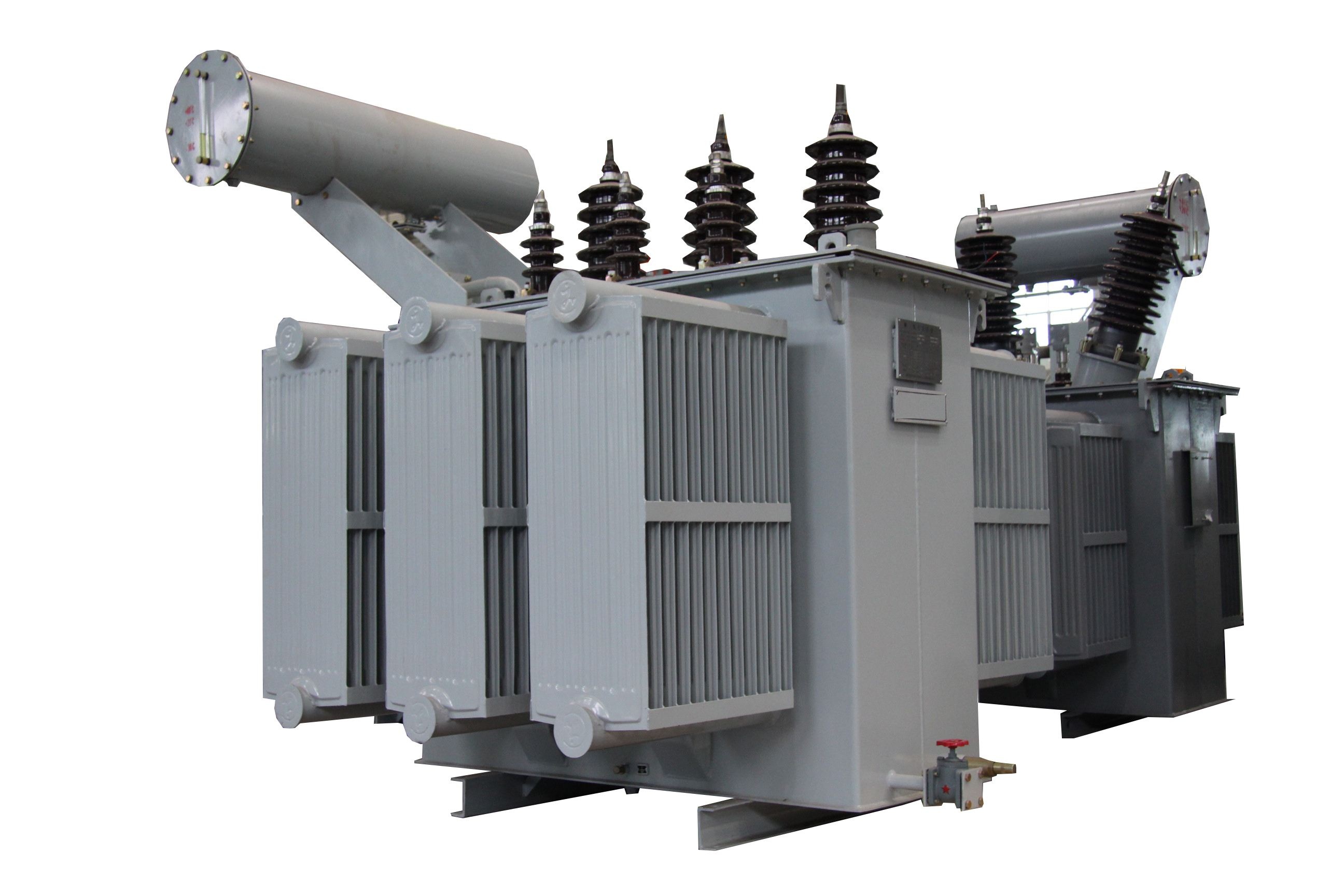
We can provide high quality oil immersed power transformers at different voltage ratings, mainly used when:
1.Step-down power transformer when power supply of the complete biogas plant and owner’s production workshop is from national grid;
2.Step-up power transformer when the electricity generated by biogas generator would be delivered to national grid through synchronization system.
Biogas Torch
Hunan Along New Energy Technologies Co., Ltdis committed to manufacture and supply high quality biogas torch.
Our biogas torch is in cylindrical tower structure,consists of tower body, burner, ignition system, control system and valve&pipe assembly. The top of torch body is equipped with a wind-proof cap. It has the following characteristics:
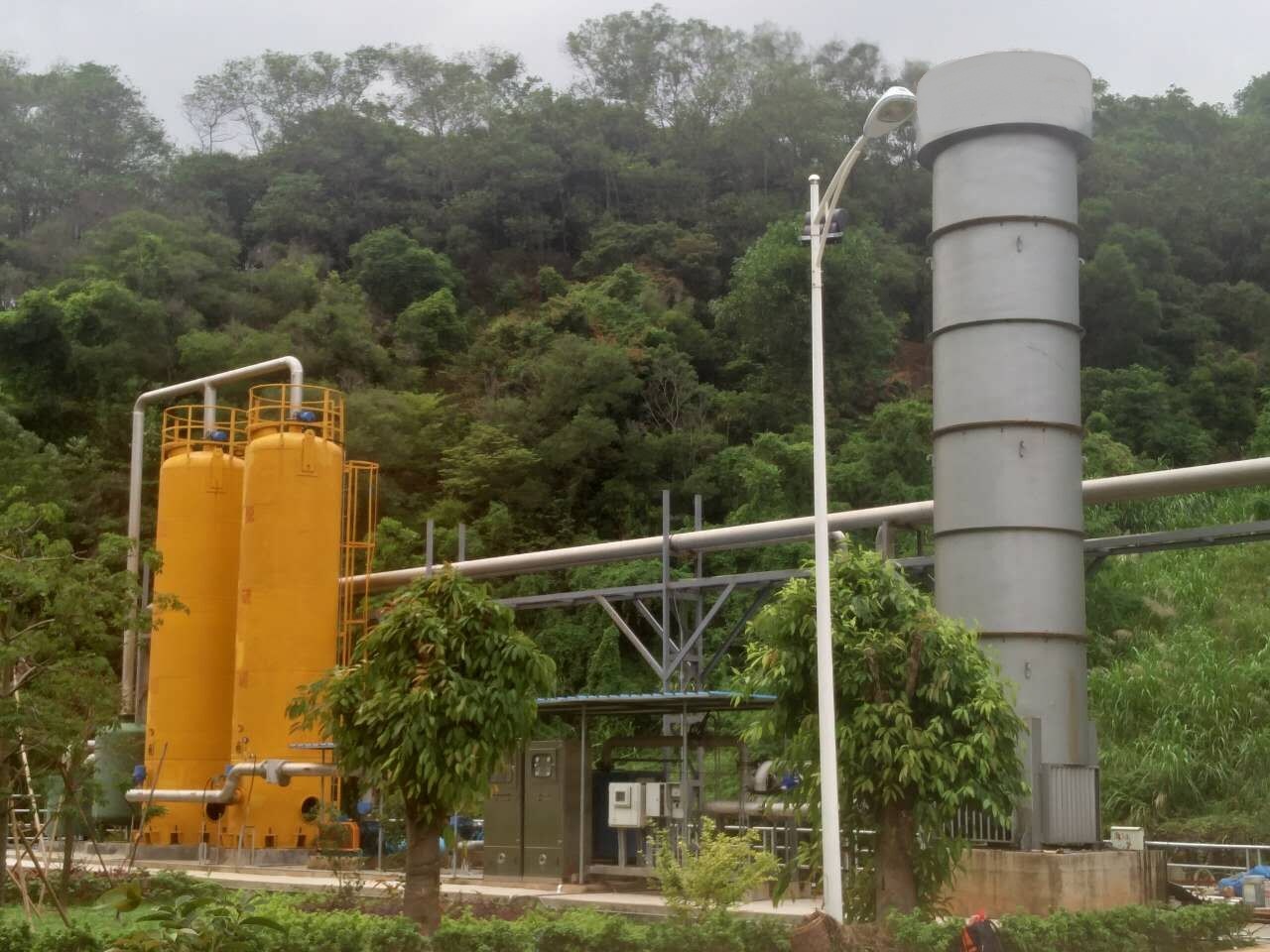
2.Main material is stainless steel 304, while the burner adopts stainless steel 310S (06Cr25Ni20) material;
3.torch shell is stainless steel, the middle layer is insulation material, while the liner is special refractory of high temp resistance; The temperature of torch appearance does not exceed 60 degrees Celsius when in full-loading condition;
4.The combustion of biogas occurs in the enclosure and no flame at top of torch;
5.torch can be operated manually or automatically or both combined with function of remote controlling available;
6.Burner and flame arrester can prevent the occurrence of tempering;
7.The solenoid valve would be open or closed automatically when the pressure signal from pressure switch is received by system;
8.Biogas supply would be cut off automatically when flame signal can not be detected by the flame detecting system;
9.Automatic electronic ignition.Constant lighting settled,which is always on working to ensure the success rate of ignition and would be closed only when the pressure is too low.
10.Combustion efficiency 99%, Noise level 60 dB.
Parameter Table for Election
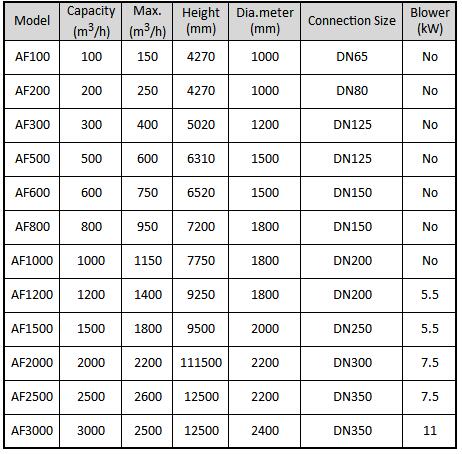
Biogas Steam Boiler
Hunan Along New Energy Technologies Co., Ltdis committed to supplying reliable steam boiler.
Our WNS series biogas-fueled steam boiler is horizontal positioned wet back type,with three-back fire tubes and wave-shaped bottom-located furnace gallbladder.Operable fire doors for front and rear air boxes with saddle type base.The shell of boiler is made of soft milky white color plates.
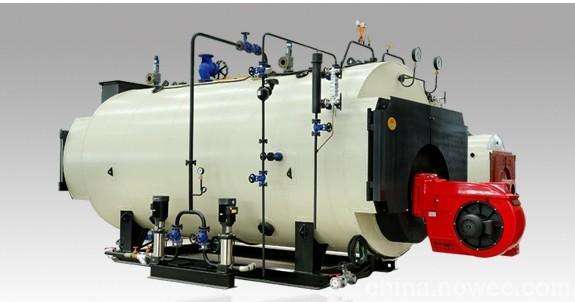
Water fed into boiler at upper position,the high-speed turbulence of water makes convection,radiation and conduction maintain in ideal state and continuously destroy the bubbles and attachments on the laminar boundary,to ensure good water-cooling on the heating surface of boiler.The design of low-positioned combustion chamber makes the safe range of water level bigger,as well as bigger the vapor-phase room.The unique steam-water separator ensures better steam quality(Dryness level higher than 97%).
Electrode type water level control system, with high, medium,low, very low water level protections. Multiple security interlock protection devices for projections of steam pressure, high temperature, burner flameout, safety valve, password, explosion-proof gate etc, so that the safe operation of the boiler is always in a controlled state.
Boiler would be packaged well before delivery, with reliable valves, burner and feed pump are imported brands with high-quality to ensure that every part of the boiler is reliable. In accordance with design specifications, set up furnace inspection door, head hole, hand hole, fire inspection hole, explosion-proof door and operable front&rear doors to ensure facilitate maintenance and cleaning.
Parameters Table for Selection
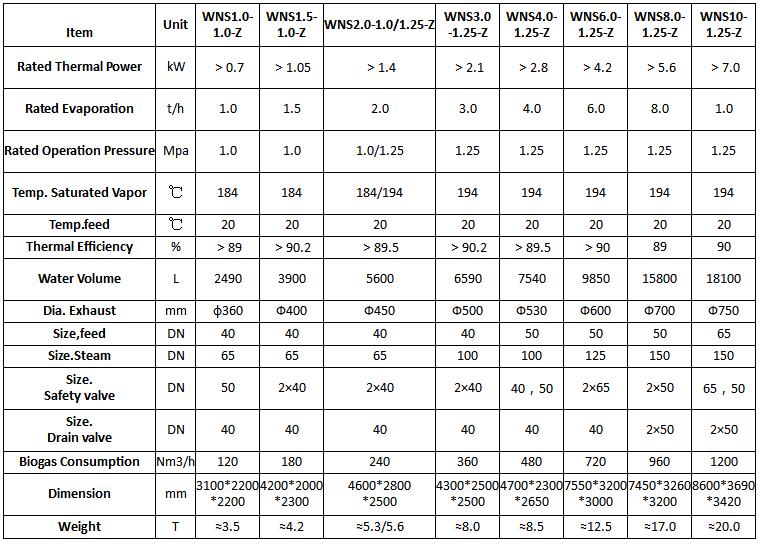
Biogas hot-water boiler
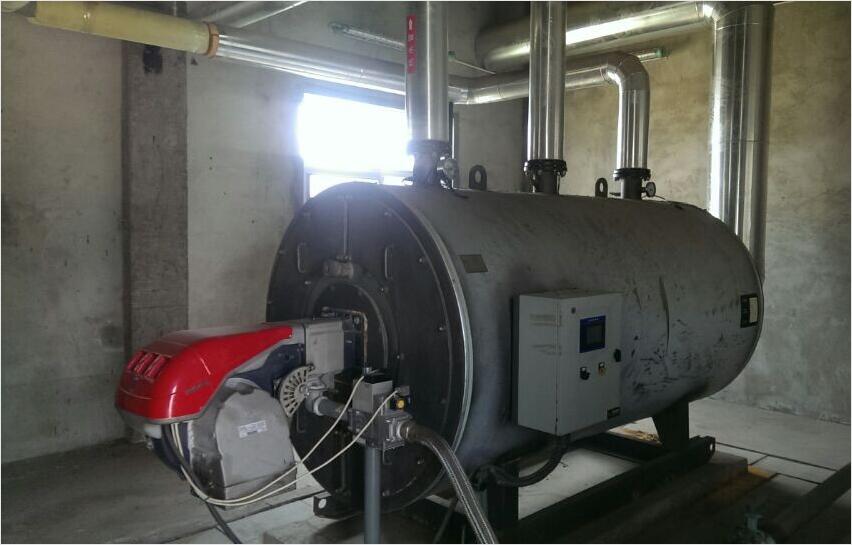
CLHZ series hot-water boiler can be fueled by biogas, or double fuels of biogas & coal, or biogas & natural-gas. Product features as below:
1.Can be fed by biogas only for environmental protection;2.Equipped with automatic controlled burner with performances of automatic swing-flap and ignition, and with protection for gas leaking;
3.Equipped with automatic controlling system for controlling feed pump and circulation pump. Temperature can be set, boiler would be stopped automatically when it reaches the set point;
4.The surface of boiler is thermally insulated with rock wool, packed with color-coated sheets. It presents good appearance. And it occupies small area.
Parameter Table for Selection
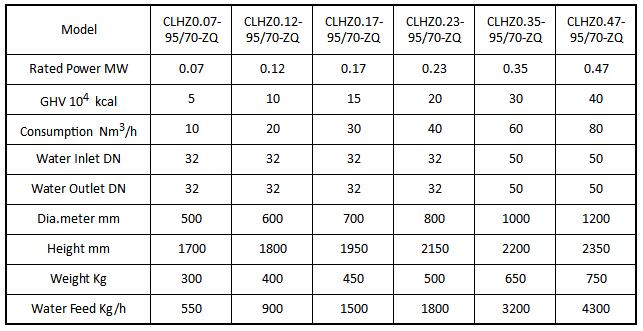
Spiral Extrusion Separator
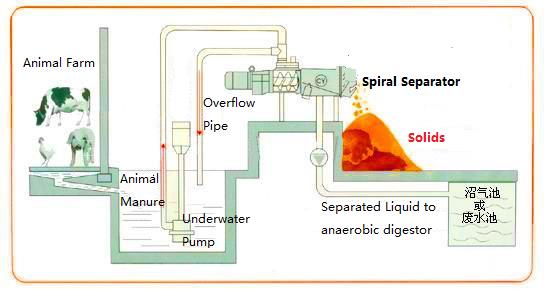
Extrusion-type separator, also known as spiral extrusion solid-liquid separator, mainly consists of mainframe,motor, sewage pump, control cabinet and pipes. Mainframe is composed of machine block,extrusion spiral shaft,sieving screen,gear reducer and discharging devices. It is widely used for solid-liquid separation of high concentration of organic sewage from all kinds of livestock farms, vinasse, decoction dregs, paper pulp, starch residue, soya residue and slaughterhouse.
Working Principle:
Liquid material with high solids content is pumped into separating system by no-clogging pump. Spiral shaft push material to the front of machine, to increase the pressure on the front edge to force the water in material extruded and flows out of sieving screen and get out of the drain. As separator working constantly, material is pumped into system constantly, the pressure on the front edge is being increased higher and higher, when it reaches a certain of degree, the solids discharging port would be open and solids would be extruded out of separator.ZK Series of Extrusion-type solid-liquid separator, has the following characteristics:
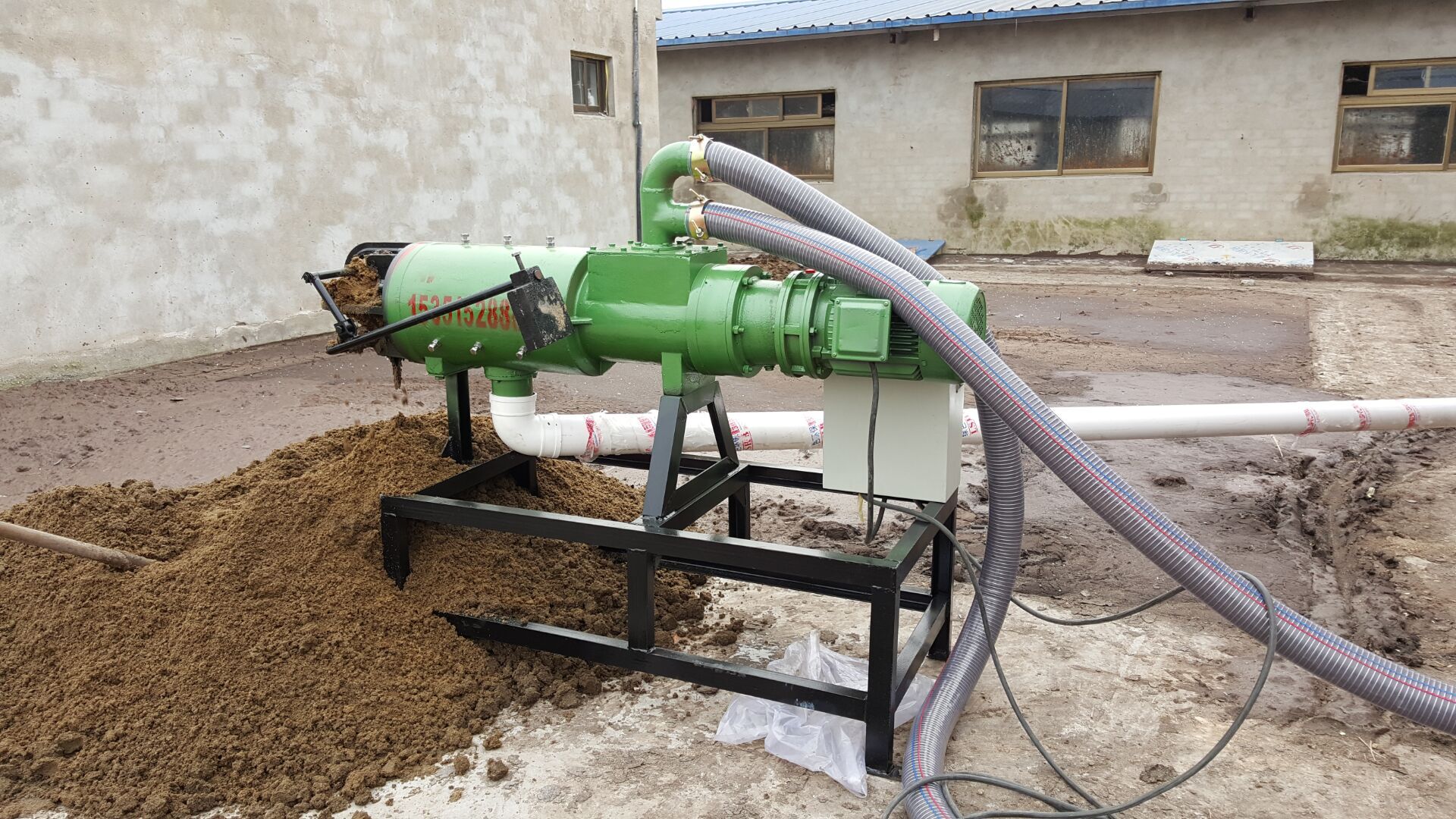
1,Practicality
High separation speed, applicable to different concentrations of livestock manure and sewage, the separated solid could reach 50~60% of TS%, easy for transportation, is suitable as raw materials for fish feed or organic fertilizer.2,Advancement
High decontamination ability, no clogging, easy for cleaning. The removal rate of total solids(TS), chemical oxygen demand(COD), total oxygen demand(TOD), nitrogen and phosphorus can reach 70-95%.3,Durability
Sieving screen and spiral shaft are made of nickel alloy steel or stainless steel with high strength. With high performance of anti-corrosion, high strength and long service life-time.4,Economy
The machine has high automaticity, low power consumption, high cost performance and easy operation by start/stop button.Parameter Table for Selection
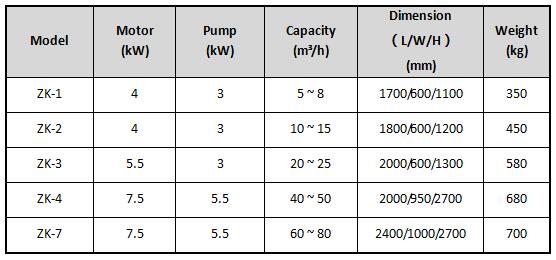
Mechanical Grille
GSHZ series of mechanical grillesare motor-chain-driven rake-teeth rotary type separator, are used for intercepting and removing big impurities, suspended solids and flotage in the sewage, to reduce the operation load of follow-up process.
This machine consists of rack, driving device, transmission mechanism, fixed grilles, reciprocating mobile grilles, rake teeth and electric control box. Driven by reducer of motor and transmitted by chain wheel, the rake tooth would be doing rotary motion; When they moves to upper position of machine, individual rake teeth would do relative movement under guidance of guide-wheel and curved rail; Most of solids substance would fall off by gravity, and is pushed to the discharging port for automatic dumping; By reverse rotation of the brush axis, the other part of solids would be washed clean.
Material Description
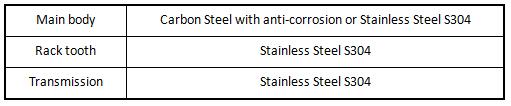
Structural Features:
1.Compact structure, high performance, big watering area, stable and reliable operation, easy installation and maintenance;2.Simple operation, good separation effect, high efficiency and long service life;
3.Easy maintenance, the underwater grilles are without fixed screws;
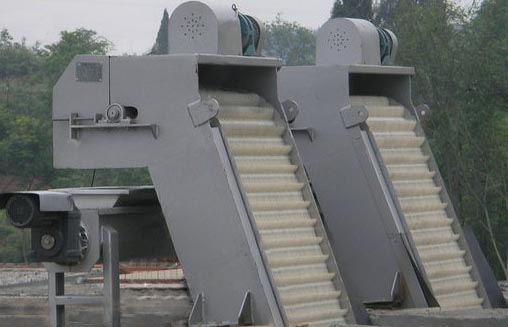
5.A set of indoor control box configured,all electrical components are domestic and international brand-name, PLC interface can be reserved for remote monitoring;
6.With controlling functions of automation,jog,emergency stop and cut-off, to facilitate the maintenance;
7.With double overload protection devices,mechanically and electrically,
A,Mechanical measure: a safety pin built into the transmission sprocket,can be cut off instantaneously in the case of overload, to prevent damage to the transmission;
B,Electrical measure: the over-current protection would avoid the burning of motor;
8.Chain and rotating wheel are made of Stainless Steel,while the underwater guidance of chain is in slide way,no need to add lub-oil, so china is not easy to be stuck by dirt;
9.The driving mechanism is equipped with protective cover,to meet the needs of outdoor installation and easy maintenance;
10.A chain plate is set between chain and rake teeth,a enclosure is formed along with the water blocking corners,thus preventing residue entering into running track of machine,to avoid infarction of chain;
11.When the tooth rakes run to the rear of the equipment, the relative displacement between the rakes, to do self-cleaning movement, the grid slag falls into the slag car. So there will be no clogging phenomenon, so the daily maintenance of the workload is very little and the bottom of the grid will not have dirt accumulation dead ends.
12.When machine installation, the two sides contacting with the ditch wall are sealed with rubber sealing tapes,which is fixed with steel strip. The bottom rake tooth chain is provided with a flat plate and a rubber sealing tape to prevent leakage of impurities in the sewage;
13.The two sides of upper part of machine is equipped with pore plates for maintenance;Even if the rake teeth or other parts are damaged by large hard impurities,the replacement work can be done at working platform, no need to go underwater and not affect the water flow.
Parameter Table for Selection
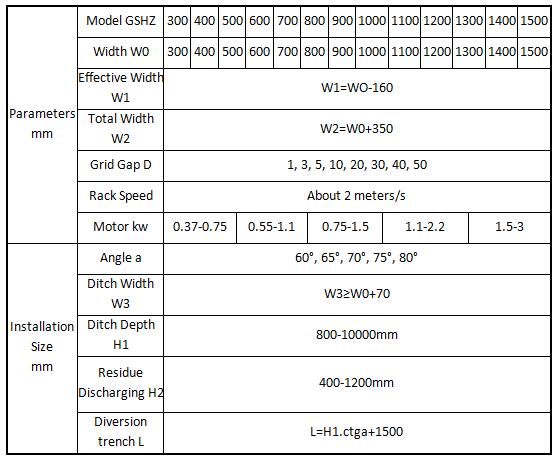
Comments:
A spiral conveyor can be ordered together, for gathering and transmission of separated solids automatically.Spiral Centrifuge
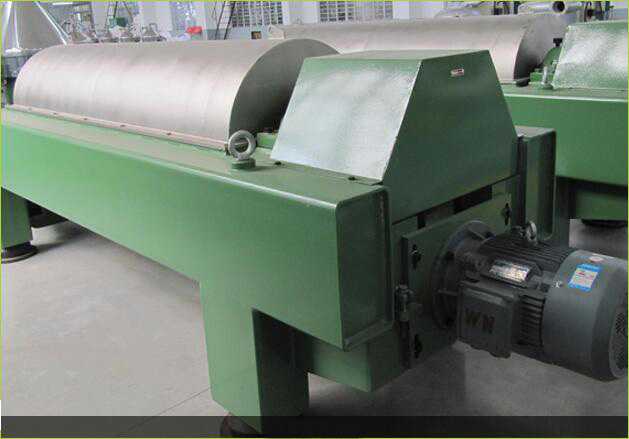
Horizontal Spiral Centrifuge:
is used for separation of oil,water and solids, which exist in feedstock of food waste. It consists of rotor drum, screw, differential, motor, rack and casing.Structural Features:
1,Under design of double cone angle, the inside wall of rotor drum is longitudinal-groove shaped,to improve the efficiency of spiral transmission of solid-phase;2,The face of spiral blade is coated by hard alloy protective layer, to prolong its wear life;
3,Main motor is controlled by Main frequency converter, while the auxiliary motor is controlled by the sub-converter, motor frequency can be adjusted arbitrarily;
4,Power supply of sub-converter is from main converter, known as DC bus power supply, to get energy feedback when auxiliary motor in working state, to effectively save energy.
Working Principle:
1,Feedstock is fed into the rotor drum of spiral centrifuge through charging pump;2,The powerful centrifugal force resulting from high-speed rotating drum make solids with higher density than water deposited on the inwall of drum;
3,Screw and drum are relatively moving because of speed differences(adjustable); The solids with higher density would be deposited on the inwall of drum, would be transmitted by spiral conveyor to the vertebral terminal of drum,to be discharged outside;
4,Two kinds of different densities of liquids(oil and water) would from a concentric cylinder; The higher-density liquid(water) in the inner layer while the lower-density liquid(oil) in the outer layer of cylinder;
5,The thicknesses of liquid layers can be adjusted by regulation panel(The moisture content in oil is adjustable); Water and Oil to be discharged through individual exports;
6,Automatic feeding and automatic discharging.
Parameter Table for Selection:
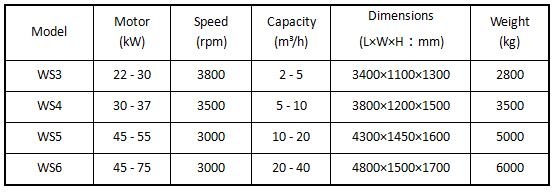
Frame Press Filter
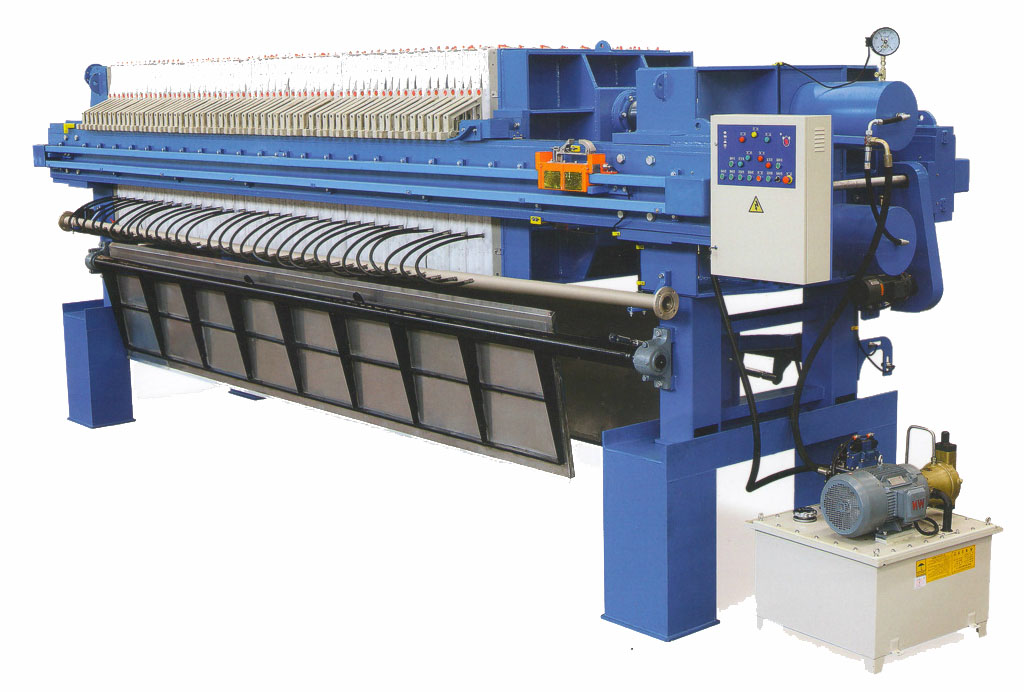
XZ Series of filter press,is used for separation of water and solid sludge.
Filter frames and filter plates with filtrate channel are arranged in parallel. Filtration fabric is folded besides each set of frame and plate.Frame and plate are compressed tightly by compression ends,so a filter chamber is formed. Sludge flows into system at the feed port, the separated water flows out of machine through filtration discharging port while the filter cake accumulated on the filtration fabric inside frame. The filter cake would be released and peeled off when frame and plate disentangled. Owing features of easy operation,high TS% in filter cake and strong applicability etc.
Frame and Plate are made of cast iron, cast steel, stainless steel, polypropylene, rubber and other materials. Frame and Plate can be compressed by manual spirally, electric spirally and hydraulically. Automatic plate pulling, automatic flapping filtration collection, explosion-proof, remote control and other functions are optional for customers’ choice.
Parameter Table for Selection:
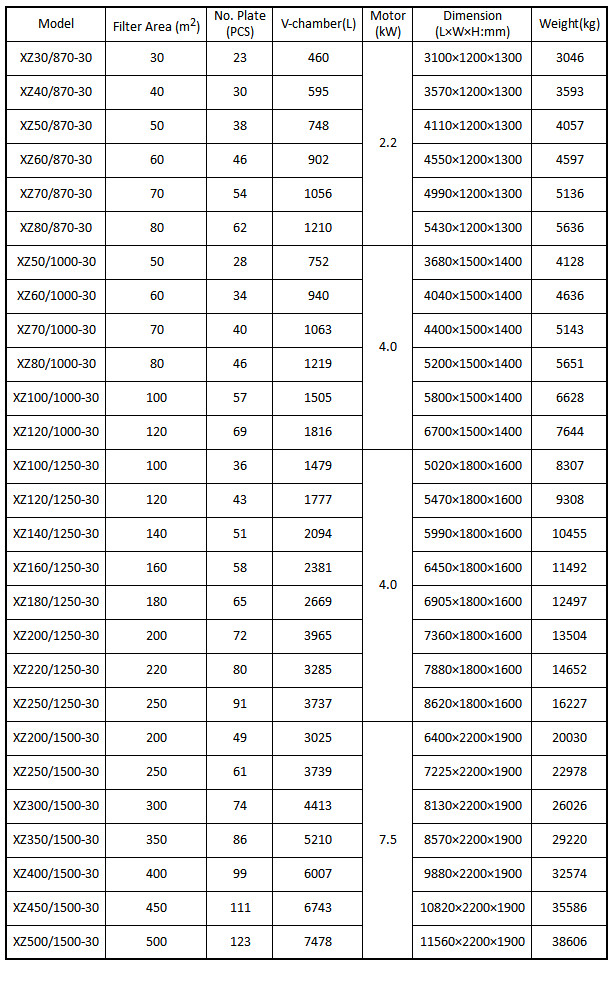
Spiral Desander
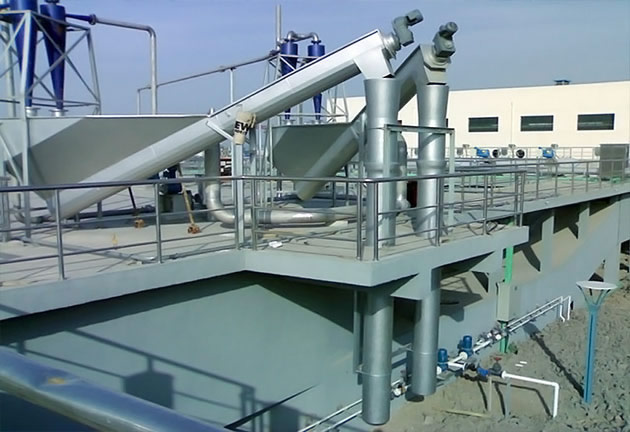
Our LSSF series Spiral Desander is used for the removal of sands in the mixture of liquid-solids. It consists of shaftless spiral, liner, U-shaped groove, water tank, deflector, weir and driving device.
Working principle:
The mixture of sand-liquid is pumped into water tank at the lower side. The sands would be deposited at the bottom of groove. Driven by spiral , the sands are pushed up along the inclined bottom of groove. When above water level, the sands continue to move up for a distance till water completely removed, then to be discharged into the sand barrel. The separated liquid if it contains organic substances can be delivered into anaerobic reactor for biogas generation.
Parameter Table for Selection:
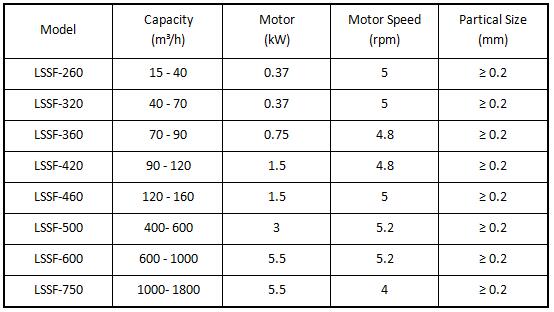
Slanting sieving separator
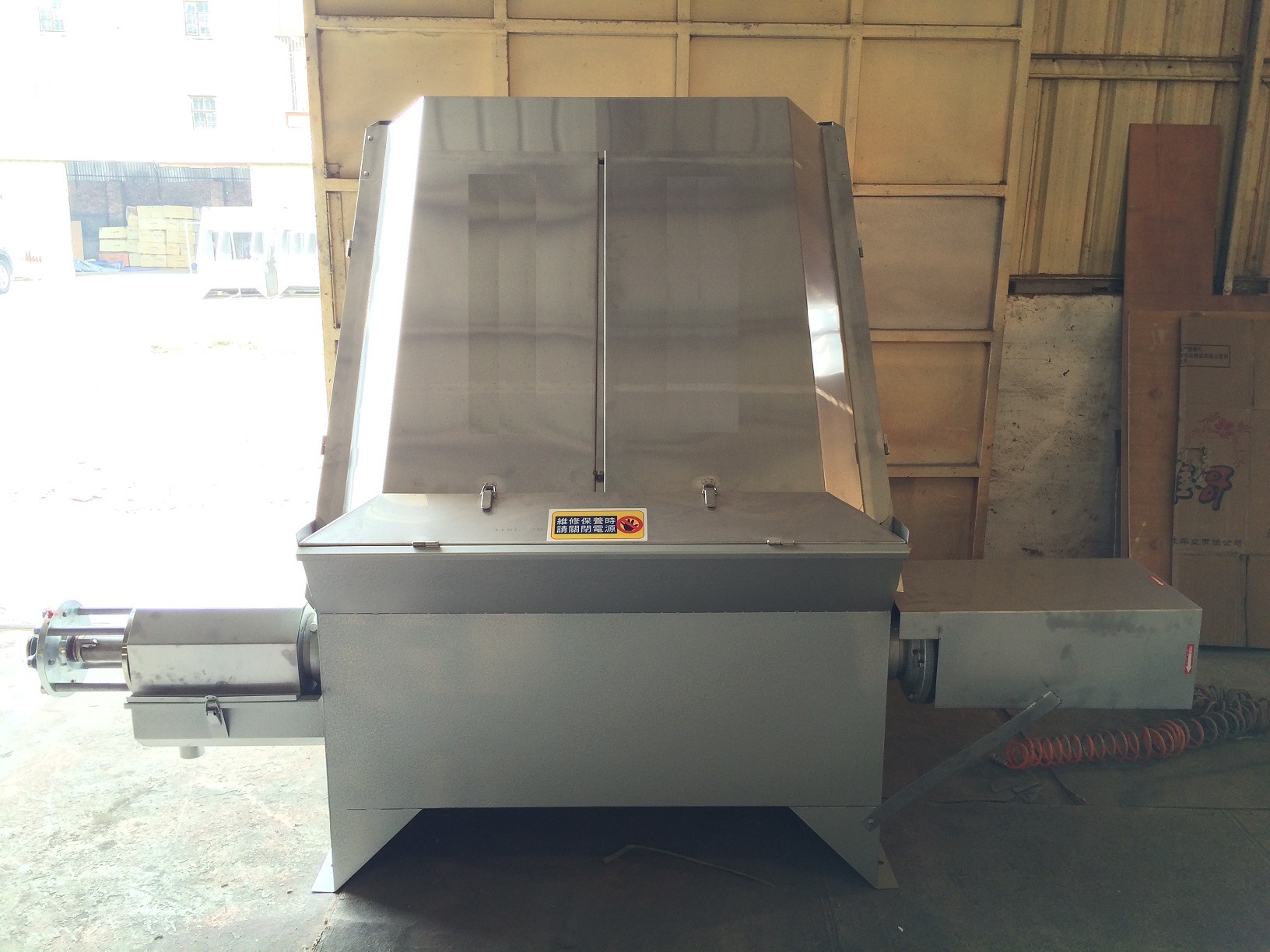
Slanting sieving separator is suitable for solid-liquid separation of waste of animal manure.
Separator is equipped with a triangular water-cutting wedge-shaped strainer and extrusion device, could achieve performance of automatic controlling for starting, filtering, extrusion and strainer washing when working or off-duty. It is mainly used for separation of big solids in the waste of animal manure, to reduce load for the follow-up biological treatment system, moreover to avoid the problem of blocking for the pumps and pipelines. The separated solids could be sent to composting plant for processing, the separated liquid can be delivered to anaerobic reactor for biogas production.
There are usually many suspended solids(SS) in the waste of animal manure. A majority of SS could be removed by the strainer. In this regard, it could effectively save the project investment in a commercial manner.
Parameter Table for Selection
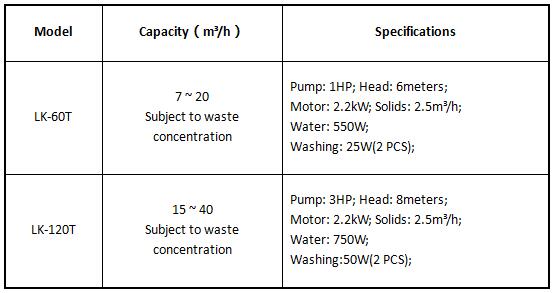
Comments:
Multiple separators could be used in parallel when project is big.
Portable Biogas Analyzer
Specifications:
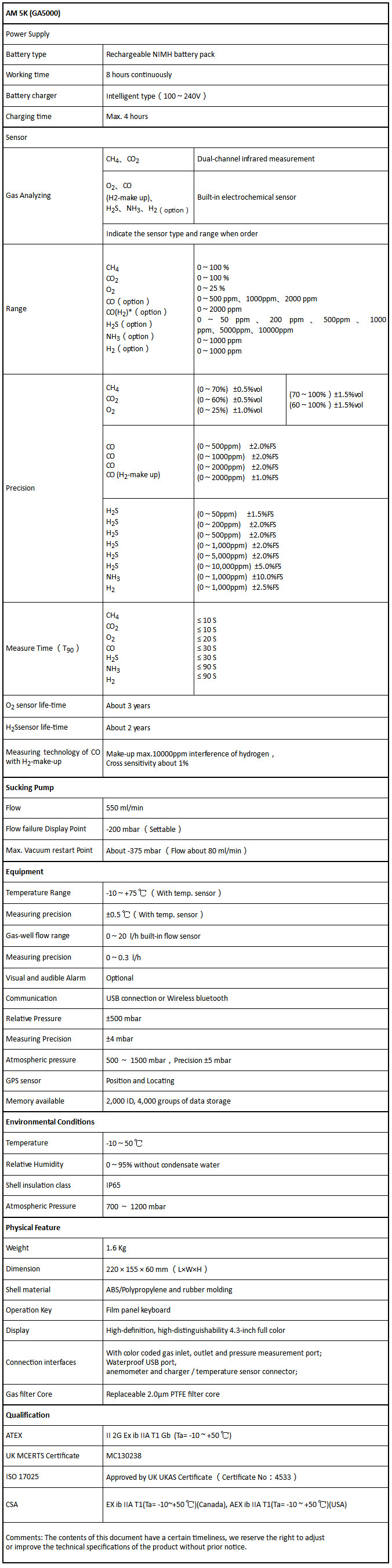
Product Features
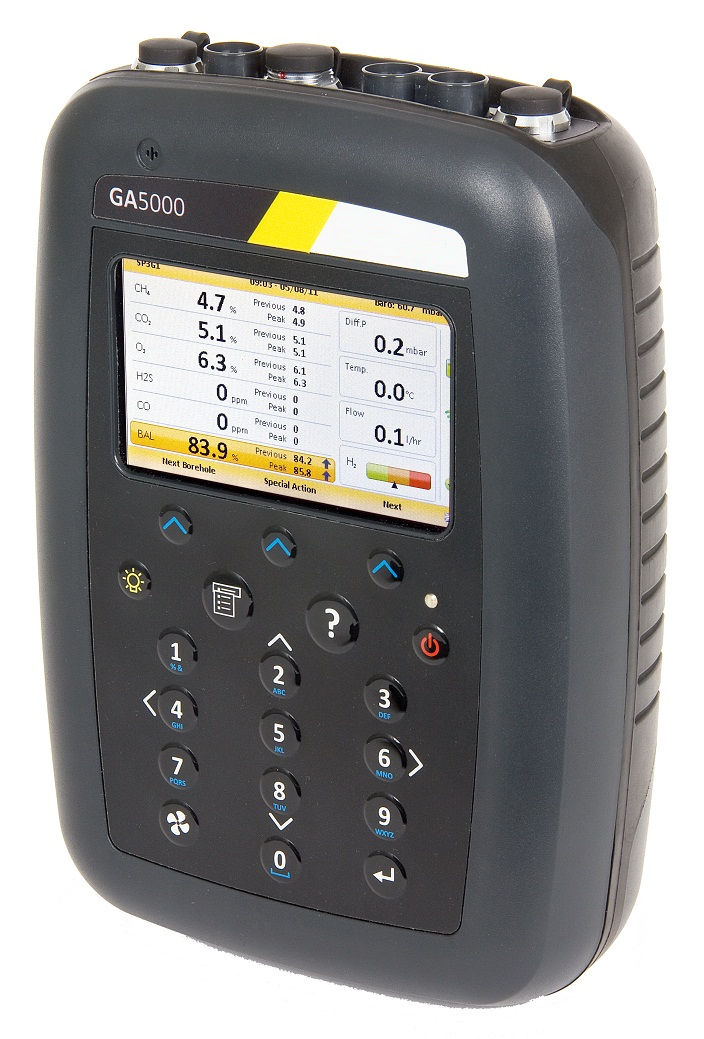
1. Simple operation and calibration steps
2. Meet the requirements of environmental legislation
3. Market-leading technology
4. Standardized monitoring procedures
5. Convenient data transmission
Optional Items
1. Optional sensor: H2S (max. range of 10,000ppm)CO (H2 compensation, up to 10000ppm (1%))
2. Gas well flow monitoring (l / h)
3. GPS navigation function
4. Analyzer computer management software
5. External measurement accessories:
anemometer (explosion-proof) temperature probe (explosion-proof)
Intelligent Vortex Flowmeter
Vortex flow-meter, a speed type flow meter, is widely used internationally for the implementation of measuring, detecting and controlling of liquid (such as water, fossil oil, grease, alcohol, etc), gas (such as air, oxygen, nitrogen, natural gas,etc) and Steam (saturated steam, super-heated steam).
VFD anti-shock type vortex flowmeter
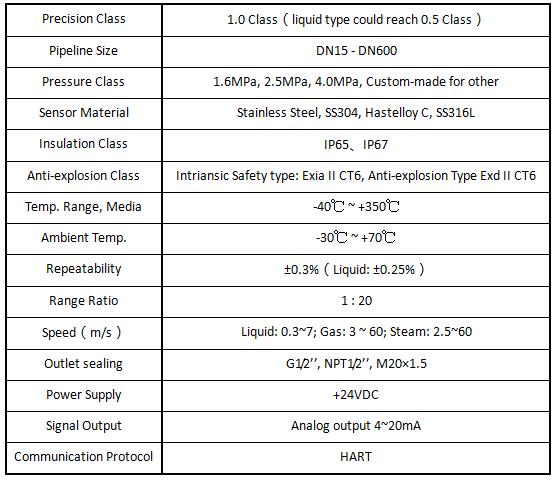
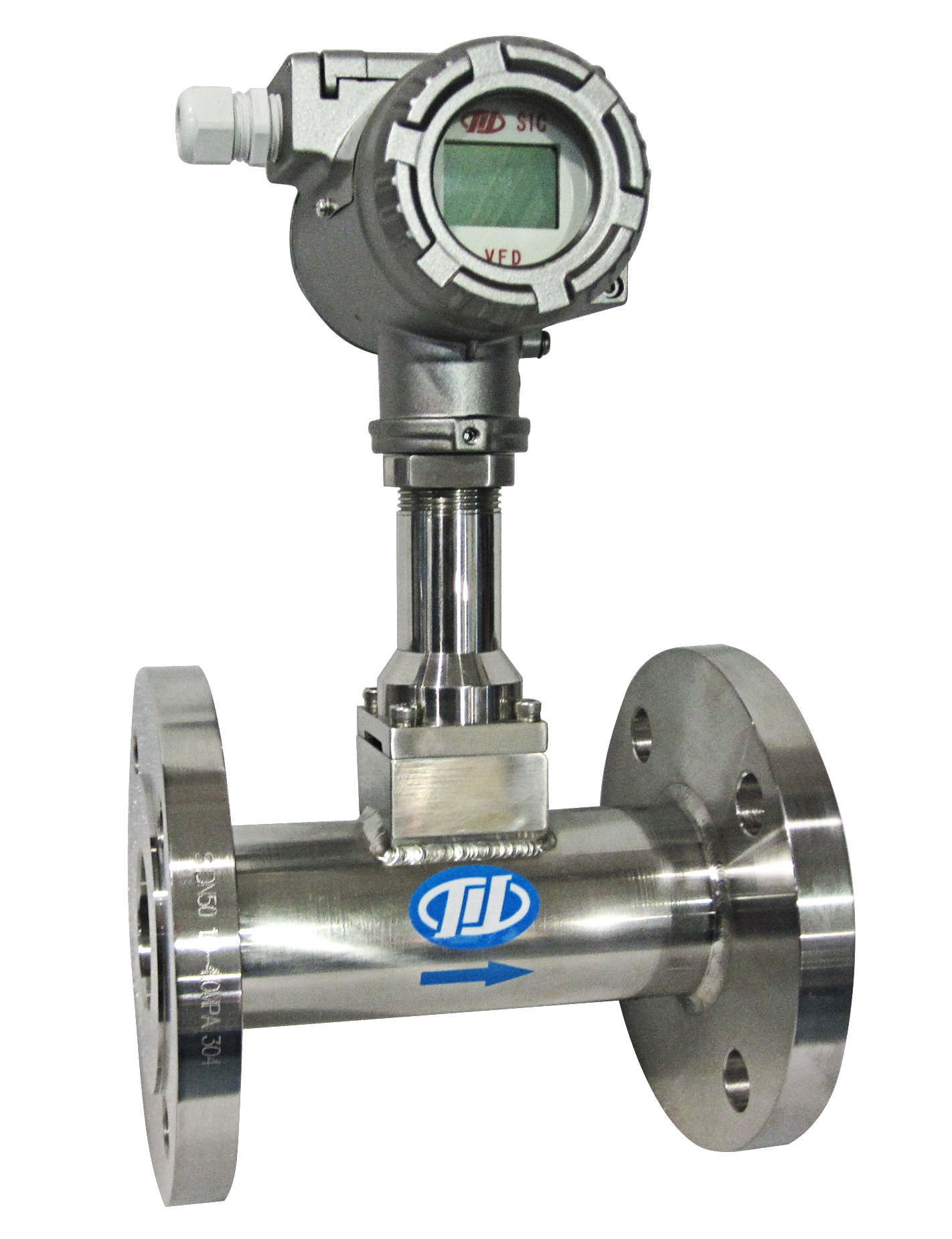
Display of Flow-meter converter:
1.Instantaneous flow;
2.Accumulative flow;
3.Bar graph and percentage of range;
Online Biogas Analyzer
BIOGAS 3000 is ATEX and IECEX explosion-proof certified biogas analyzer, with on-line detecting and domestic data output supported by powerful gas analysis technology.
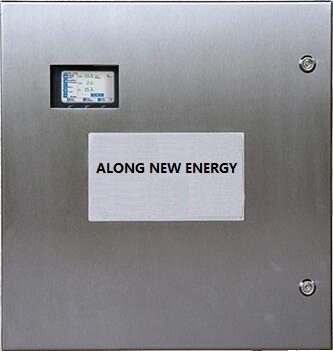
Product Features:
1.Standard model for CH4, CO2 and O2, and optional measuring for H2S, H2 and CO;2.Modular design for easy on-site maintenance;
3.User calibration function to ensure accuracy and reliable data output under extreme temperature conditions;
4.ATEX and IECEX certification;
5.ISO / IEC 17025 standard calibration to achieve the best accuracy
6.Be able to control the detection process before and after desulphurization
7.Continuous monitoring function, Max. 4 sampling points to control the complete detection;
8.IP65 rating of dust-proof and water-proof;
9.Built-in special alarm of level monitoring, gas alarm and fault notification;
10.4-20mA output, Modbus RTU communication, optional PROFIBUS and PROFINET communication;
11.Optional: heater, extended temperature range.
Product Parameters:
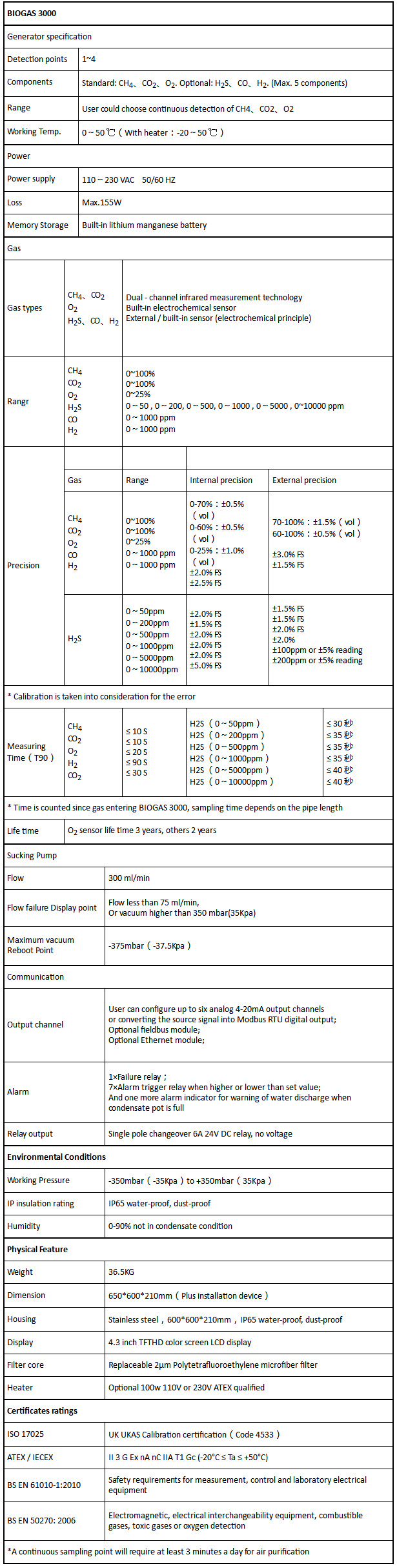
PLC Automatic monitoring&Controlling System
We can provide PLC monitoring and controlling system for the complete waste - biogas - energy plant. A complete PLC system is composed of two parts: Hardware modules and software modules. It can realize the real-time monitoring and automatic/manual controlling of the whole project. Real-time understanding of the operation status of the whole project helps improve the precision of regulating and controlling, to increase the efficiency of biogas production and stability of plant running.
Hardware:
Sensor, PLC controller, Actuator, Network communication module, PC, etc.Software:
PLC software, on-site configuration software, Internet remote control software, etc.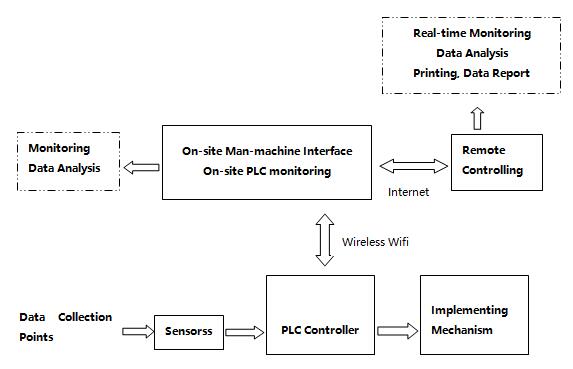
The sensors and PLC are serial-communication connected. The sensors collect data from different points of the entire plant and convert these physical values into analog, then transfer them to PLC channel. The PLC collects and process these analog signals from the channel terminals transmitted by the sensors and store in the database for analysis.
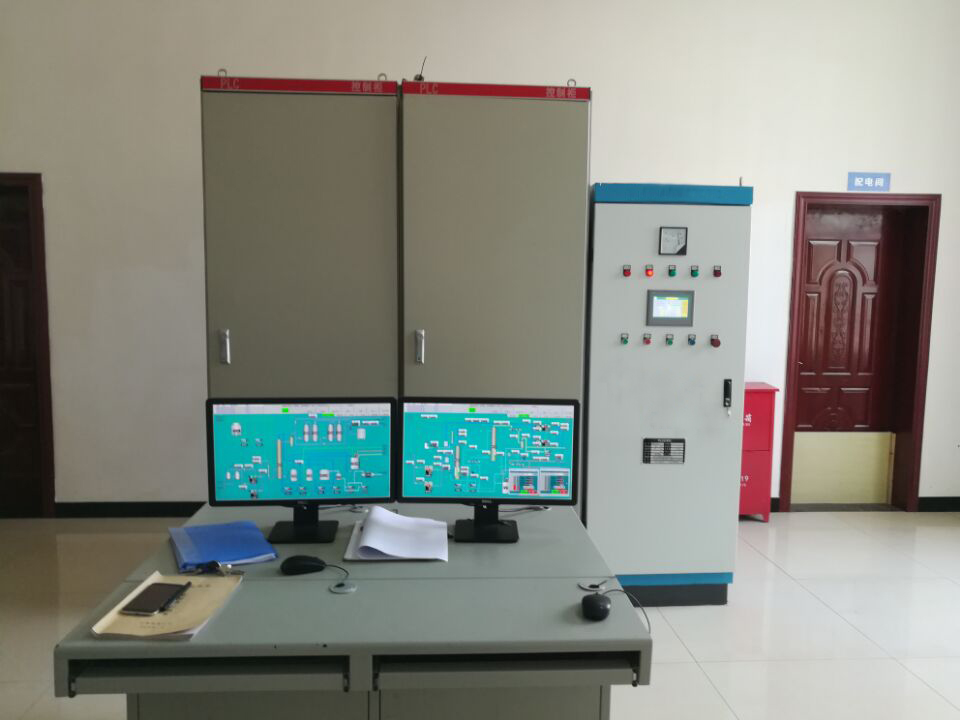
The implementing Mechanism is divided into Automatic and Manual operations:
1. Automatic mode:
The system receives PLC instructions combined with order from principal computer, to achieve the purpose of automatic controlling and regulating;2. Manual mode.
Staff manually operate the machine&devices according to the working status indicated on the computer or MMI;According to the project process, data collecting points can come from:
1. Anaerobic tank:
Temperature, pH, liquid level, gas tank pressure, ORP, etc;2. Biogas storage:
Gas components, flow, pressure, temperature, etc;3. Biogas treatment:
Pressure, temperature, liquid level, flow, gas components, water dew point, etc.Air Flotation System
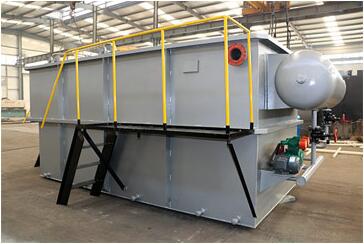
YW series air flotation system is used for separation of solid-liquid or liquid-liquid. It’s dissolved air type, working principle is that by means of conversation of soluble organics into unsoluble matter by coagulant and flocculants, the resulted suspended solids is removed by scraper so as to purify the water.
The quantified waste water enters into the air flotation mixed zone, in contact with the water full of dissolved air, thus make the flocculants adhere to the micro-bubble and then flows into the air floating zone. The flocculants rise to the surface of water as scum, some of the water reflows as the dissolved air water and the other flows into the clean water pool. The scum will be cleaned by the foam scraper.
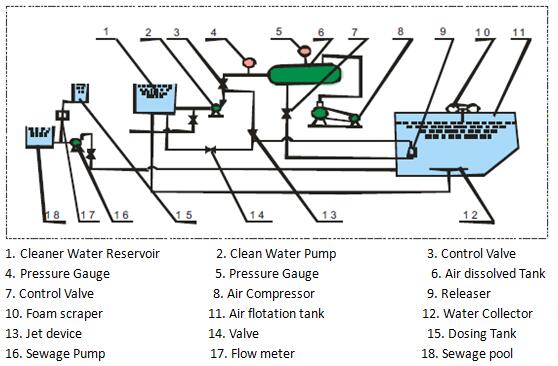
Parameter Table for selection:
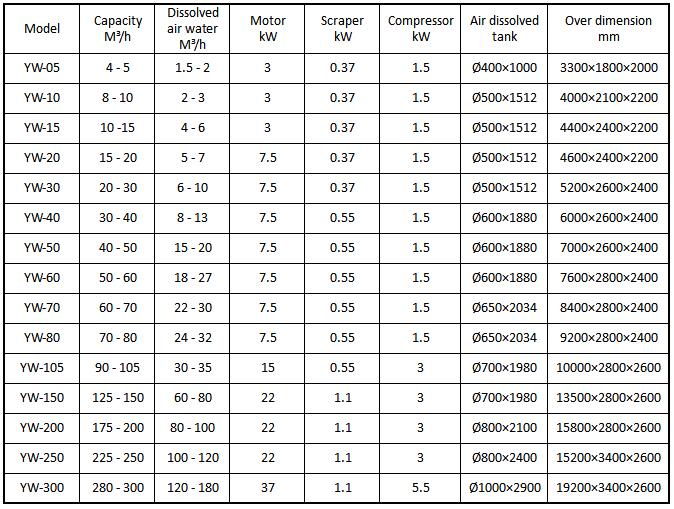
MBR Membrane Bioreactor

Membrane BioReactor(MBR) is a new type of waste water treatment technology, a combination of high efficient membrane separation and activated sludge process, suitable for municipal or industrial sewage with high organic content. It works instead of traditional secondary sedimentation tank for removal of suspended solids and the removal rate of nitrogen and degradation of organic matter could be greatly improved.
MBR is a kind of simple operation, highly automated technology of sewage treatment under modular design, has the following advantages:
1.Less area occupation;2.Can maintain a high MLSS value (<15g / L) and longer sludge residence time (<60 days);
3.The quality of output water is stable;
4.Less sludge rest, reducing the cost of sludge treatment;
5.Low energy consumption, simple cleaning and low operation cost.
A2O System
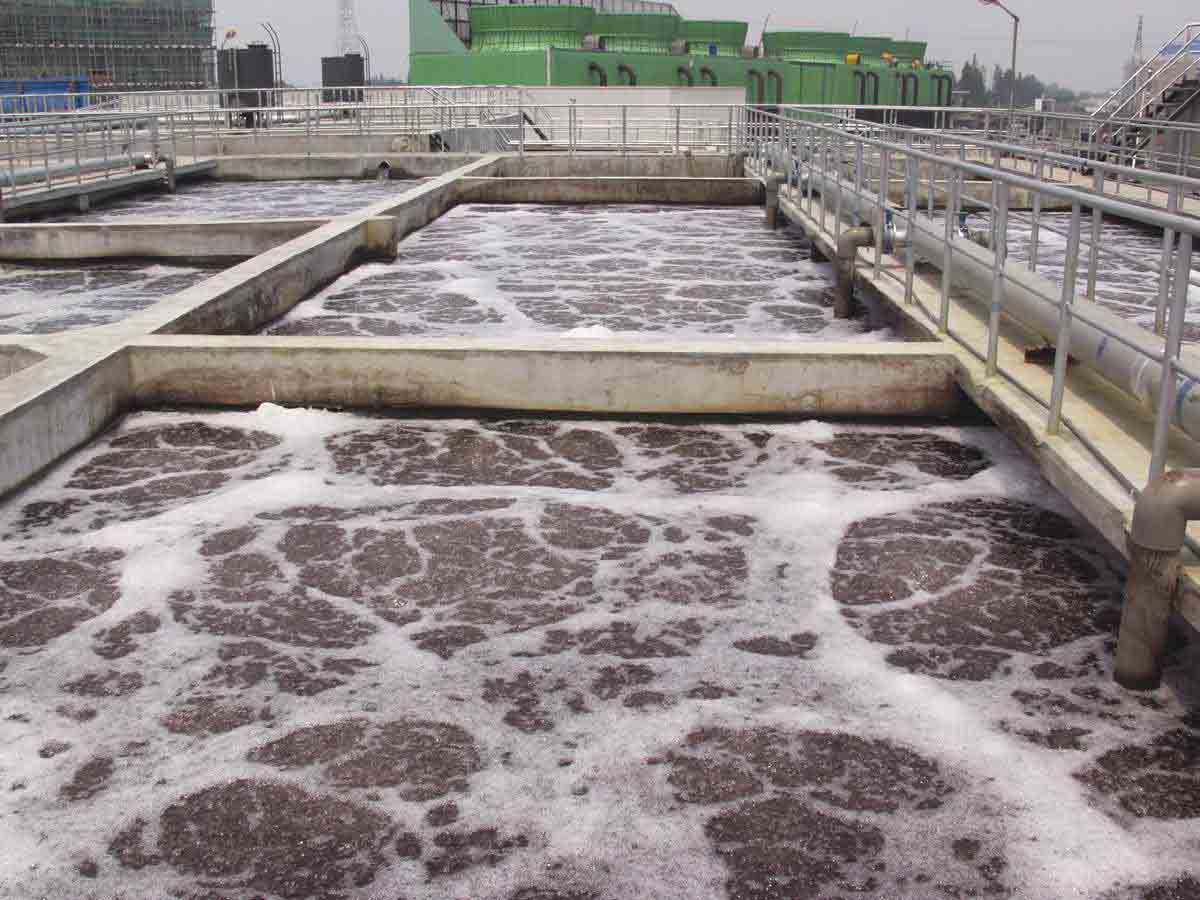
A2/O (Anaerobic/Anoxic/Oxic) sewage treatment system, is a kind of biological processing technology, high adaptability for different sewage quality, good anti-load performance, stable output quality, no expanded sludge output and low operation cost.
The A2 / O process is divided into anaerobic, anoxic and oxic segments. The anaerobic and oxic segments are equipped with biological fillers for microbial metabolic activities, along with reactions of hydrolysis and acidification of COD/BOD. Blower and aeration system are installed in the oxic segment, the decomposed organic substance is absorbed by means of aerobic bacteria’s metabolism, to achieve the purpose of water purification.
The material and equipment involved in this system are chemical packings and support, chemical additive, air blowers, aerators, overflow weirs, level controller, steady flow tube, agitators(optional),pumps, valves, pipes, connection fittings, filter press, etc;
The flow-chart of A2/O system(If get air flotation system included ahead of A2/O):
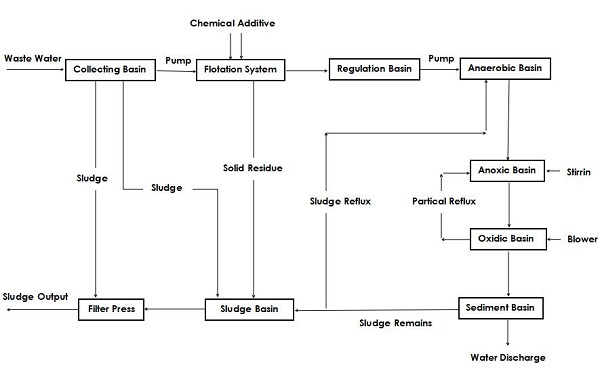
Civil works involved include anaerobic pool, anoxic pool, first biological pool, secondary biological pool, secondary sediment pool, sludge basin, disinfection pool and blower room,etc. Equipment involved are fillers&support, blowers, aeration system, sludge press, pumps, pipeline, chemicals and so on.
Sometimes simpler design is also suitable, eg. A/O(Anoxic / Oxic) only, in accordance with the characteristics of sewage quality and design requirements.
PC-MBR
PC-MBR(Plate type Ceramic membrane bioreactor)
PC-MBR is a kind of system for sewage purification and filtration by using nano-plate ceramic membrane modules. The main advantages are: high efficiency, long life time, high degree of automation , Small area occupation, low operating costs and so on, especially suitable for the sewage treatment plants at towns, residents, concentrated areas, schools, hospitals and tourist sites. It can save a lot of investment in pipe network construction, is a very good solution for those decentralized sewage treatment.Advantages of PC-MBR
1) The plate ceramic embrane flux is relatively high, per square membrane flux is ranged at 15-60L / H (flux according to sewage conditions).2) The internal design is multi-channel microcirculation to ensure that the sewage would be processed under many steps of internal nitrification and denitrification, making better treatment effect.
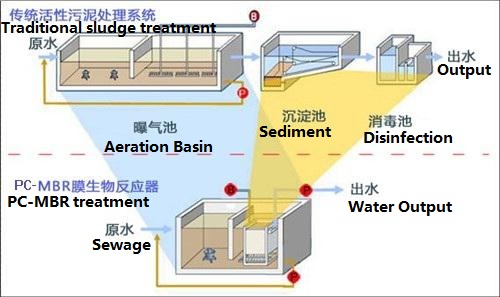
PC-MBR Project References
Example #1:100 tonnes/d rural sewage treatmentLocation: Changfeng, Pingxiang, Jiangxi Province,China
Project effects
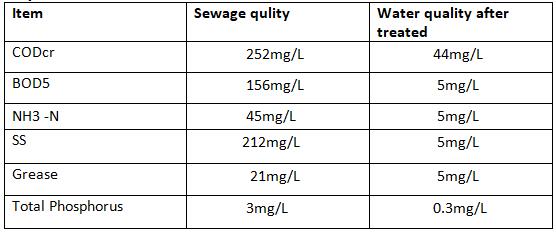
Colibacillus in the water after treated ≤100 pcs/L
Feature of sewage quality:
- High ratio of B/C;
- C:N:P = 100:5:1;
- Good biodegradability;
Figure: Treatment capacity: 100 tonnes/d PC-MBR system
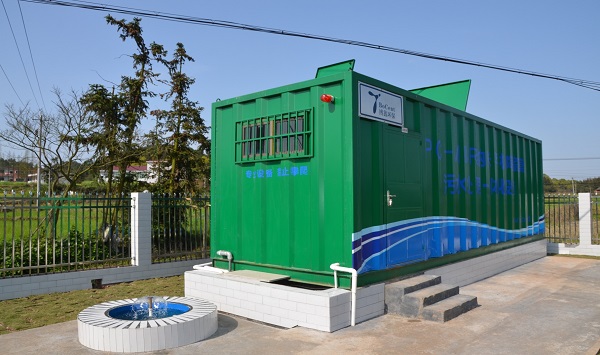
Figure: Treatment capacity: 50 tonnes/d PC-MBR system
Example #2:50 tonnes/d rural sewage treatment
Location: Changfeng, Pingxiang, Jiangxi Province,China
Project effects
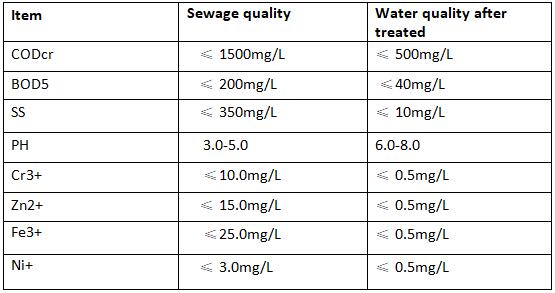
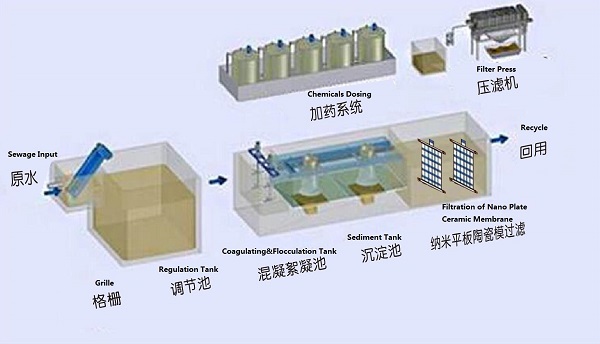
PC-MBR features
- Membrane flux is relatively high;- Non-blocking;
- High degree of automation, easy maintenance;
The whole system adopts computer program control, automatic operation, to improve processing efficiency;
- High efficiency for oil removal
Grease content in the water above 1000mg/L, it can reach about 15 mg/L after treated, the removal rate of up to 98% or above.
AR Series Blower
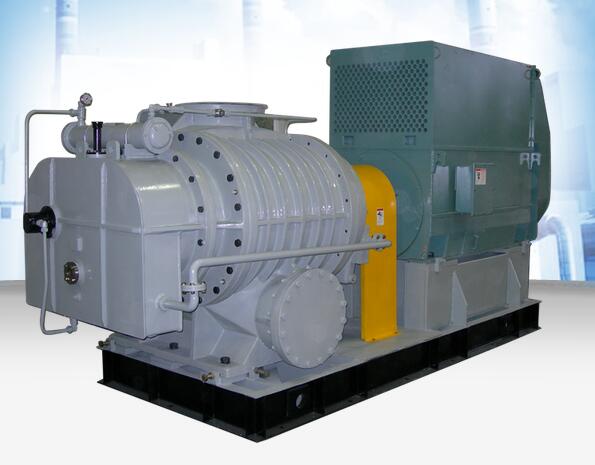
AR Series Rotating Blower is a high quality lifting machine for gas transmission. It features the highest level of gas blower manufacturing in China, normally combined in our biogas pretreatment system and improvement system to increase pressure and regulation of biogas or landfill gas.
Product Features:
1.The forced gas supply, the gas flow becomes smaller under the operating pressure. And gas transmission is free from oil pollution;2.Adopt double cyclooid blade profiles or advanced design in aerodynamic theory make effective blower and energy saving;
3.High precision of dynamic rotor balance cause low vibration;
4.Selected parts, high precise gear, high reliability for the whole machine, long life time;
5.Equipped with special designed muffler, low noise operation;
6.Simple structure, beautiful shape, easy operation and maintenance;
7.A variety of types available according to different working conditions, the intensive performance advantages make the model selection easy in a power saving way;
8.The AR series can be extended to other models such as AR-K, AR-M, AR-N, etc. For special purposes of sucking or transporting different gas media for different types of industrial uses.
Flow: 0.76 - 1200 m3 / min;
Pressure: 9.8 - 98 kPa;
Motor power: 1.1 ~ 1.250 kW.
NSR series Blower
NSR series roots blower has high cost-performance. Under mature technology, it is widely used for biogas or air boosting and transmission in our GasCle systems and oxidation systems.
Main Parameters:
1.Pipeline size Ø40 - Ø300mm.2.Gas flow 0.35 - 132 Nm3 / min.
3.Operation pressure 9.8 - 98.8 Kpa.
4.Motor 0.75 - 280 kW.
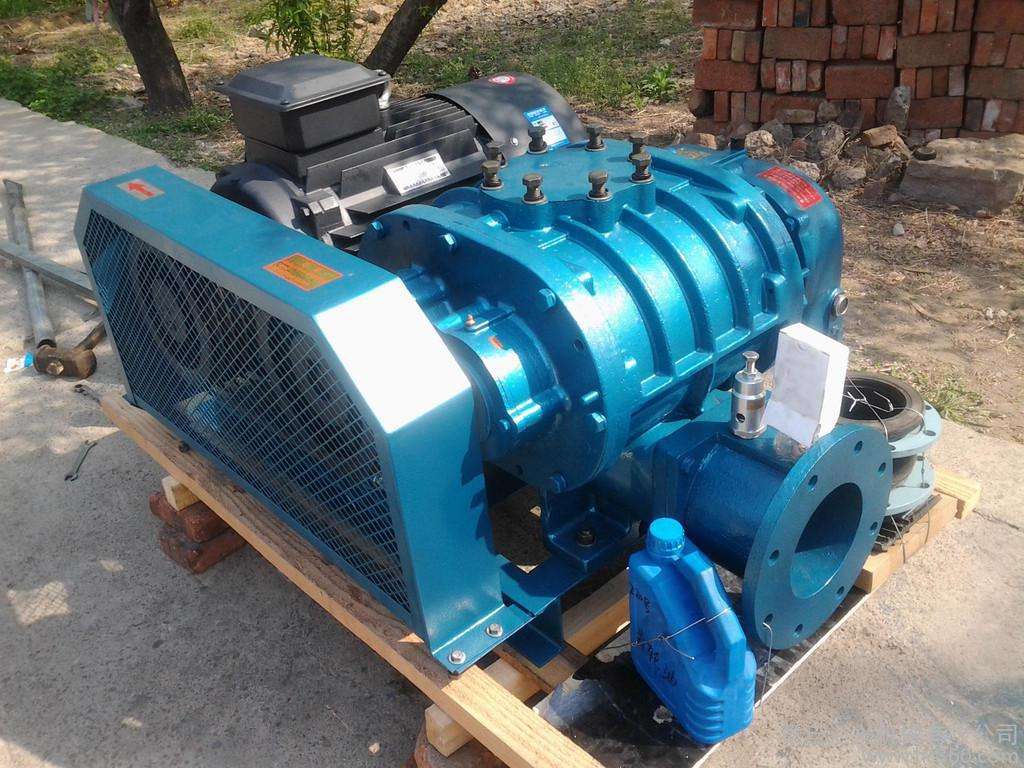
Structure features:
1.There are two sets of 3-blade impellers inside the case, driven by a pair of synchronous gears to do reciprocating movements in the opposite directions. The rotation of impellers originates gas pressure. A certain gap reserved between impeller and housing, no friction for long-term operation;2.Fixed helix of 20° or more. Special design of gas strength for inlet and outlet causes less noise and almost no exhaust pulsation;
3.Rotor is 3-blade straight type, just needs to ensure a certain gap between the rotors on the cross-section, efficiency is much higher than the same-size rotor spiral blower;
4.The design for special shaped rotor can easily maintain the gap between rotors, to get a good efficiency improvement;
5.The mass production of rotors by precise CNC machine under a set of strict precision management makes no performance differences of blowers produced. Rotor has been in a balanced state in manufacturing process, so that almost no vibration caused when blower running;
6.Adopting the most advanced driving gear produced by using special Cr-mo steel through appropriate quenching, in strict accordance with JIsI-class precision.
7.Clean gas output, no grease and dust. No lubrication oil inside housing. And special structure stops bearing and gear oil entering the internal housing.
8.Advanced company management system ensures that we can delivery goods within the contracted delivery time.
Material description for main parts:
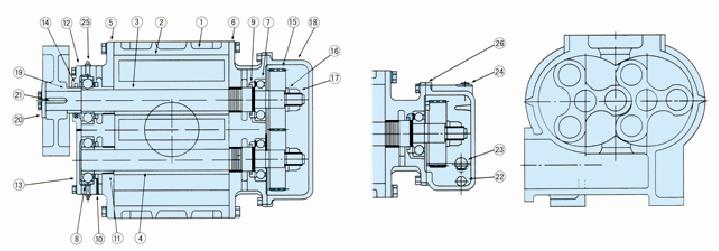
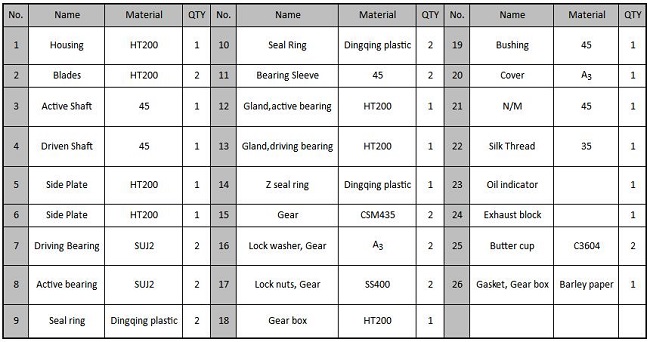
Gas Compressor
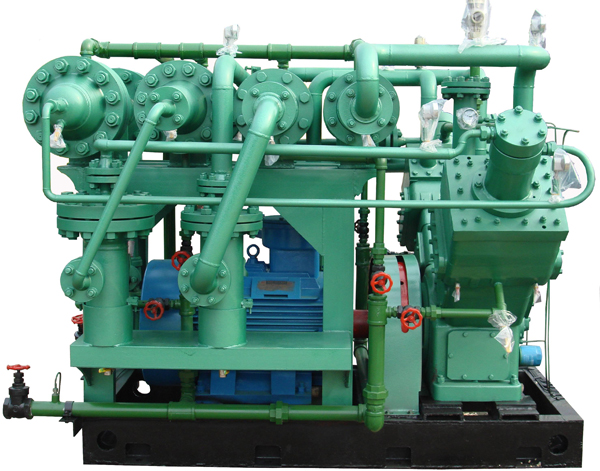
We can provide selected gas compressors for compression of biogas and natural gas under different pressure ratings. Machine quality has been proved many times in our actual projects. They are mainly used in our biogas upgrading projects for Making CNG or pipeline gas. Clients need to advise detailed requirements when inquiry, such as the gas flow, inlet/outlet pressure, biogas composition and temperature.
Parameter Table for Selection:
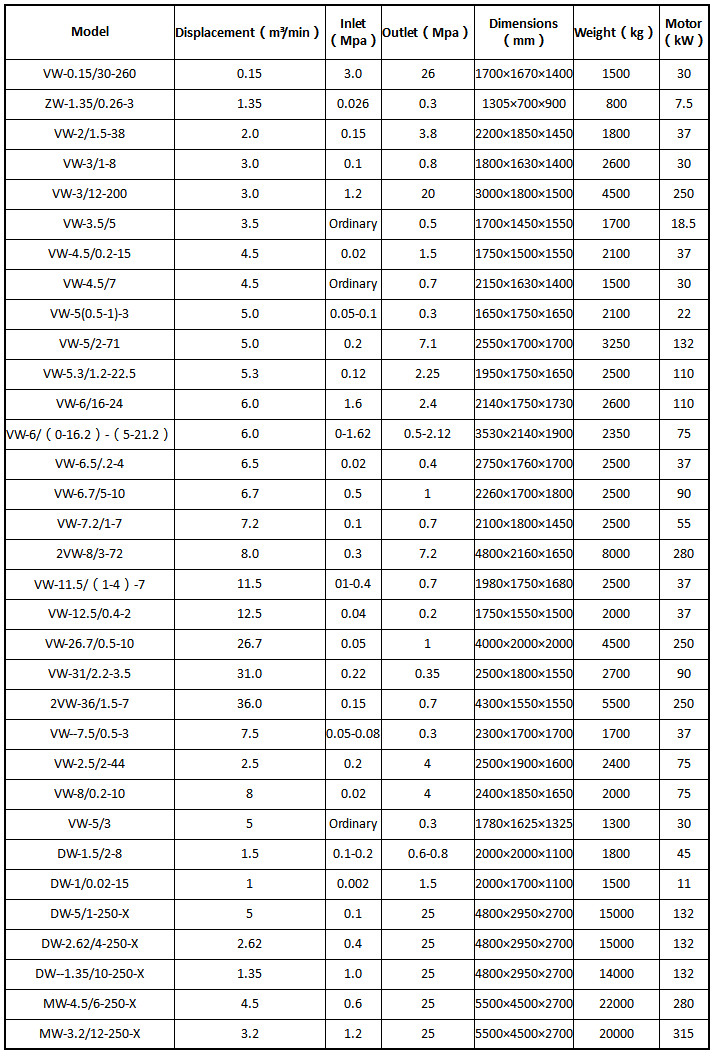
Progressive Cavity Pump
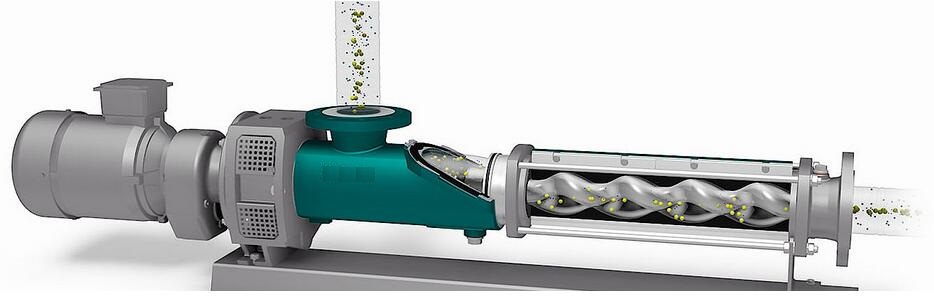
Our G series single progressive cavity pump, main components and characteristics are as follows:
1.Rotor. Using the most advanced grinding and polishing process, improve the performances of wear resistance, hardness characteristics and corrosion resistance, to extend its service life-time;2.Stator. Both ends with sealed flanges, to make rotor and the launcher fully cooperated to improve work efficiency;
3.Shaft seal. Customers can choose the sealing methods according to the specific conditions. Standard configuration is mechanical seal;
4.Feeding port.
5.Outlet. Using wear-resistant materials;
6.Motor. Variable speed motor, explosion-proof motor for optional;
Features of G series single screw pump are as follows:
1.Wide range of applications. Materials with TS% up to 60% and concentration up to 1,000,000CPS can be transported effectively;2.Low mechanical vibration and noise, without agitation, shear, turbulence and stirring in transmission;
3.High self-absorption ability, suction height on the vacuum up to 8.5 meters.
4.The unique structure of rigid rotor plus resilient stator makes it possible to transport solid particles;
5.The temperature of the material to be conveyed can be up to 120 degrees Celsius, the flow rate up to 500m3 / h. Pressure up to 9.6 MPa;
6.Flow and speed are in a strict linear relationship, adjusting the speed to control the flow, usually used as metering pump;
7.The hardness of stainless steel (304,316,316 L, 904,329J1, etc.) rotor could reach HRC55-60, after special physical&chemical treatment, to make high performance of corrosion and wear resistance.
Parameter Table for Selection:
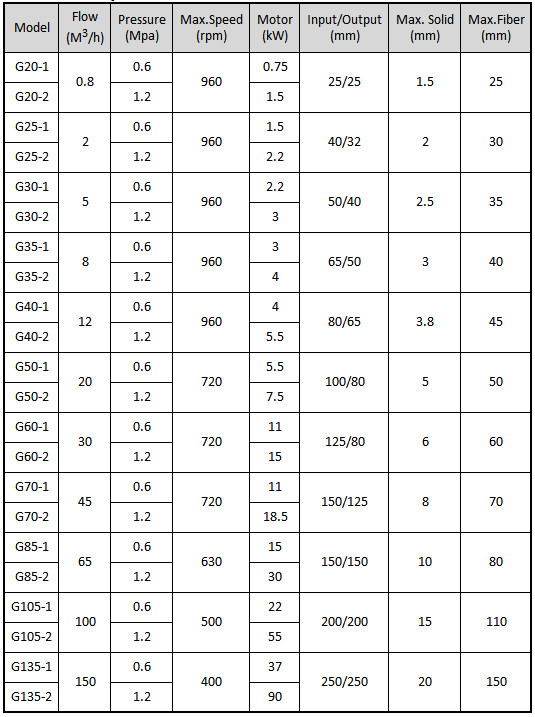
Grinding Pump
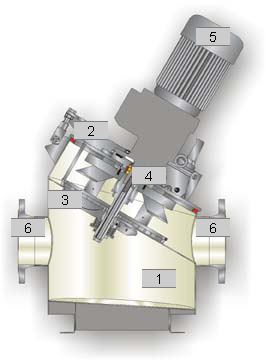
Maximum flow could reach 300 m³/hr
Maximum Total Solid content allowed could reach 10%
Structural design for M-Ovas® series Grinding Pump:
1,Cavity
The housing is equipped with a sandstone settling chamber in accordance with the principles of hydrodynamics,with a upper-positioned hole for cleaning. Open the cover of hole,the sedimentation can be easily removed. The housing is galvanized or made of stainless steel to prevent corrosion.2,Cover
The chopper is integrated on the cover. There is a cylinder on the cover used for assisting in opening the cover. In this way, it is more convenient to clean up the solid material in the settling chamber.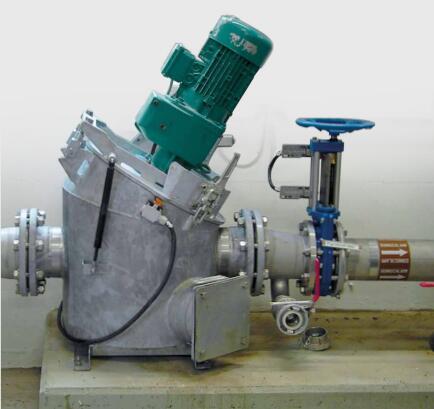
3,Chopper
The cutter blade is made of wear-resistant hardened steel. The chopping performance is optimized by the cutterhead with the automatic adjustment of the blade mechanism. The blade is made of wear-resistant hardened steel. The flywheel supports the chopping operation and reduces the power consumption of driving. Cutters and blades can be replaced easily and no need of disassembly of pipe fittings.4,Axis Sealing
Mechanical sealing of Lubrication quenched hardened alloyed steel end to prevent material leakage.5,Driving Device
Standard drive is equipped with heavy-duty bearings.6,Pipe Connection
The entrance&exit are located on the same level. Pump can be connected directly to a horizontal pipe or on a 90 ° flange with an NEMO® pump.Rotary Lobe Pump
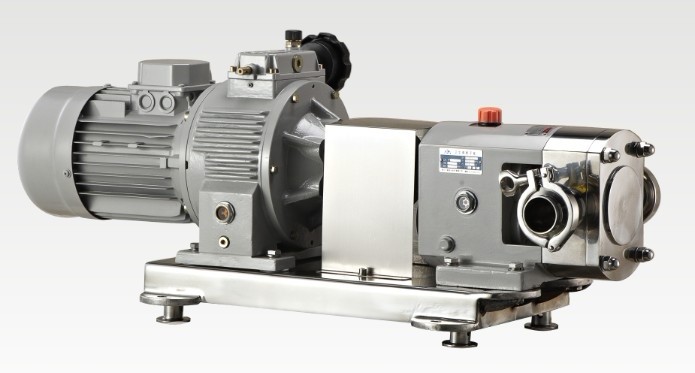
Our LQ series rotary lobe pump has the following characteristics:
1.High-precision rotor and unique design of low shear force ensure the highest sanitary grade under the premise of no damage for media in the transmission process;2.Standardization of products not only increased the flexibility of combination of involving parts,but also caused sufficient stock;
3.Flexible design on input&output locations horizontally or vertically, offer custom-made service,to provide customers with real convenience;
4.Perfect design enables customer to clean for drainage more conveniently;
5.Flexible design of connections,to meet customers’ multiple requirements;
6.High-quality transmission for customers to do various regulations according to different working conditions;
7.With CIP and SIP sanitary standards.
Parameter Table for Selection:
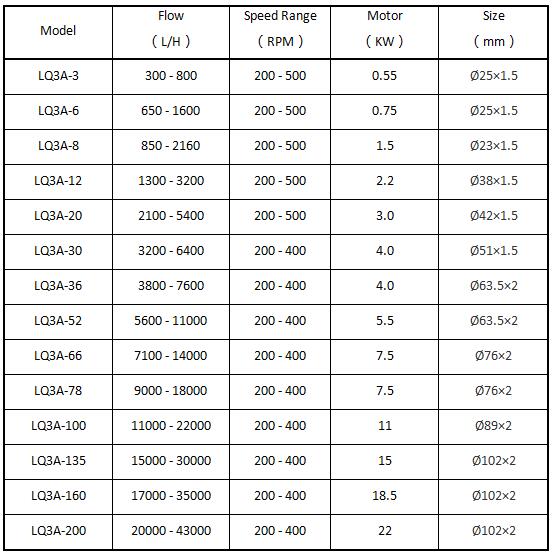
Drain Pump
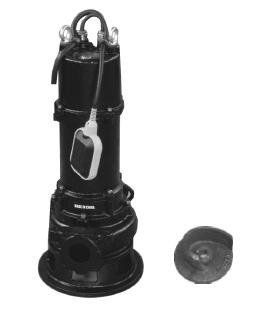
Our CP series of drain pump,researched and produced by joint-venture factory of Australian CLEAR company in China, mainly used for sewage drain, has the following advantages:
1.The design of large-channel single-leaf anti-clogging impeller enables solids particles with diameter of 25~80mm could get through pump effectively;2.Reasonable design with high performances of anti-blocking and anti-winding, impeller attached with hard alloy knives could laniate the large particles and long fibers;
3.In line with the latest international pump design,excellent anti-corrosion and sealing cables,the overheating protection devices of motor.The water leakage detector can automatically cut off power to protect the pump. Two sets of mechanical sealing in series and high-quality castings.All these features could guarantee reliable running of pumps continuously;
4.Compact structure,easy movable,easy installation.No need to built special pump room,to save project cost;
5.Dual-rail automatic installation system,to make installation and maintenance real convenient;Worker doesn’t have to enter the water basin;
6.AUTOMATIC and ORDINARY types of pumps below 4KW available for customers’ choice.For AUTOMATIC type,built-in motor overheating protection,leakage detector and water level switch provide protections in case of over-loading,leaking.The opening and closing of pump could be automatically controlled by the water level switch,no need to connect outer controlling devices,to avoid pump burning resulting from ineffective manual care and abnormalities.ORDINARY type doesn’t have the above functions,need to be connected with external control cabinet.
7.Material: pump body (HT200); shaft (304 stainless steel); impeller (HT200); fasteners (304 stainless steel).
Parameter Table for Selection:
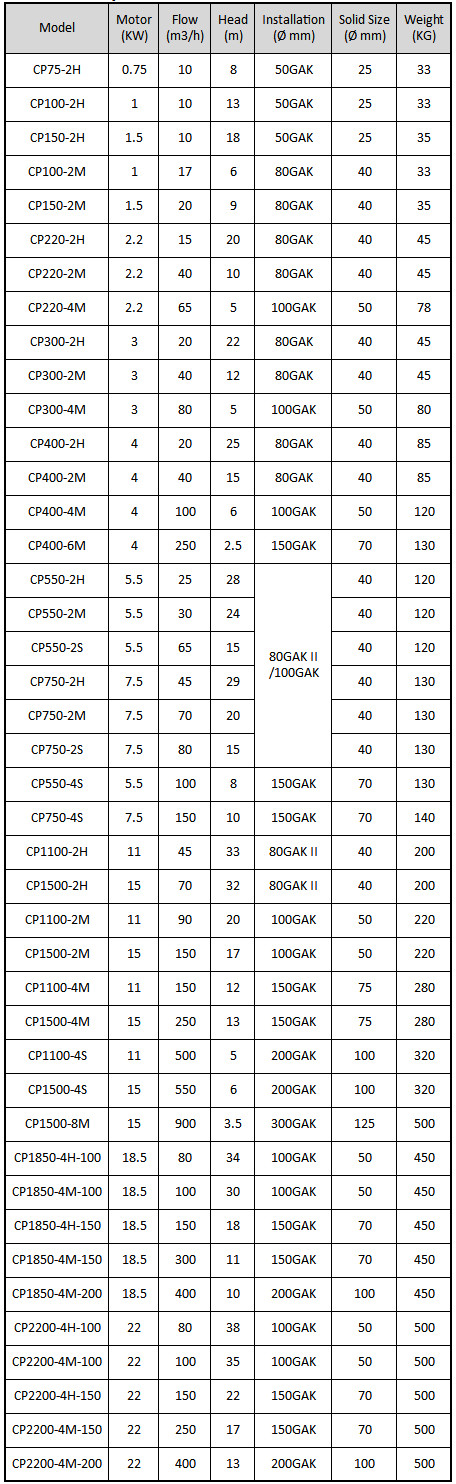
Comments:
1,Single-phase available for CP50,CP100 and CP150;2,AUTOMATIC and ORDINARY types available for choice.
Sewage Pump
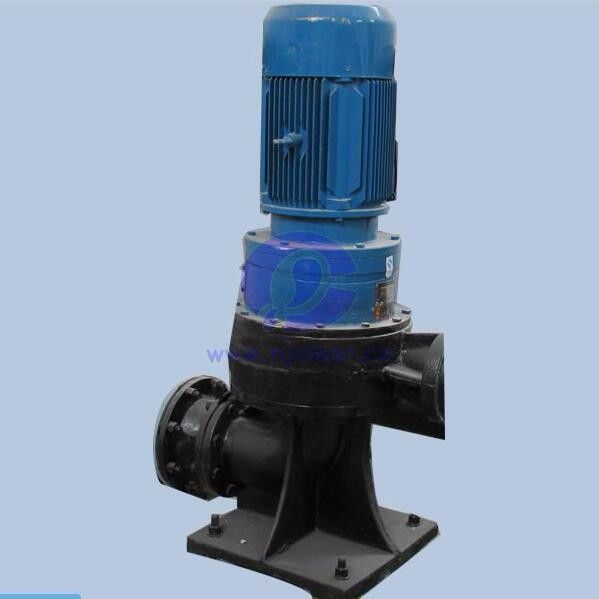
Our WL series of sewage pump,researched and produced by joint-venture factory of Australian CLEAR company in China, has the following advantages:
1.With structure of single(double) flow channel or single(double) blades,no clogging hydraulic design,smooth operation,little vibration,can achieve automatic controlling;2.The utilization of imported bearing,mechanical sealing and Stainless Steel shaft guarantees the excellent performance of pumps;
3.Flow 20 - 4000m3 / h; Motor 4 - 250KW; Head 6 - 54m; Particle size 25 - 300mm; Output size 65 - 500mm;
4.Working Conditions: PH 5 - 9; Water temp not higher than 45 degrees Celsius; Solid weight not more than 25%.
Parameter Table for Selection:
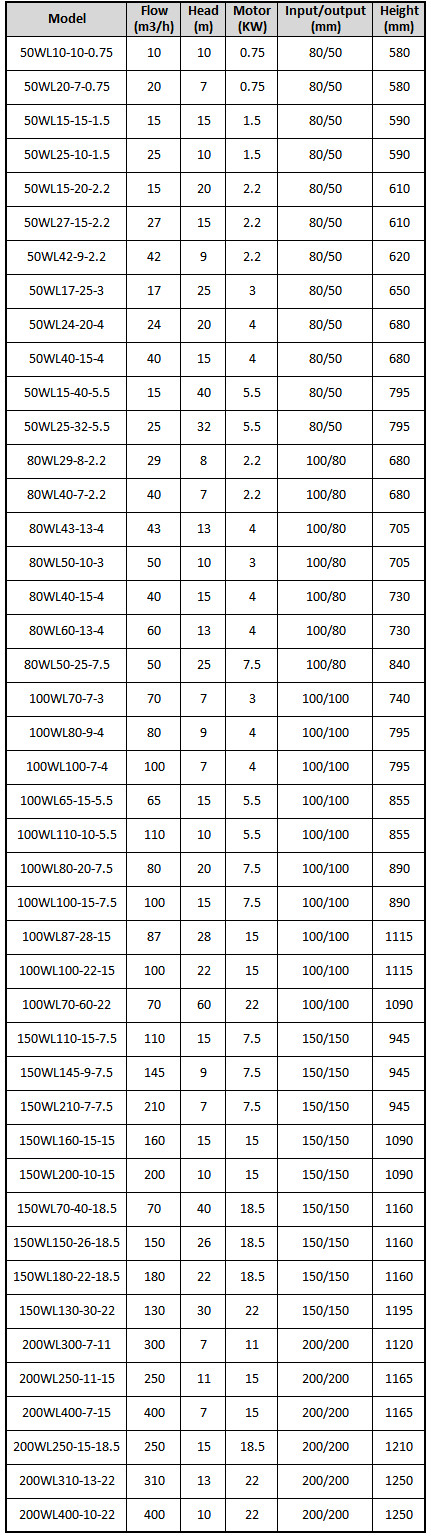
Shredder
We can provide ETS series of high-quality double-shaft shredder, produced by a wholly-owned subsidiaries in China of a French brand with 30 years history.
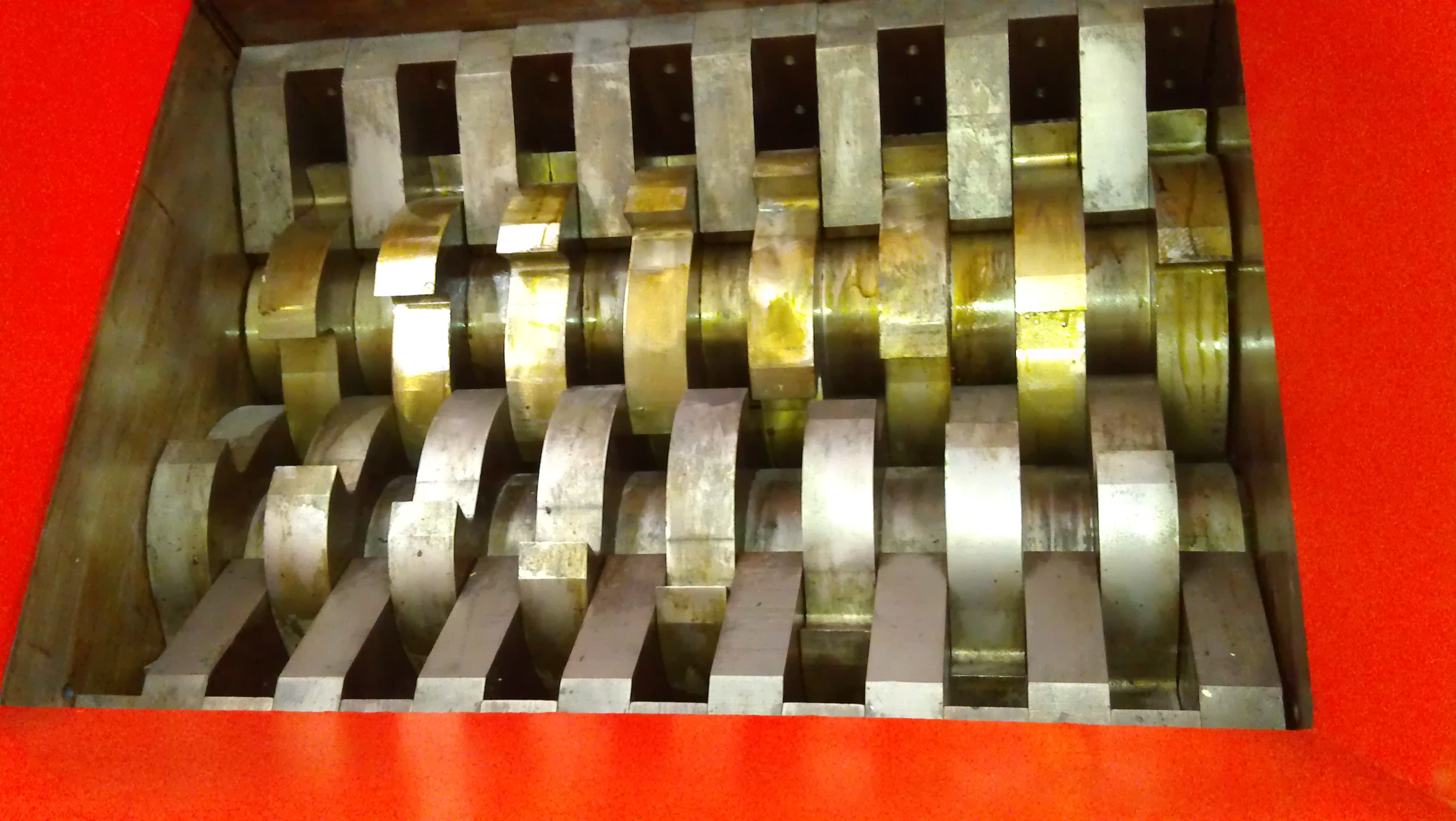
Structural characteristics:
1.Feeding hopper.
Special design of the feed hopper could prevent material splash when working. Equipped with large feed port, convenient for forklift or conveyor to feed. Specially designed hopper shape to meet the special needs and to ensure continuous feeding, simple operation, without any manual operation.2.Rotor.
The strong durable rotor surface is concave designed according to different types of feedstock. Two-side replaceable rotary knives are installed on a special seat.3.Rotor bearing.
The solid bearing block is mounted outside of machine, separate from the crushing chamber to prevent invasion of impurities, prolong machine life-time and reduce cost of maintenance.4.Screen.
The screen for sieving is mounted under rotor, its aperture is designed in accordance with the solid size after shredded as required(10~40mm). The hinged sieve frame facilitates the disassembly, the replacement is easy to operate, or the screen is not required.5.Driving device.
The motor and gearbox are linked by helical gears, driven by a large gearbox mounted on the top of spindle.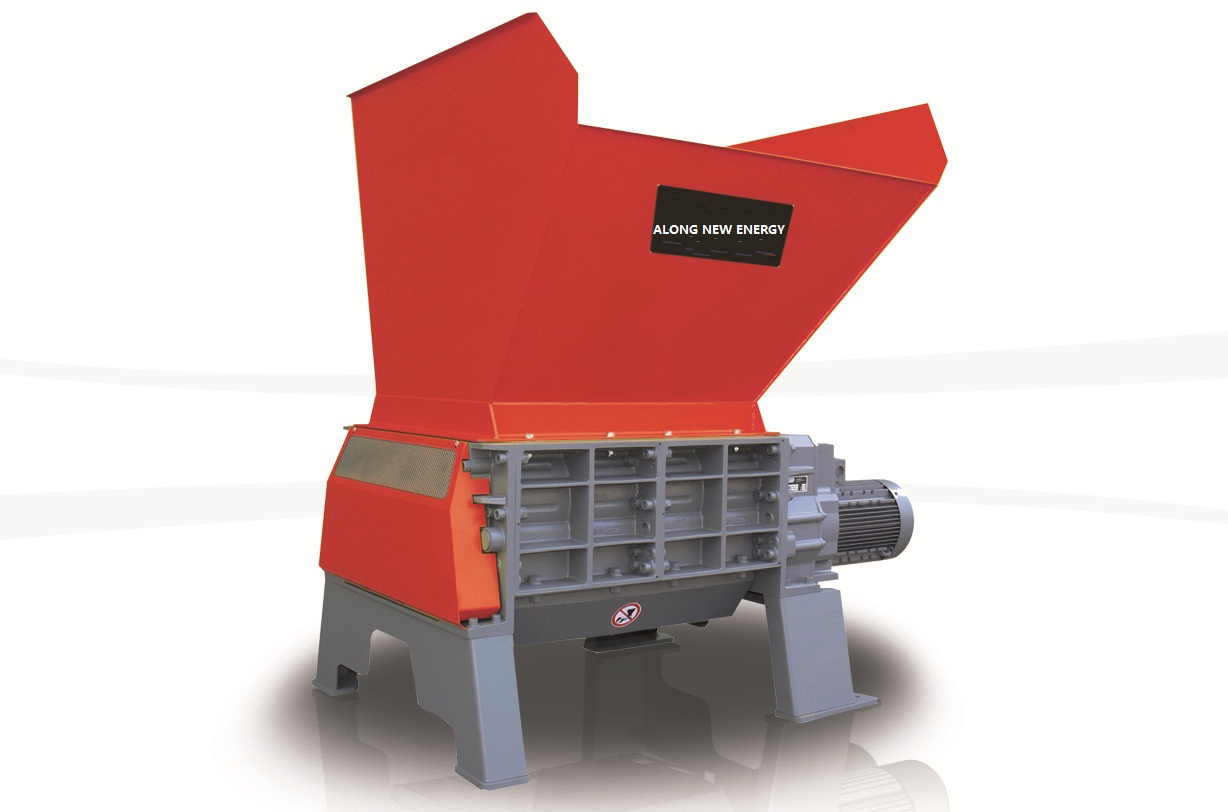
Configurations of the main parts of machine:
1.Electrical components: Siemens or equivalent;2.Indicator: Siemens or equivalent;
3.Power: Adopt print line numbers, only provide primary size power access port, with standard alignment;
4.Operation and maintenance is a chain relationship, shredder can’t work when repairing or can’t repair when working;
5.Electric control box: Dust-proof and water-proof;
6.Brand: German Rittal or equivalent;
7.Indicators: DC24V, LED type;
8.Control buttons: DC24V voltage;
9.Motor brand: Germany WEG or equivalent;
10.Reducer brand: Boneng or Guomao;
Parameter Tables for Selection:
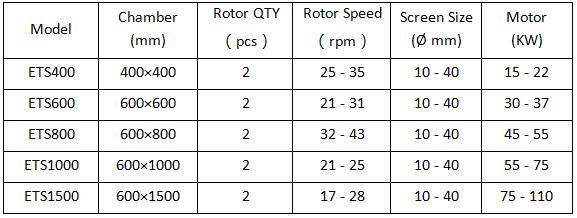
Comments:
Warranty is 1 year;Hammer Crusher
ZTBC series of hammer crusher consists of hopper, rotor, screen, rack, electrical components,etc; The feedstock (eg, fruit and vegetable wastes) is fed into the crushing chamber, under the actions of high-speed rotor and screen, the crushed waste is forced to push through the screen and fall into collector or transported to the designated place.
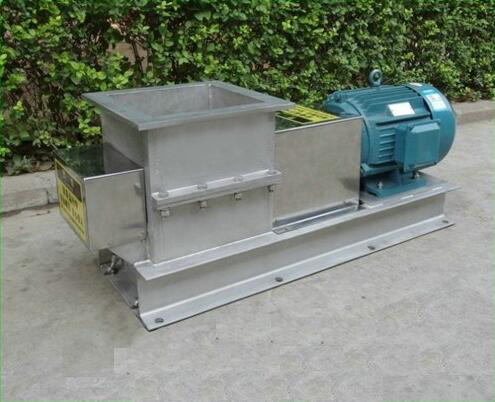
Product Feature:
1.Low noise, big processing capacity, low power consumption, no intertwining, no knife sticking, no blocking, easy maintenance;2.No turntable design can avoid the generation of iron scrap resulting from relative movements;
3.Wide application; The screen is not easily blocked, it is suitable for those waste with high content of fiber, such as vegetables, biomass,etc; It’s convenient to take the screen off and clean it;
4.The screen size can be minimized at 0.5mm;
5.Tight structure design, easy operation, has protection of over-load;
6.Sandblasting treatment to make good appearance, Modular detachment, especially to clean;
The below waste can be crushed:
1.Vegetable waste, Such as Bean sprouts, celery, cabbage, carrots, ginger, potatoes, etc;2.Fruit waste, Such as Apple, pear, kiwi, pineapple, etc;
3.Nuts, Such as Mangosteen, Tremella, etc;
4.Fine crushing of powdery waste from feed mill, food industries, alcohol plant,livestock farms;
5.Food waste, animal pluck,overdue food in supermarket,etc;
Parameter Table for Selection:
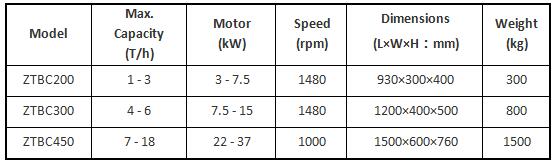
Knife Gate Valve
Z673H series slip type pneumatic knife gate valve is a kind of important control valve in the plant production process. Switch controlling can be reached through solenoid valve, and the performance of flow adjustment could be achieved through a positioner of electrical valve. Users can choose the optional items according to actual needs.
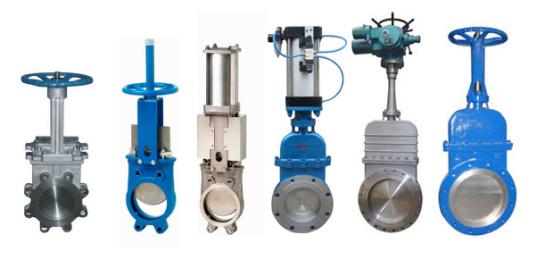
Product features:
1, The lifting sealing surface of gate enables adhesive to be scratched off automatically;2, The use of stainless steel of gate could effectively prevent seal leakage resulting from corrosion;
3, Kentanium sealing surface to ensure good performances of wear resistance;
4, No grooves on the sealing surface of valve body to cause accumulated objects makes opening flexibly;
5, Short length of structure to save raw materials and space for installation is also effective to support the pipeline strength;
6, Scientific design for packing of upper sealing makes seal safe,effective and durable;
7, The design of triangle holder to save raw material and ensure the mechanical properties;
8, The guide block ensures the correct movement of the gate, the four press blocks ensures effective sealing for the gate;
9, The reinforcement design for valve body improves its strength;
10, The stainless steel valve stem is durable, the double-headed bolts make opening/closing quickly;
11, The types of driving mechanism can be chosen freely;
12, For valves bigger than DN150, complete sealing makes opening more effectively and prevents leakage;
13, Fluorine rubber sealing surface can achieve sealing effect and improve operation temperature;
14, The rubber sealing surface is directly vulcanized in the valve body and won’t fall off;
15, Compact design to occupy a small space; Light, cheap, easy installation, wear resistance, anti-blocking, easy maintenance, easy operation and long life-time.
Product specifications of the selection (knife gate valve):
1. Operation: hand wheel, manual zipper, spur gear, bevel gear drive, pneumatic and electric.2. Connection form: Flip type, flange type.
3. Sealing material: metal-to-metal hard seal, metal-to-polyurethane, with enhanced Teflon soft seal.
4. Applicable medium: farm waste water, industrial organic wastewater, mud, slaughterhouse wastewater, sedimentation tank, wood pulp, fiber, ore, pulp, biogas and so on.
5. Pipeline size: DN50 ~ DN1200.
6. Operating temperature:
Soft seal (PTFE): - 40 ° C to 180 ° C
Carbon steel: -29 ℃ ~ 425 ℃
Stainless steel: -40 ℃ ~ 600 ℃
Chrome molybdenum vanadium steel: ≤550 ℃
Working pressure: 0.6 ~ 1.6MPa
Material Description for individual parts of valve
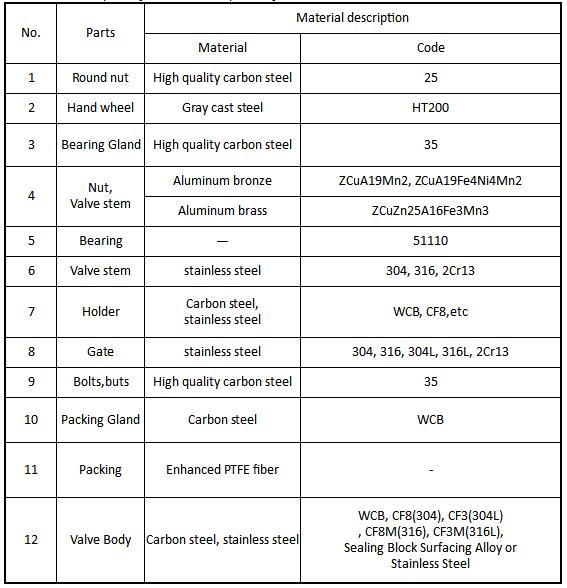
Comments:
Depending on the operating conditions, it can be equipped with an electromagnetic valve, triple air parts, limit switches and positioners.Butterfly valve
D673H series of pneumatic slip-connection hard seal butterfly valve is used for flow regulation and cut-off of fluid in the pipeline of water supply and drainage in the fields of food, medicine, petrochemical, power plant, steel mills, industrial water treatment and high buildings.
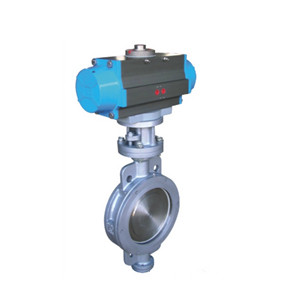
Product features:
1.Adopting three eccentric sealed structure, nearly no friction between valve seat and butterfly plate, with high performance of better sealing if closing tighter;2.The use of stainless steel as material of seal ring, with double advantages of metal hard seal and flexible seal. Sealing performance is good under conditions of low or high temperature. With features of wear resistance and long life-time;
3.Cobalt-based surfacing hard alloy for the seal surface, with features of wear resistance and long life-time;
4.Large butterfly plate is hanging structured with high strength, big open area and low resistance;
5.The valve has two-directions sealing, unconstrained by flow direction, nor by spatial positions;
6.The driving device can be installed in multiple stations (90 ° or 180 °) for convenient operation;
7.Connection ways for option: Flange, double-clip, butt welding, lug-slip;
8.Driving devices for option: Manual, worm gear, electric and pneumatic;
9.Pipeline size: DN50 ~ DN1200;
Material Description for individual parts of valve:
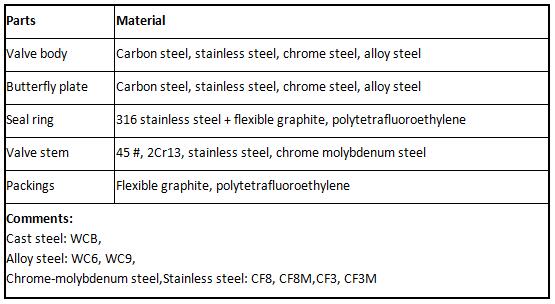
Ball Valve
Q641F series of Pneumatic stainless steel ball valve:
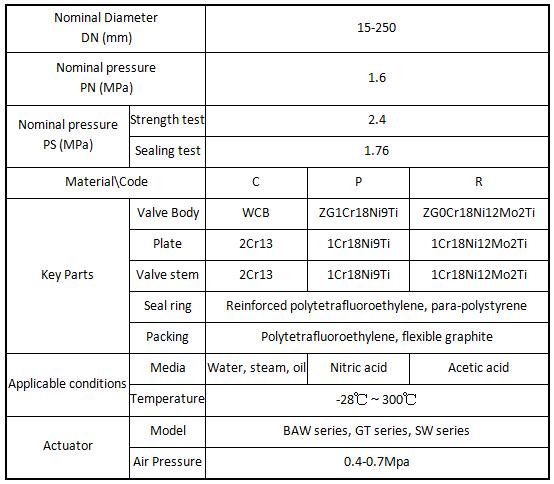
Comments when order

2. Based on pipeline design to choose reciprocating(two switches) or spring reset (normal opening/closing);
3. Controlling accessories for option: Single electronic controlling solenoid valve (Power-off normal opening or closing); Double electronic controlling solenoid valve (Switching); Valve location sensor; Air handling FRL, anti-explosion type can be chosen in special conditions.
Normal Dimension and Actuator:
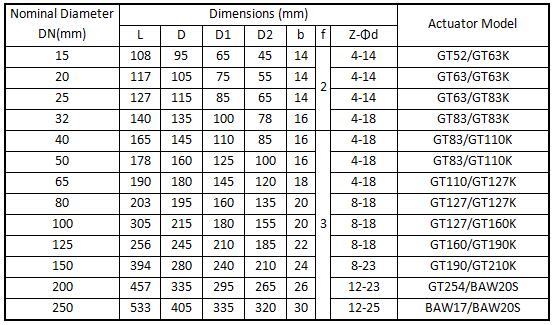
Flame arrestor
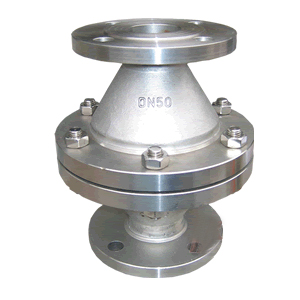
Product Name:
Flame arrestorApplication:
Widely used in biogas piping system in biogas projects,to stop flame spreading in the pipes.Chief proprty and specification:
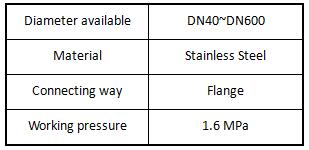
Pressure Regulator
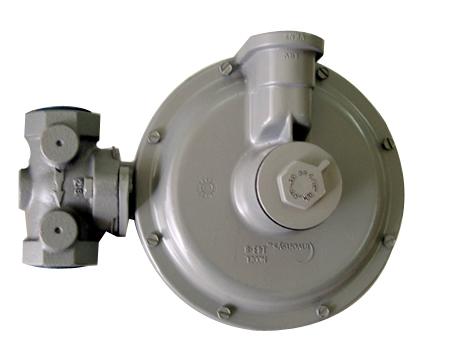
Nombre:
Regulador de presión de biogásSolicitud:
Se utiliza para regular o reducir la presión del biogás, adecuada para la generación de energía.Jefe de propiedad y especificación:
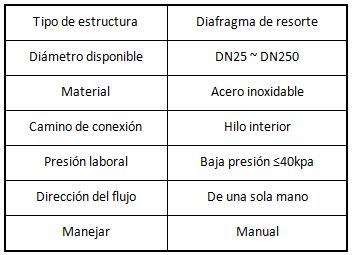